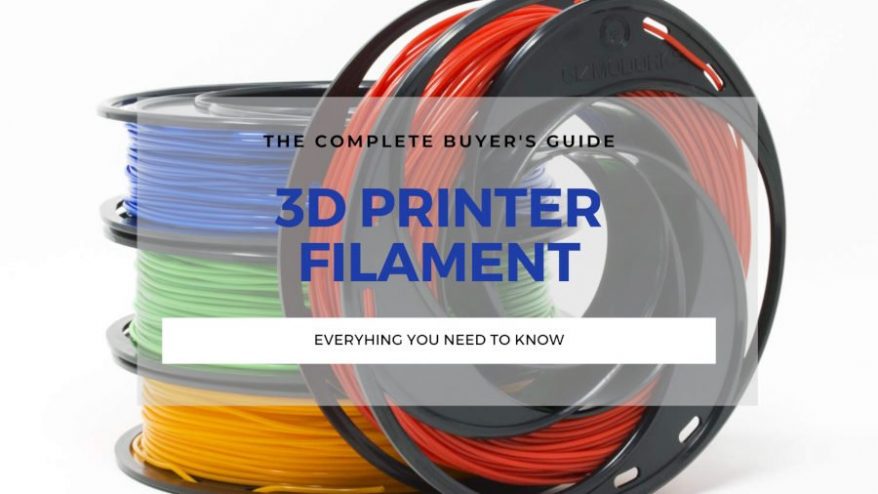
If you’ve just bought yourself an FDM 3D printer, then you’re almost ready to start printing to your heart’s content – you just need the materials. These 3D printer filament materials are simply melted and extruded from your 3D printer’s extruder, and then printed to create your chosen model.
But which filament is best for you?
- What is 3D printer filament?
- 3D Printer Filament Types
- Hobbyist 3D Printer Filaments
- PLA (Polylactic Acid)
- ABS (Acrylonitrile Butadiene Styrene)
- PETG filament (Polyethylene Terephthalate with added Glycol)
- Flexible 3D printer filaments — TPU, TPE, TPC
- Nylon filament (Polyamide)
- Support Filaments
- Composite Filaments
- Professional 3D printer filaments
- PC filament (Polycarbonate)
- ASA (Acrylonitrile Styrene Acrylate)
- PP (Polypropylene)
- PEEK filament (Poly Ether Etherketone)
- Other filaments
What is 3D printer filament?
Filaments come on spools, making them easy to feed into your 3D printer. Filaments are plastic materials in spaghetti-like strands that are melted and extruded onto your printer’s print bed to make your 3D model according to the specs you chose in your 3D software.
3D Printer Filament Types
There are two main types:
- 1.75mm filament: the 1.75mm size is by far the most common, and is the smaller diameter of filament available.
- 2.85mm filament: sometimes referred to as 3mm filament, 2.85mm filament appears to be going increasingly out of fashion with makers drawn to 1.75mm filament instead. However, some printers including BCN3D Sigma printers and Ultimaker’s range of 3D printers take 2.85mm filament, including the Ultimaker 3, S3 and S5.
What is the best 3D printer filament?
Well, it depends. If you’re a beginner to 3D printing, then ABS or PLA are your best bet, with PLA considered the easiest filament to 3D print with overall. PETG is considered a good middle ground between ABS and PLA, which is explained in more detail in each 3D printer filament type section below.
If you’re looking to print crazy glow-in-the-dark, clear or conductive models, there are PLA blends with all of these attributes. PLA is considered the most versatile filament, and clear PLA filament, conductive PLA filaments and others are commonly used for specialized projects.
For those looking to print flexible parts, TPU, TPE and other flexible filaments exist for these uses. These are explained in more depth in their flexible filament section within this filament guide.
For experts looking to print with the strongest 3D printer filaments, PC, Nylon, Carbon fiber-filled, or even PEEK may be more appropriate — though tougher filaments cost more.
Cheap vs expensive filaments
PLA and ABS are the cheapest 3D printer filaments, starting at around $20 per kilo. PETG is only marginally more expensive, costing around $25 per kilo, and is more durable than PLA.
Tougher materials like Nylon start to get more expensive, while the most expensive 3D printer filaments such as PEEK filament can set you back hundreds of dollars per kilo. This is due to its strength, heat resistance and industrial use, which we’ll explain further later on.
3DSourced is reader-supported. When you buy through links on our site, we may earn an affiliate commission. Learn more
Hobbyist 3D Printer Filaments
PLA (Polylactic Acid)
- Temperature: 180-210°C
- Heated bed: optional at 40-60°C
- Heated chamber: not required
- Glass transition temperature: 60-65°C
- Adhesion: can use glue stick, blue painter’s tape, and more
PLA or PolyLactic Acid is the ‘go-to’ 3D filament for most makers. PLA filament is an eco-friendly biodegradable material made from cornstarch.
