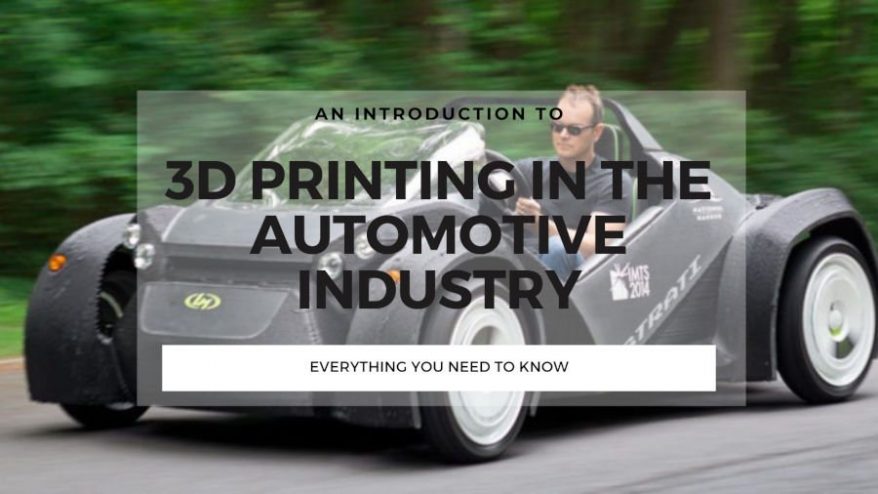
How 3D Printing is Key To The Automotive Industry’s Future
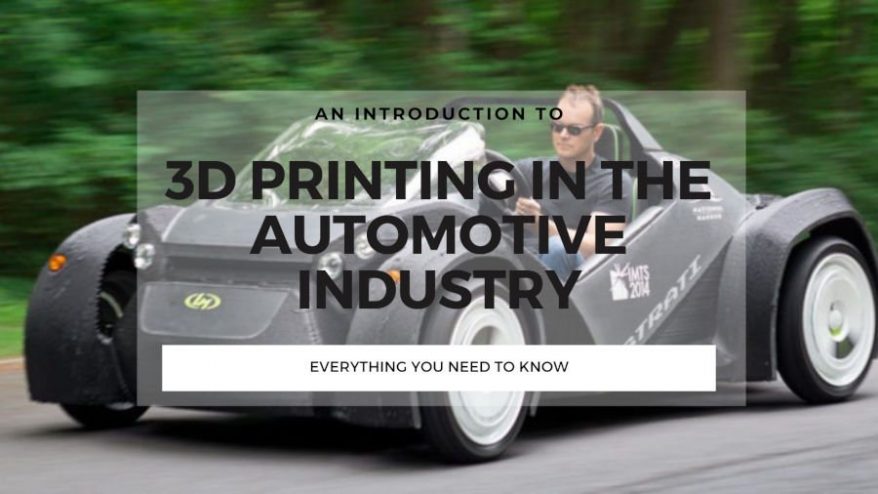
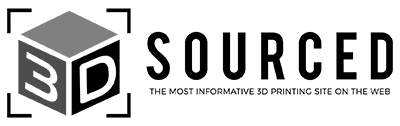
At 3DSourced we’ve covered everything 3D printing and 3D since 2017. Our team has interviewed the most innovative 3D printing experts, tested and reviewed more than 20 of the most popular 3D printers and 3D scanners to give our honest recommendations, and written more than 500 3D printing guides over the last 5 years.
While a mass-produced, fully 3D printed automotive is not yet a reality, recent strides in both 3D printing and car manufacturing have yielded exciting prospects. The advantages of 3D printing in the automotive industry allow for a faster, cheaper, and greener future.
But how exactly is 3D printing changing the creation of our roadsters? And when can we expect 3D printed cars in our garages?
- We also have a ranking of the most exciting 3D printed cars
- We also have a feature story into the uses of 3D printed car parts
Introduction to 3D Printing in the Automotive Industry
Initially, 3D printing was used by car manufacturers to quickly prototype the make and fit of various parts. By 2010, motor companies started experimenting with 3D printing fully functional car parts to be used in the manufacturing process.
Today, 3D printed car parts are widely used to both restore classic cars as well as create parts for brand new cars, with many manufacturers taking advantage of the savings in time and money compared with traditional methods.
Companies such as Renault, Porsche, VW and Bentley use 3D printing to make parts and test prototypes, having found significant benefits.
If you are interested in purchasing a 3D printer for uses in the automotive industry, we may be able to help:
*One of our trusted partners will be in touch following a quote request.
Part 1: 3D Printing used to improve popular automotives & supercars
Luxury cars and 3D printing
Street-legal and highway-ready vehicles made using 3D printed models are quickly becoming a feasible and cheaper alternative to factory-made roadsters, and can be made quicker and in a more environmentally friendly fashion.
As well as in more affordable and practical cars, many companies have been using 3D printed car accessories in their luxury vehicles since 2015. By using this cost-effective technique and high-end equipment, Bentley have been able to provide a proof of concept for the combination of both 3D printed parts and hand-designed customizations.
For example, the grill and body of the Bentley EXP 10 Speed 6, first unveiled as a concept design in 2016, are both partially 3D printed.

Porsche using 3D printing in their automotive parts
Porsche has also been investigating the advantages of 3D printing in their sports cars. Highlighting the light weight and strength of 3D printed pistons for maximum efficiency, Porsche continue to research 3D printing cars as a cost- and labor-cutting measure in mass production.
Porsche has been using 3D printing to replace rare parts in their classic line since 2018, noting that using additive manufacturing to 3D print their pistons made them 10% lighter. They have also used 3D printing to create new fixtures such as customizable sports seats.
In 2019, Porsche published their intent to use 3D printing to further prototype newer models by testing newer and more complex designs.
