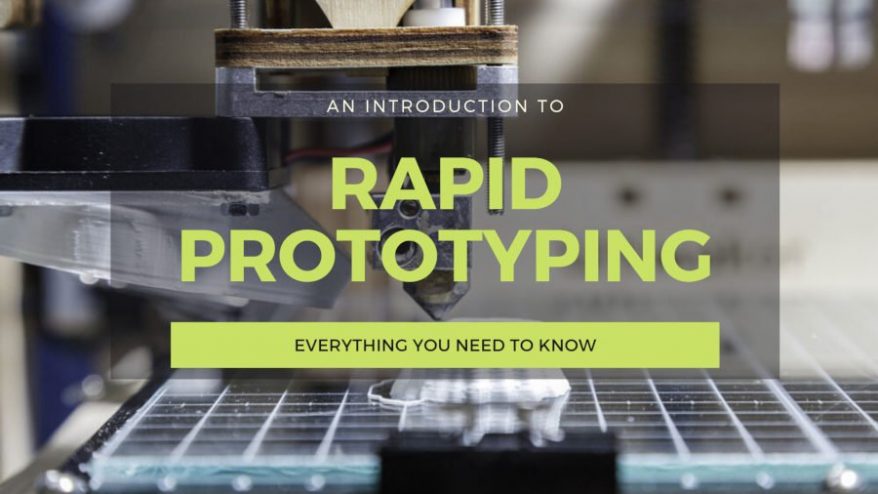
What is Rapid Prototyping 3D Printing? Everything You Need To Know
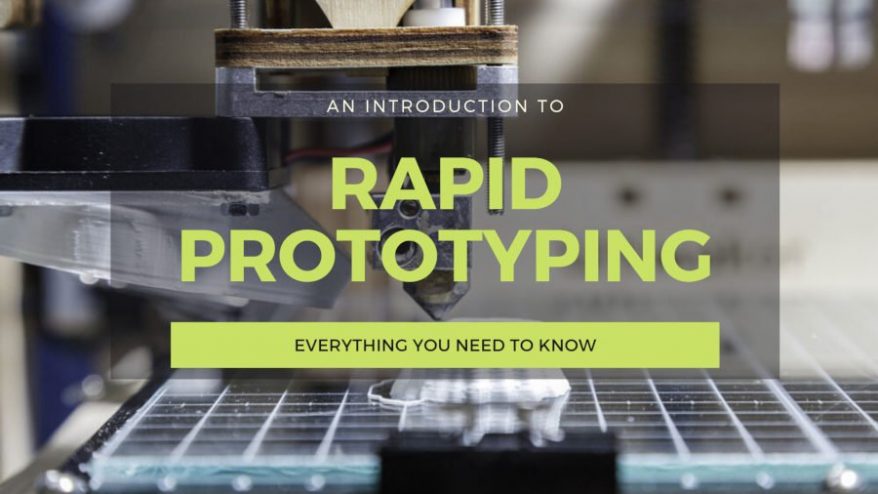
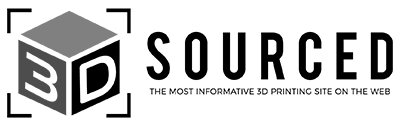
At 3DSourced we’ve covered everything 3D printing and 3D since 2017. Our team has interviewed the most innovative 3D printing experts, tested and reviewed more than 20 of the most popular 3D printers and 3D scanners to give our honest recommendations, and written more than 500 3D printing guides over the last 5 years.
Rapid prototyping was mainly first used in the car industry to test if new car parts were feasible back in the 1980s. Today, rapid prototyping 3D printing, as well as other methods like CNC, is more accessible than ever before and is commonly used across sectors including the automotive, aerospace and medical industries.
Using CAD software and a 3D printer, new prototypes can be printed, reviewed and improved on multiple times per day. 3D printing offers very flexible, accurate, fast and low-cost prototyping.
With the ability to evaluate and improve prototypes repeatedly until you’re completely satisfied, rapid prototyping lowers the chance of errors in the part before starting an expensive production run.