History:
Now probably the most widely used filament for makers worldwide, PLA is a product of the RepRap movement, with co-creator Vik Olliver discovering the material’s potential for 3D printing while trying to unearth a good filament for the first RepRap machines.
15 years later, PLA is used by millions worldwide to 3D print all types of models, and is known for being a very cheap filament as well as for being the only biodegradable filament.
3D printing tips:
It’s easy to print with because it requires some of the lowest temperature settings of any 3D printer materials and generally doesn’t warp. You’ll find PLA is also non-toxic and doesn’t smell much when printing.
Whereas 3D printer filaments like ABS and ASA are made of plastic compounds, PLA is made from renewable and biodegradable crops like corn starch. This makes PLA the undisputed eco-warrior favorite, and also means that when printing there is no foul smell or toxic fumes, unlike ABS.
Due to the purity of the raw materials used, higher quality PLA also yields better results with post-print finishing, such as sanding or drilling if required.
If you’re not sure what material to use, and just want something easy to 3D print (it’s forgiving on your slicer settings, though it can ooze and string) with respectable strength and usability – PLA is worth trying out.
It’s worth noting that PLA is typically brittle in comparison to most other durable filaments. If you need something just like regular PLA but more durable, or with higher temperature resistance, PLA+ could be your answer.
Unlike ABS, PLA does not require a heated bed when 3D printing filament, but we still recommend using one for the best results. You don’t need a heated chamber or enclosed build area, making it a favorite of DIY 3D printer owners that typically have open print areas.
We recommend the following PLA selections:
There are a large range of PLA filaments available, with a huge variety in quality and strengths. Generally, it’s considered weaker than ABS – but higher quality 3D printer PLA can result in a surprising amount of finished part strength.
There are a huge number of different filament blends available. Common blends include wood filaments, as well as copper PLA and carbon fiber filament — you can even get glow-in-the-dark PLA for nighttime projects.
However, PLA melts at far lower temperatures than filaments like ABS, making PLA parts far less suited to high-temperature applications. PLA is also brittle, and if enough pressure is placed on a PLA part it can snap. It can’t be acetone-smoothed like ABS, though it is very easy to paint your finished parts, and gluing multiple PLA parts together is also no problem.
Read our full guide: PLA 3D printer filament guide
Best filaments: Best PLA filaments
ABS (Acrylonitrile Butadiene Styrene)
- Temperature: 230-250°C
- Heated bed: required, recommended temperature 90-110°C
- Heated chamber: highly advised
- Glass transition temperature: around 105°C
- Adhesion: glue stick, blue painter’s tape and others
Perhaps the second most commonly used filament is ABS (or Acrylonitrile Butadiene Styrene on Sundays) – it’s a common plastic used in a lot of casings and consumer products that require a durable material. Your phone case or keyboard is likely made from, or has some components in ABS.
Good ABS filament is stronger than good PLA (and considerably stronger than cheaper varieties) and has a higher temperature resistance (it won’t go soft in a hot car on a sunny day) but takes a little more care when printing. Cheaper ABS can be crumbly or inconsistent to print.
As well as being one of the most widely used 3D printer filaments, it’s also one of the most versatile, available in many different colors and sizes — you can even buy clear ABS to paint after printing. ABS also has good heat resistance, with a glass transition temperature of around 105C — far higher than filaments like PLA (60-65C).
It is also cheap, costing around $20 per kilo, and as a result is commonly used for rapid prototyping.
3D printing tips:
This is because it has a tendency to warp if your heated bed is not hot enough (as it contracts when cooling), and requires a hotter extruder temperature. However, once your ABS plastic filament settings are tuned in and everything is at the correct temp – printing it is no harder than any other material.
This material can also be smoothed with acetone. This means you can make it look more like a non-3D print, but that’s usually at a cost to detail.
As with all 3D printing filaments, it’s extremely important to only print in a well-ventilated area. ABS is no different. The very process of printing can release microparticles into the air during the heating and extruding process – so always read the guidelines from your printer’s manufacturer.
ABS filament requires a heated bed, and preferably a heated chamber — so RepRap 3D printers and 3D printer kits may struggle. Without a heated chamber ABS may warp and pull upward at the corners, and the midsection may even crack if the warping pulls two areas apart. It can also smell bad when printing, with pungent odors that can cause nausea — so it is best to 3D print ABS filament in a room you don’t need to use.
Is ABS filament transparent?
Not naturally, like PLA and some other materials (see below) but we do a modified ABS that is, also it prints more translucent unless you acetone smooth.
- We also have a full, in-depth guide dedicated to ABS filament.
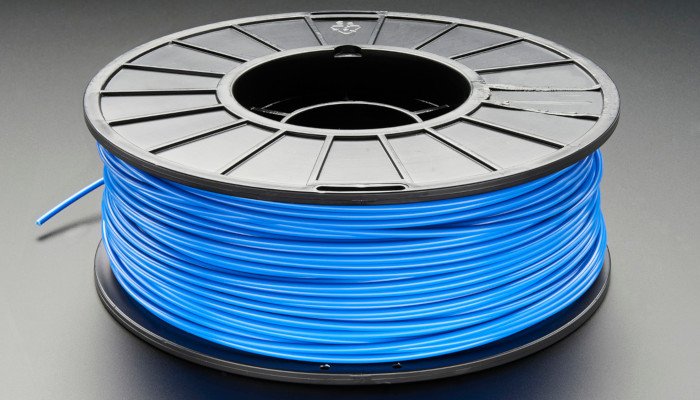
We recommend the following ABS selections:
However, for the price there aren’t any stronger filaments or more durable filaments than ABS. Nylon is tough but more expensive, and PEEK is more than 10x pricier. Therefore, ABS is perfect for anyone looking to create sturdy and high-quality parts without breaking the bank.
For more info on ABS:
PETG filament (Polyethylene Terephthalate with added Glycol)
- Temperature: 220-245°C
- Heated bed: optional but recommended, at 70-90°C
- Glass transition temperature: around 80°C
- Adhesion: blue painter’s tape and other options
- Density: 1270kg/m³
PETG is PET with added glycol in order to improve its 3D printing characteristics. PET is widely used to make water bottles as well as in injection molding, with glycol added to make it less brittle and improve impact resistance and durability.
It is effectively almost unbreakable – layer adhesion is excellent and it will just keep bending, rather than snapping like more brittle plastics might.
Other benefits include hardly any warp and virtually no smells when printing. It also bridges well. When printed optimally for transparency, PET is one of the clearest.
3D printing tips:
Although easy to print with, you want to make sure your PETG filament settings are dialed in properly.
The main advantages of PETG filament are that it has good impact resistance and fantastic thermal characteristics but without the problems with warping associated with ABS or brittleness associated with PLA.
For these reasons, PETG is considered a stellar third option for those deciding between PLA and ABS, and is becoming an increasingly popular filament.
Possibly the main advantage of PETG however is how great layer adhesion is during 3D printing. It’s natural stickiness makes for fantastic layer adhesion, leading to strong and durable parts that do not warp — this makes PETG one of the best 3D printer filaments for long and thin parts that are a nightmare for ABS.
We recommend the following PETG selections:
However, PETG’s softer surface makes it prone to wear and tear from general scratching, and is therefore not an ideal material for any application that involves heavy use or that needs to retain a certain surface finish.
Additionally, PETG’s great layer adhesion has some downsides. It sticks so well that it is a poor option for printing supports, bridges, and other structures. For this reason, PETG is less of an attractive option unless you have a dual extruder 3D printer and can print a better support filament such as PVA or PLA. You should also be wary of stringing, and correct your 3D slicer settings if you notice excessive oozing.
For a more in-depth guide to PETG 3D printing:
Flexible 3D printer filaments — TPU, TPE, TPC
- Recommended extruder temperature: 220-260°C depending on the flexible filament type
- Heated bed: optional, recommended temperature 40-60°C
TPE — or Thermoplastic Elastomers — blend plastics and rubber together to create this special type of flexible 3D printer filament. These filaments are flexible and elastic — far more so than other flexible 3D printer filaments like PLA.
Flexible filaments are any material that can be easily bent out of shape, and then returns to it’s original (post printed) shape once released. These are different, but share similarities to semi-flexible, extremely durable materials like PETG and Nylon.
Flexi filaments have various vibration dampening, impact absorbing and shape restoring properties. Excellent uses involved model car tyres (or tank tracks), bouncy objects and custom printed stress balls – but the uses are limitless.
They’re available in different hardnesses, often referred to on the Shore D hardness scale. Lower numbers are softer, and higher are firmer materials.
It is commonly advised when 3D printing soft material to do so at half the usual speed, at around 20-30mm/s, at least to start with. You may also want to check the extruder you use is compatible with flexible materials – as some extruder designs can cause problems, especially with softer grades of flex.
- We have a specialized article focused on TPU if you want to find out more about TPU filament.
- For TPE and other flexible filaments, we have an article explaining every type of flexible filament.
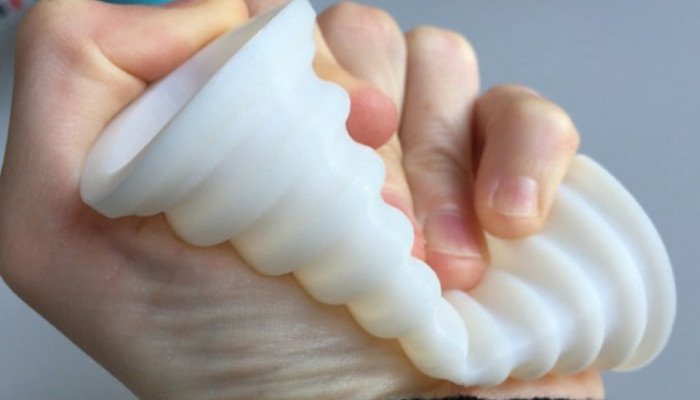
There are several different types of TPE, the most popular being TPU (Thermoplastic Polyurethane). These flexible 3D printer filaments are great for absorbing shocks, as well as dampening vibrations.