Rapid prototyping can even be done with biomaterials to create 3D bioprinted tissues that imitate real organs and structures for drug testing and other important treatments.
What is Rapid Prototyping?
The definition of rapid prototyping is using CAD programs and a machine like a 3D printer or CNC mill to quickly produce prototypes, test them for shape or function, and tweak or iterate based on the feedback, so you can then print the next prototype and test it.
Rapid prototyping is the name that encompasses all the technologies and techniques involved in creating viable prototypes in record time, to review and refine designs.
Rapid prototyping means that you can quickly get a physical product in your hand, which is far better and easier to analyze than a CAD design on a computer screen.
High fidelity vs low fidelity rapid prototypes
There are two main forms of prototyping:
- High fidelity prototype – one that is close in appearance and function to the final design. With the additional testing you can conduct on a physical prototype you can find all flaws before investing in a full manufacturing run. It is much easier to verify a high fidelity prototype’s design, fit, and function before either buying the prototyping machines or outsourcing production.
- Low fidelity prototype (concept models) — focused on helping designers validate their ideas, and for testing aesthetics. Concept models are also useful for showing the concept to stakeholders, decision-makers and customers, getting feedback on the design and communicating the design far better than if they were just shown a CAD design.
If you’re looking to purchase a 3D printer for rapid prototyping, we may be able to help:
*One of our trusted partners will be in touch following a quote request.
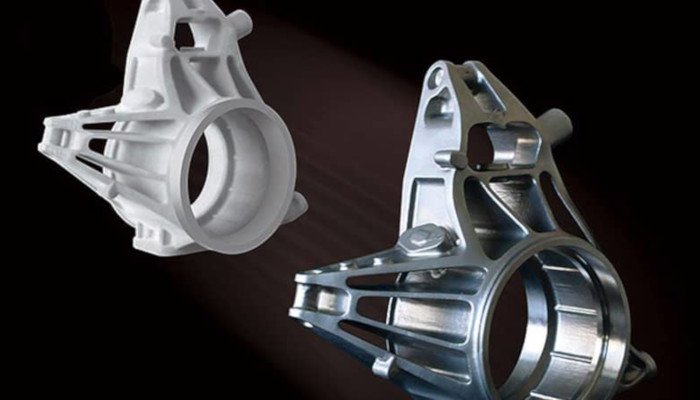
The Rapid Prototyping Process
The process can be divided into three main phases: printing, reviewing and refining.
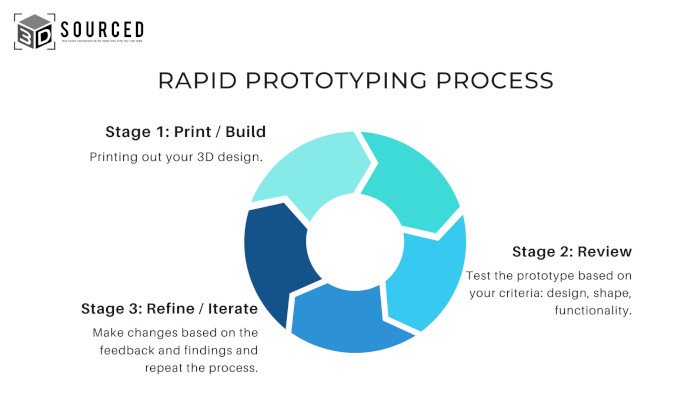
Before you can 3D print your final prototype, you need a design. The 3D CAD design file of a scale model of your final product can then be imported into a 3D slicer to be sliced into layers before printing it. Sometimes 3D scanning is also used to create a model of the part to be iterated on, such as a 3D printed car part.
Read more: best product design software tools
Typically new product development engineers and designers will:
Rapid Prototyping 3D Printing Process
3D print the designed part overnight
Prototypes can take hours to print, especially if you require smaller layer heights and better precision, or your prototype is large.
Test the prototype for form or function
The prototype is tested for shape, color and aesthetics if a cosmetic model, or testing function such as the prototype’s heat or impact resistance. Feedback is gained based on the test results.
Rapidly iterate based on the feedback
Make changes to the CAD file based on the feedback and tweak everything in preparation for 3D printing the next iteration overnight again.
CNC milling is also occasionally used, but for individual, custom pieces, 3D printing holds several key advantages. 3D printing is an additive manufacturing technology, so only the materials needed for the design are used. On the other hand, CNC milling is subtractive, removing excess material until you reach a final design. This uses up additional materials and requires more cleaning up afterwards.