They also have very good heat resistance properties, making TPU and other flexible filaments perfect for creating less rigid tools that can withstand high temperatures. When printing with TPE or TPU, you’ll notice it has fairly similar characteristics to PLA.
We recommend the following flexibles:
However, TPE can be difficult to print, and considerable care must be taken to maintain precise print settings, or the print could fail. TPU and other flexibles are also prone to small imperfections on printed models through stringing and oozing.
Additionally, extra care should be taken if using a Bowden extruder, as the longer feed lengths can cause jams.
For more info:
- The best TPU and flexible filaments
- Complete guide to TPU filament 3D printing
- Guide to flexible filaments
Nylon filament (Polyamide)
- Temperature: 240-275°C, generally around 250°C
- Heated bed temperature: 90-110°C
- Does Nylon require a heated chamber: Yes
Nylon is a form of Polyamide, with Nylon filament known for being very tough, heat and impact resistant, and difficult to scratch or wear down. As a result, not only is Nylon filament used in some maker projects, but is used heavily in industrial 3D printing situations for rapid prototyping and other uses, and Nylon PA12 powder is also used in SLS 3D printers and in MJF.
This is, hands down in our opinion the most versatile printing material currently available. It’s an amazingly strong filament. Outside the 3D printing world it’s commonly used in clothing, when printed thinly its flexible (think living hinges) and when printed thick it’s got a good level of stiffness to it.
Ultimately Nylon is very durable, has a low friction coefficient (often used in low RPM gearboxes and bushings) and in our Nylon 12 blend has an increased resistance to chemical and thermal influences than the more common grades such as Nylon 6. It is these properties that make Nylon so suitable for blending with other materials to create filament types with a range of excellent benefits.
3D printing tips:
You will absolutely need a heated bed as well as a heated chamber to 3D print Nylon filament. Without these additions, Nylon will warp and parts will be rendered useless. Therefore, use a heated bed as well as an enclosure or heated chamber to keep a steady temperature maintained, further preventing curling or warping.
Additionally, use the correct build surface for Nylon filament, such as an adhesive like glue stick, or PEI sheets or Kapton tape.
Nylon is more expensive than consumer filaments like PLA, with high-quality filaments starting at around $50 per kilo. There are several different Nylon filament types, including NylonX, which is mixed with carbon fiber, and NylonG, which is mixed with glass fibers. Both blends give Nylon added strength but cost much more than standard Nylon.
We recommend the following Nylon selections:
Nylon is considered tougher than even ABS, owing to its higher impact resistance from its flexibility. Unlike ABS, it also does not create bad odors during 3D printing. It is mainly used for its fantastic strength, impact resistance and flexibility.
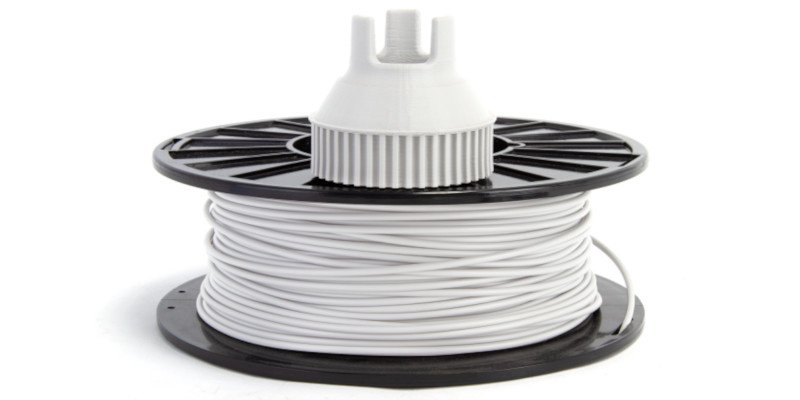
However, Nylon’s proneness to warping and curling mean you must be very careful when 3D printing. Keep precise print settings to ensure your print doesn’t warp and fail, and do not attempt to 3D print Nylon without a good heated bed and chamber.
Nylon is also very hygroscopic and requires airtight storage in a dry place or its 3D printing characteristics will drastically worsen.
For more info on Nylon:
Support Filaments
PVA (Polyvinyl Alcohol)
- Temperature: 190-210°C
- Bed temperature: max 45°C
- Adhesion: blue painter’s tape (and others suitable)
PVA is probably best known for its ability to be dissolved water, and it is therefore often used as a support material in geometrically complex prints alongside PLA. It’s used with PLA as the two materials share similar melting points and print characteristics.
It is perfect for these prints as its solubility means that leaving a print overnight in water completely removes the PVA supports, leaving no trace or blemishes that would otherwise affect the quality of the print.
We recommend the following PVA support filament selections:
If necessary, PVA can also be used to print models, rather than just as a support filament. It is however not ideal for this, as like PC it absorbs moisture from the air, and any contact with water will spell doom for your part. It therefore requires 3D printer filament storage to retain its properties.
Moreover, PVA is liable to clog the 3D printer’s nozzle when printing if left hot without extruding any 3D printer filament. It’s also expensive, which may be a barrier considering it cannot be used for any product intended to be taken outside.
It’s worth considering though it’s extremely hygroscopic – that means you’ve got to keep it dry and sealed with desiccant to preserve it
For more information, here’s our full guide to PVA filament:
HIPS (High Impact Polystyrene)
- Temperature: 230-245°C
- Heated bed: required, recommended temperature 90-115°C
- Adhesion: blue painter’s tape, glue stick, and others also work well
HIPS is a dissolvable material mostly used as a support material when printing with ABS. The main advantage of using HIPS with your ABS 3D printer filament is that after printing, simply leave your model in Limonene to dissolve the HIPS supports.
It’s often regarded as just a support material, which it works as very well. However, it also works great as a standalone printing filament due to the fact it’s easy to print and generally regarded as quite strong and low warp.
In fact, it will actually print nicely as a higher impact alternative to PLA.
HIPS is a copolymer combining the hardness of polystyrene with the elasticity of polybutadiene rubber to create a high-impact thermoplastic that’s pretty tough and strong – without the typical brittle properties.
It’s for this reason alone we feel HIPS filament is a really underrated 3D printing material in its own right.
As a support material, HIPS dissolves using Limonene solution – which is an easily obtained solvent that’s made from the skin of lemons. Once submerged for 24 hours, the HIPS will have dissolved and you’ll be left with the print with clean, crisp overhangs, and no evidence of any supports or any imperfections.

Having similar properties to ABS, it’s perfect for use with a dual extruder 3D printer, and its light weight means it’s well suited to parts where cutting weight is the aim.
Moreover, HIPS is cheap, and though dissolvable in Limonene, it is still water-resistant. It’s stronger than standard polystyrene, and possesses good mechanical and strength characteristics, leading to its use in plastic signs and point of sale displays.
We recommend the following HIPS selections:
However, as with ABS, HIPS requires the use of a heated bed, and high temperatures are recommended along with a heated chamber with ventilation. HIPS 3D printer filament is liable to warp, so careful monitoring of temperature is required to avoid visible and rough looking layers.
Likewise, as with ABS it exudes strong fumes, and is guilty of clogging up the 3D printer nozzle which can waste time and material.
Read our full guide to HIPS filament here:
Composite Filaments
Wood filaments
- Extruder temperature: 180-220°C
- Heated bed temperature: optional 40-60°C
- Do you need a heated chamber or enclosure to 3D print wood? No.
Relatively new developments in 3D printing have made it possible to print beautifully finished wood models on even the most budget-friendly 3D printers!
These wood filaments are typically a mix of 70% PLA, and 30% wood elements, such as pine, bamboo, and other woods. These filaments give an authentic wooden sheen to your models, letting you create precise wood models that look almost identical to the real thing — only very close inspection will reveal the truth.
Beyond choosing the wood type like pine or birch, you can tailor your preferred wooden finish during printing. Higher temperatures will stain the wood a darker shade, with lower temperatures the opposite. However, don’t print too high — wood is flammable.
We recommend the following wood filament ranges:
Since it’s mostly PLA, wood filaments still print at low temperatures and with relative ease, so even low cost basic printers should be able to print without too much issue. After printing, you can finish, stain and polish your prints to create gorgeous wood-like aesthetics.
Read our full guide to wood filament printing here:
Metal filaments
- Extruder temperature: 190-220°C
- Heated bed: Optional, at 40-60°C
When we say metal filaments, we don’t mean 3D printing solid metal parts in the way industrial metal 3D printers do. Rather than being full solid metal, metal filaments use a percentage of metal powders mixed with standard filaments like PLA.
The most commonly used metal filled filaments include stainless steel, bronze, and copper. However, make sure before you buy that you are indeed buying a filament with metal powder in, rather than a metal color filament.
We recommend the following metal filament ranges:
Rarely used for things metals would be used for, metal filaments are mostly an aesthetic choice, creating metallic parts that can look like real bronze statues or metal cosplay features.
They’re easily printable on even standard desktop 3D printers, but you should upgrade to a hardened steel nozzle to avoid the composite filaments repeatedly wearing down your standard brass nozzles.
You can read more in our full guide to metal filaments:
Carbon Fiber filled 3D printer filament
- Recommended extruder temperature: depends on main material.