The functionality of the part printed depends on your needs. If you only need to evaluate the design, you may not need the part to be able to perform any part of its functions – so may not need to print it in metal but in plastic instead.
Some high quality, industrial-standard filaments we recommend for FDM rapid prototyping:
Once the part has been printed, you can decide if the prototype is fit for purpose and whether it is good enough to go ahead and start manufacturing. If not, tweaks can be made based on the findings to create the next iteration, and the next prototype can be quickly 3D printed.
Rapid prototyping machines and options: 3D printers & CNC
SLA prototyping
SLA, or stereolithography, is ideal for concept models, cosmetic prototypes and designs with complex geometries, and concept models for presenting clients and decision-makers. SLA is one of the most accurate rapid prototyping technologies, capable of smooth surface finishes with barely visible layer lines. Coupled with its affordable cost, SLA rapid prototyping makes great aesthetic prototypes to test shape, design and size — and they’re great for showing clients or upper management.
However, the resin parts created are weak to UV and so cannot be left or used outside, and SLA parts are weaker in general than parts made using other rapid prototyping technologies and methods. SLA prototyping also has a niche use in creating masters to be used for vacuum casting, and is often used in the jewelry industry for wax investment casting, as well as in 3D printing hearing aids in the audiology industry.
- We have a full buyer’s guide for SLA 3D printers.

SLS prototyping (powder based rapid prototyping)
SLS, or selective laser sintering, prints prototypes from Nylon, though it is also used with TPU, and even PEEK powders have been recently developed. A powder based rapid prototyping method, plastic powders are sintered selectively to create the solid part.
No supports are required for SLS 3D printing prototyping as the part lies on the remaining unsintered powder, reducing the need for post-processing and leaving good surface finishes on parts. Complex geometries are possible, and SLS parts are far more resistant to wear-and-tear than SLA prototypes and therefore better suited to functional prototype testing.
It’s also great for movable components and parts with hinges or snap-fits, and parts are used in sectors such as prosthetics as they can also be biocompatible. SLS is also used to 3D print sunglasses frames, brackets, ducting, and works well as a substitute for injection molding and creating strong, functional parts.
However, SLS produces parts with a slightly grainy texture which may make it less suited to aesthetic prototypes.
- We have a full buyer’s guide for SLS 3D printers.

FDM rapid prototyping
FDM rapid prototyping, or fused deposition modeling, is by far the most affordable rapid prototyping 3D printing method, and can create relatively strong prototypes from ABS, Nylon, and various other materials for good functional testing. This mostly includes jigs / fixtures, tooling masters, prototypes for heat resistance testing and other functional testing for parts made from ABS, ASA, and sometimes even Ultem and PEEK.
Some FDM printers are dual extruder 3D printers, meaning they can print two different materials or colors of filament simultaneously, opening up a range of new design and prototyping options. They can also print supports in a soluble filament material like HIPS or PVA, so when dissolved away afterwards, you’re left with just your model and none of the imperfections that can occur during support removal.
However, most FDM 3D printers are relatively slow, parts have clear layer lines, and generally cannot match the surface finishes of SLA or SLS.
- We have a full buyer’s guide for commercial 3D printers.
- Also, we have a buyer’s guide for dual extruder 3D printers.

MJF
MJF, or Multi Jet Fusion rapid prototyping, is fast, prints tough Nylon parts suitable for functional testing and even end-use production parts, and creates some of the best surface finishes and precision of any 3D printing rapid prototyping technique.
MJF parts are considered to have better surface finishes than SLS, and it is considered the faster 3D printing process. MJF prototyping is used to create durable jigs / fixtures, brackets, vessels within the oil and gas industry, fan housings and vents, electric component housings, mechanical assemblies, and enclosures.
However, it’s expensive, and you’re limited to mostly just PA12 Nylon prototypes.

Polyjet
PolyJet rapid prototyping offers fantastic accuracy, with up to 16-micron precision as well as the versatility to 3D print multiple different materials within one part, and multiple different colors for multi-color or full color prototypes. For example, if you needed a part featuring both flexible and rigid materials in separate areas, PolyJet would be the best rapid prototyping method for you.
PolyJet is used across the automotive and aerospace industries, as well as in consumer goods and electronics, with niche applications in the medical industry creating very accurate, multi-material or color parts.
However, it suffers in a similar way to SLA in that parts are not strong enough for functional testing.