Carbon fiber filled 3D printer filaments are those which contain short fibers infused into the original filament – such as PLA or Nylon – to give it extra strength and hardiness.
Other carbon fiber-filled filaments exist, such as PETG, ABS, and PC. Markforged, as well as releasing their first metal 3D printer recently, have pioneered FDM 3D printers that use these filaments.
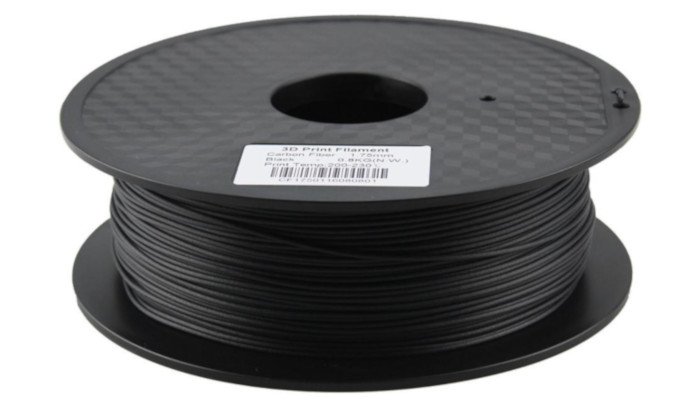
These extremely strong fibers mean 3D printed parts will be stronger, retain their shape better (as the fibers prevent shrinking), and best of all, lighter.
We recommend the following carbon fiber filaments:
- Matterhackers range of PLA and other composite carbon fiber filaments
- Dynamism range of premium carbon fiber composites
- Amazon range of carbon fiber filaments
However, the use of these carbon fibers within the 3D printer filaments can increase the chance of the printer nozzle clogging during printing.
Moreover, the filament itself is not suitable for all printers due to its enhanced properties and toughness – basic RepRap 3D printers or cheap 3D printers may struggle. Lastly, the filament becomes slightly more brittle with its enhanced strength, which may not always be ideal.
Carbon-reinforced Nylon 3D printing tips:
- Temperature: 260-275°C
- Bed temperature: 100-115°C
- Adhesion: Kapton tape
For more information, here’s our full guide to carbon fiber 3D printing:
Glass filaments
- PLA Glass temperature: 180-220C, heated bed optional at 40C+
- Glass-reinforced Nylon temperature: 255-275C, heated bed at 100-110C
Perhaps considered fragile by those who only know glass from easily shattered windows or drinking glasses that break when dropped on the floor.
In fact, glass fibers actually provide excellent strength and durability, and are added to standard filaments to notably improve their strength for prototyping and other industrial uses.
We recommend the following glass fiber filament range:
PLA glass composite filaments can be made 50% stronger, and 2x less flexible with glass additions. PLA is typically seen as brittle, with glass providing more flexibility without breaking.
NylonG, or Nylon glass composites, are also strengthened without losing Nylon’s trademark flexibility, and is used in industry for high-strength industrial prototyping and other applications.
The main benefits of this material, aside from those mentioned above,are its abrasion resistance.
Need to print something that needs to take quite a bit of rough and tumble that’s low friction and hard-wearing? Like RC helicopter landing skids, or similar (OK, so we’re not thinking very inventively right now). This could be your go-to for tough stuff.
Otherwise settings are similar to our standard Nylon 12.
For more information on glass filaments:
Professional 3D printer filaments
PC filament (Polycarbonate)
- Temperature: 300°C+
- Heated bed temperature: at least 90°C, recommended 120°C+
- Do you need a heated chamber or enclosure to 3D print polycarbonate? Yes
- Polycarbonate glass transition temperature: 150°C
- Adhesion: PEI sheets, glue stick
Polycarbonate filament is extremely strong, can take powerful impacts, and withstand very high heats. It also has a transparent finish that looks great.
PC is also lightweight, making it ideal for products that need to be clear, strong, resist heat, and light, and is a heavily used filament in engineering applications, as well as 3D printing sunglasses and riot gear – and even used with toughes glass to make it bulletproof.
- We have a full guide to PC filament in our complete Polycarbonate filament guide.
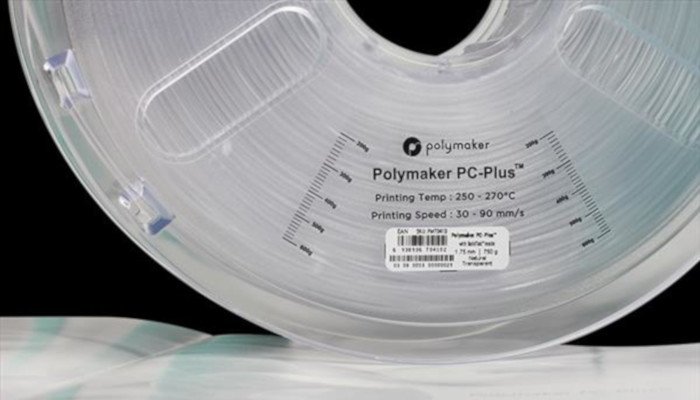
As a result of its toughness, not all 3D printers can handle PC filament, because your hot-end needs to run at around 260-300°C for it to print nicely.
One of the benefits of such a high printing temperature though is its thermo-stability – polycarbonate filament takes a bit of heat to soften it up. But that’s not to say it’s brittle when cold, far from it. This thermoplastic is also durable and takes quite a force to break it.
Another interesting quality of Polycarbonate is that it is not strictly rigid but slightly bendy, meaning it can move flexibly without snapping or breaking with high tensile strength. This makes it useful in areas where flexibility is a necessity. Moreover, PC’s ability to retain its structure until around 150°C makes it ideal for use where high temperatures are involved.
We recommend the following PC filament selections:
However, as a result of these strong heat properties, very high temperatures are required to print the 3D printer filament. As it is difficult to prevent the rapid cooling of the part from these high temperatures, PC is very prone to warping – from small temperature deviations, or in the event of too much cooling – therefore requiring a specialized cooling chamber with heated bed.
Polycarbonate is also very hygroscopic and if not stored correctly will deteriorate as it absorbs moisture from the air. We explain how to store and dry affected filament in our PC filament guide below:
ASA (Acrylonitrile Styrene Acrylate)
- Temperature: 230-250°C.
- Heated bed: required, recommended temperature 90-100°C.
- Adhesion: Blue Painters Tape / Glue Stick / PEI Sheet
ASA is a 3D printer filament with good impact resistance as well as being resistant to heat and scratching. However, due to the different rubber material used to produce ASA, it is more expensive than standard 3D printer filaments.
Acrylonitrile Styrene Acrylate is a specialist material, which is new on the scene. It’s very similar to ABS, but with one key difference – it’s resistant to UV light. That means it won’t crack or yellow when left out in the sun over time. If you print practical outdoorsy things, or print for business this printing material is invaluable.
3D printing tips:
ASA filament otherwise has similar properties to ABS — it’s slightly denser, slightly more durable, and harder wearing. If you’d like to learn more about the differences between this and regular ABS filament, check out our comparison article.
Something to note when printing ASA though is that it needs to cool really slowly, or it can crack. This is easily solved by turning your cooling fans right down, to about 5% or 10%.
If you have an enclosed printing chamber, that’s even better – but otherwise, try keep the ambient temperature warm and no drafts and your prints will come out a dream.
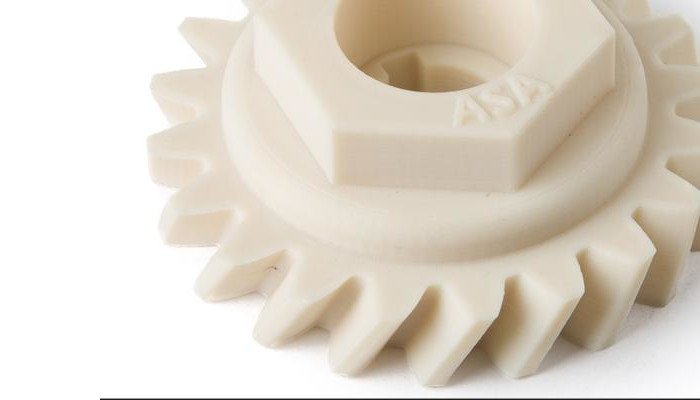
We recommend these ASA filament ranges:
In addition, this new material composition means it requires a high extruder temperature with recommended ventilation to counteract the fumes produced melting it. A heated bed is also highly recommended to prevent the warping that can be more unpredictable with ASA than some other filaments.
Read our full guide to ASA here:
PP (Polypropylene)
- Recommended extruder temperature: 220-250°C
- Heated bed: 85-95°C
PP is another semi flexible 3D printer filament like PC, and is very lightweight. It however lacks some of the strength of PC, and is therefore used mostly in low strength applications where its flexibility is needed, such as in making ropes, stationery, and in the automotive and textiles sectors. It is also a main material used in injection molding.
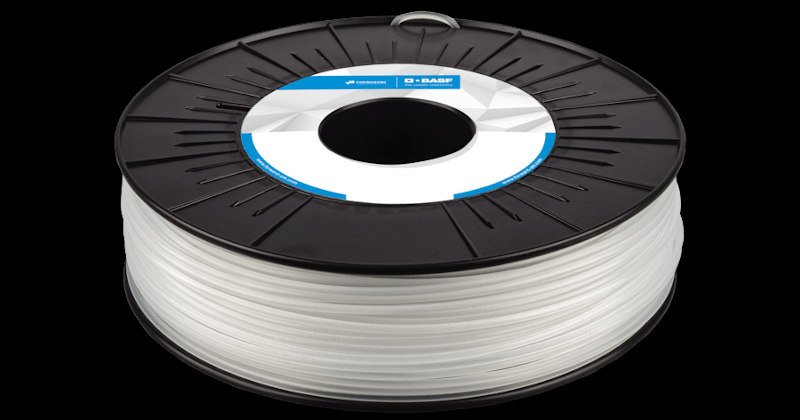
PP is useful in 3D printing as it is both impact resistant and fatigue resistant. This makes it perfect for parts that need to be able to absorb shocks, and its scratch resistance comes in handy here too.