DMLS
For metal rapid prototyping, DMLS, or direct metal laser sintering, is often used to create dense, strong metal prototypes from materials including stainless steel, inconel, aluminum, cobalt chrome, titanium, and more.
A major advantage of metal prototyping 3D printing is DMLS can create internal features that CNC machining cannot, as additive manufacturing allows for these features to be created during the printing of the part, and generally DMLS is ideal for prototyping small, complex and precise metal parts, such as those with interlinking chains, and complex internal geometries. DMLS is also used to create metal aircraft parts that save weight, thereby saving fuel and keeping costs down while lowering pollution and helping save the planet.
DMLS, and generally metal 3D printing, has been adopted more for its ability to print parts that previously would have required several separate parts, to print in one single part with no welding. This makes for stronger and more reliable parts, such as in rocket engines, with space rocket companies including Relativity Space using DMLS in their prototyping. DMLS is also sometimes used in jewelry with precious metals, and for testing high temperature resistant prototypes.
However, DMLS is expensive and moderately slow, and post-processing is necessary for a finished part.
- We also have a buyer’s guide for metal 3D printers

CNC
Whereas 3D printing rapid prototyping is ideal for visual testing and aesthetics, CNC prototyping creates stronger parts that have better surface finishes than 3D printing generally. This is because whereas 3D printing uses a percentage infill for the part, for example 20%, CNC parts are solid — and therefore heavier and stronger. For functional testing, 3D printing cannot compete with solid CNC machined parts.
CNC milling is the most well-rounded and commonly used rapid prototyping machine within CNC, but grinding and turning are also used, with other CNC machines like laser cutters, plasma cutters and water jet cutters far less frequently used. Each machine has a number of interchangeable rapid prototyping tools for different uses. CNC parts are made from metals like stainless steel or aluminum, as well as industrial plastics like PLA, PC and PP, and sometimes even wood or foam.
A main reason to use CNC as a rapid prototyping machine is for the fantastic accuracy available. Though very precise prototypes cost more as the time required for these tight tolerances is higher, some machines offer incredible 0.005” or better precision. You can also rapidly iterate with materials that you can’t 3D print like wood (though wood-like filaments are available), as well as a wide variety of metals.
However, CNC prototyping is generally more expensive (especially if requiring a 5 axis CNC machine), creates more waste as it is subtractive rather than additive, and cannot create some of the geometries possible in 3D printing.

Rapid Prototyping Case Studies
Unilever Nozzles
As documented in Matthew Syed’s excellent book Black Box Thinking, Unilever had a laundry detergent production problem back in the 1970s in their factory near Liverpool, UK. The process to create washing powder involved boiling hot chemicals and forcing them through a nozzle at high pressures before separating what was to become the detergent sold in stores.
But the nozzles often clogged, blocked, and were inefficient. Production was slower, and the resulting detergent grains were of different sizes. Unilever had both efficiency problems and quality issues.
A team of biologists were let loose on the problem after a prior team of mathematicians failed to come up with a solution. They created ten new nozzles, each iteration with small differences — slightly longer, shorter, with a smaller hole or with tiny grooves. One iteration improved slightly on the original, just by 1-2%.
The team then took this slightly improved iteration and created another 10 iterations of this nozzle, making another series of small changes and testing them for effectiveness. This continued and continued as more and more prototypes were created to find marginal gains, again and again, before an ‘outstanding’ nozzle was developed after 449 failures. Whereas evolution takes tens of thousands of years, the same principles could be augmented using cutting edge technologies and new iterations can be produced every hour now with 3D printing.
3D printing wasn’t commercially available in the 1970s when this occurred, but if it were to happen in the present day, 3D printing and rapid prototyping could create the ideal nozzle in record time. Rapid prototyping allows for extremely accurate prototypes and slightly different iterations to be quickly tested, reviewed and documented. With larger parts, 3D printing ten iterations could take several days, but with small parts such as a pen lid-sized object, ten iterations could easily be produced in one print run on an SLS 3D printer. This allows for extremely quick innovation.