We recommend the following PP filament ranges:
- Matterhackers range of PP filaments
- Dynamism Polypropylene filament range
- Range of Amazon Polypropylene filaments
However, PP lacks the strength necessary in many industries, ruling it out for many applications. It is also liable to warping during printing, and is also relatively expensive. Moreover, if you want to customize your model post print, PP is not a good option due to its low solubility for different colored dyes.
PEEK filament (Poly Ether Etherketone)
- PEEK 3D printing temperature: 360-450°C
- Heated bed: 120-160°C
- Do you need an enclosure or heated chamber when 3D printing PEEK? Yes.
- PEEK glass transition temperature: 143°C
PEEK is a very strong plastic that, due to its phenomenal thermal resistance (melts at 343C), requires extremely high temperatures to print. It’s a high grade, industrial material that offers the same strength by volume as steel, despite being 80% lighter. As a result, PEEK is seeing increased use in aerospace and automotive parts to save weight.

In addition to its use in the aerospace industry, PEEK has uses in high fashion 3D printed shoes, as well as wide use in the medical sector to create dental instruments, lightweight prosthetics, and implants as an alternative to standard metal implants. This is because PEEK doesn’t react to boiling water or steam, making it an ideal filament for areas where sterilization is required.
Absolutely not a consumer 3D printer filament, PEEK is reserved for high value-added industrial applications — though if in future prices come down it could see more day-to-day use. It is favored for its extremely high strength, fantastic temperature and chemical resistance, and low weight.
We recommend the following PEEK filament selections:
However, these advantages don’t come cheap, and PEEK is certainly far from inexpensive. Expect to pay around $500/kg, sometimes up to even $700. Moreover, it requires these very high temperatures to print, meaning that only industrial 3D printers can print it effectively, no cheap DIY 3D printer kit machines are likely to cut it.
Even small deviations in printing conditions can create imperfections in PEEK printed parts, so conditions must be kept very stable. Moreover, most desktop 3D printers do not come with hot ends that are able to 3D print PEEK, as they cannot handle the temperatures required.
For a more in-depth article on PEEK filament:
Other filaments
Cleaning Filament / Flushing Filament
- Temperature: 170-280°C+
Excuse us for getting personal, but you should be aware that carbon can build up in your hotend nozzle over time.
Now, if you print with the same material, at the same temperature, and your filament is always of a high quality – generally you shouldn’t need to worry about cleaning your nozzle as often. However, we would recommend it as a course of action periodically, especially if you’re a high-volume printer.
Where you’re really going to see the benefits to nozzle cleaning filament though is when you change materials – especially if you’re going from a hotter printing material to a cooler temperature one.
Let’s say you’re printing ABS at 250°C, and then take out the material to reload with PLA. PLA prints low, typically at around 180-210°C. That means, any ABS residue isn’t going to get hot enough to push out, and is going to cause friction.
Not just that, but if you increase the heat of your hotend to 250°C to flush out the ABS with PLA, you risk cooking, or burning the PLA. Which can also clog your nozzle, so for best results, use Floss between 205-210°C to clean out PLA.
Therefore, cleaning filament works perfectly as a flushing filament to use between material changes (and once in a while even if you don’t change) – to keep your nozzle clear and blockage-free.
What’s more, it only takes 30 seconds per clean making it a real time saver.
PMMA (Acrylic Filament)
- Temperature: 245-255°C
- Bed temperature: 100°C
- Adhesion: blue painter’s tape / glue stick
PMMA, or polymethyl methacrylate, is a hard, scratch-resistant, lightweight thermoplastic. Commonly known as acrylic, it’s well known for clarity and shatter resistance.
Not as strong as Polycarbonate, but significantly more impact resistant than glass, PMMA filament is ideal when you require something easy to print yet with excellent translucency and scratch resistance.
Think headlight lenses, aquariums and ice-rink protective glass as common uses for PMMA.
In addition, PMMA can also be acetone smoothed, similar to ABS. It’s also used for lost-wax casting, as it cleanly burns away when using as a form for a cast mold.
Related articles:
- Filament calculator – how many meters of filament on a 1kg spool
- How much can you print with 1kg filament / PLA?
- The best filament dry boxes
- Best filament storage for 3D printing
- How to dry wet 3D printer filament
- How to smooth PLA
- How to acetone smooth ABS filament
- How to join or fuse filament
- Ender 3 filament buyer’s guide (and V2 / S1)