Rapid Prototyping Services
A number of rapid prototyping companies offer 3D printing services to meet the growing demand for 3D printed prototype parts. This offers businesses the opportunity to access 3D printing without having to pay the upfront cost of a 3D printer.
Though industrial 3D printers capable of rapid prototyping 3D printing have become far cheaper in the last few years, companies who only need to produce a few parts per year will save money by using these rapid prototyping services instead.
- View our guide to the best 3D printing services.
3D printer manufacturers such as Desktop Metal have tried to solve the issue of upfront costs with rapid prototyping machines by offering yearly rental fees. For example, their Fiber 3D printer can be rented for $3,495 per year, on a three-year contract. Some businesses may find that favorable to a large upfront cost or the continuous payments to services without ever owning a 3D printer.
Best 3D printers for rapid prototyping
There is no single best 3D printer, this all depends on the materials, size of prototype and a variety of other factors. If you need a metal 3D printed prototype, then you’ll need to choose between metal 3D printing technologies, whereas if you need a plastic part made, you have choices between FDM, SLA, SLS and others depending on the strength of part and other characteristics you are looking for.
If you want extremely smooth surface area, you may want a resin 3D printer or a part created using Multi Jet Fusion. For low cost parts and low cost 3D printers, you may prefer an FDM printer.
- We have released a free 3D printing ebook about the technologies available.

Some printers are more suited to industrial demands than others, and have become well known for their ability to create accurate parts that can be tested as functional prototypes, and do it quickly and consistently. The link below features a buyer’s guide to the best industrial printers that cost under $10,000 that provide excellent reliability, accuracy and are simple to operate.
- We recommend our guide to the best industrial 3D printers.
Rapid Prototyping Software
To create a prototype to print you’ll first need to design it on a 3D CAD software modeling tool. Depending on how complex and intricate your part is, you may be able to design it on a consumer software tool, but usually in rapid prototyping a more complete software modeling tool is required. You’ll also need a 3D slicer to slice your model before you can print it.
Sometimes a 3D scanner is used to scan an existing part that can then be 3D printed and tested. Usually however a 3D CAD design is used instead.
Rapid prototyping is also sometimes used as a term in the software industry for creating a design of a prototype of an eventual app or program, and using that early prototype to get early feedback and gauge demand, before committing to developing a full product.
We recommend reading the following guides for choosing a rapid prototyping 3D software tool:
- We list our 10 recommended professional 3D modeling software tools.
- Our guide to the best free 3D modeling software.

Advantages and disadvantages of rapid prototyping
Rapid Prototyping Advantages
- Very accurate: very intricate and precise models can be created that accurately reflect the final part. This makes it easy to evaluate the part’s shape and design.
- Reduce time to market: can test multiple iterations very quickly, and even multiple iterations concurrently. You can test multiple iterations at the same time by printing multiple, slightly different parts and evaluating which performs the task best or looks best, and further iterate on the best one. Getting to the perfect design faster can save companies huge amounts of R&D investment.
- Better design feedback: visual prototypes are better for examining than designs within a 3D software tool. You can gain a better idea of how a product will look and perform in use, and make changes based on any areas that need work. Additionally, real-life prototypes are easier to explain to upper management and to customers so they can provide their feedback.
- Instantly incorporate changes: once problems have been identified, they can be instantly changed and improved on the 3D CAD file and reprinted.
- Additive manufacturing uses less materials: especially valuable in metal part prototyping as these parts can cost hundreds of dollars each in materials alone.
- Minimize risk: rapid prototyping means you can explore and test ever potential flaw, cheaply, before starting on a large production run. You can inexpensively minimize any risks leading to any product recalls by extensively testing these prototypes.
Rapid Prototyping Disadvantages
- May require a skilled operator: metal 3D printers especially often require trained operators to ensure printing is safe and optimum. This is dependent on how complex the 3D printing technology is, as for example FDM 3D printers are far simpler and require far less skill to operate. If outsourcing to a rapid prototyping service, this will add to costs.
- Time lags and costs if not done in-house: if you have a rapid prototyping service print the part for you, this may add 2-3 days to the process as the part needs to be mailed to you. The costs may also add up over time if you print many parts, so it is important to estimate how often you will be 3D printing parts to ascertain whether it is better value to outsource rapid prototyping or have it done in-house.
- Some limitations in materials that can be used: wood, for example, cannot be properly 3D printed. You cannot 3D print rubber either.
- Expensive: especially if the entire rapid prototyping process requires dozens of iterations, and you’re using DMLS or another metal 3D printing process.