Rezvani Beast
Additionally, American boutique car manufacturer Rezvani revealed their Rezvani Beast car in 2014. The Rezvani Beast features 3D printed panels, mirrors, lights, and diffusers to make the high-performance vehicle lighter and improve performance. Rezvani claimed the use of 3D printing plays a big part in propelling the car to a 2.7 second 0-60mph time, a mere 0.2 seconds short of the record for commercial vehicles.
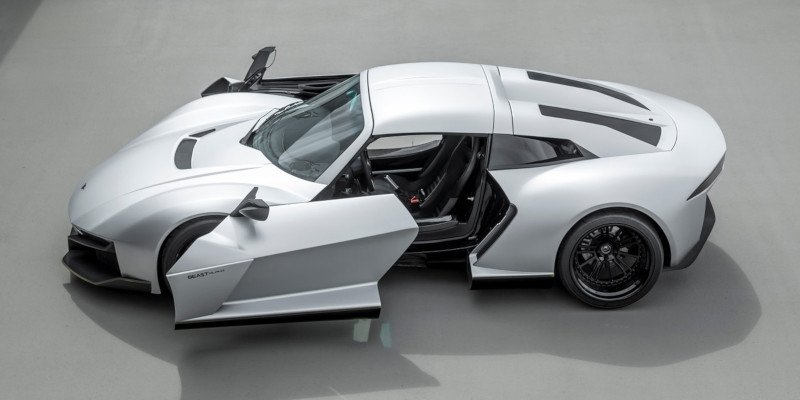
Part 2: How 3D Printing is Creating Entire Cars
Divergent Blade
As well as parts, designs for entirely 3D printed cars are also on the rise for both personal and professional use. Cars made mostly through 3D printing have been said to be ‘low-velocity’ vehicles, with maximum speeds generally around 40mph.
However, manufacturing company Divergent Microfactories claimed back in 2015 to be close to building a car capable of beating the previous record of 0-60mph in 2.2 seconds. This car was the ‘Blade’, widely referred to as the world’s first 3D printed supercar, and was officially unveiled featuring an entirely 3D printed body and chassis.
On top of saving both time and money, the Blade supercar highlights the numerous benefits of 3D printing in the automotive industry by printing parts on-site rather than importing them, and creating parts without waste, making car production far more environmentally friendly. What’s more, parts can be made to order instead of being overproduced and stocked, thereby significantly reducing both machine usage and material waste.
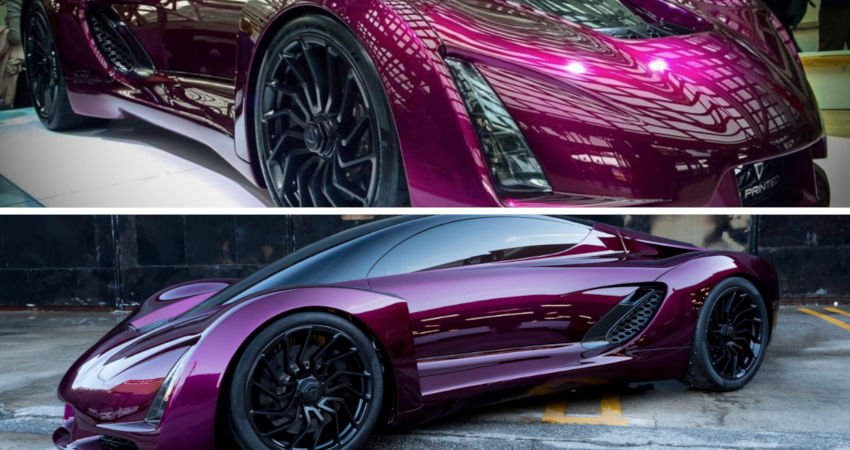
BigRep Loci
In July 2018, 3D printer company BigRep revealed their model design for the Loci, a fully customizable autonomous car produced with only 14 unique parts and made entirely using their personal line of industrial 3D printers.
BigRep further elaborated on this design in a video presentation in November 2019, demonstrating their designs and prospects for the fully electric and self-driving car, as well as planned features including wireless phone charging and automatic remote parking.
Combining the increasing interest in self-driving cars with the ever-evolving capabilities of 3D printing presents a potentially game-changing innovation in the future of urban transport.
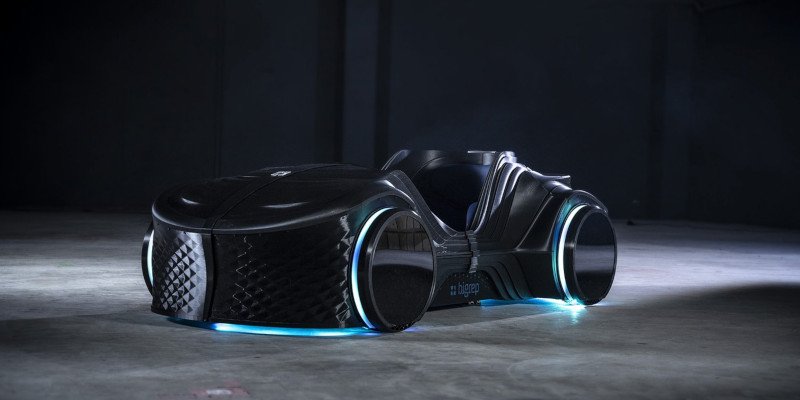
Local Motors Strati
In 2014, Arizona-based company Local Motors developed a compact car made largely of 3D printed parts, boasting a printing time of 44 hours before assembly – compared to month-long lead times for current vehicles.
The result was the Strati, a two-seat vehicle designed with the intention of future mass production. Comprised of only 49 parts, the Strati was able to prove 3D printing’s efficiency by lowering costs and hastening manufacturing time.
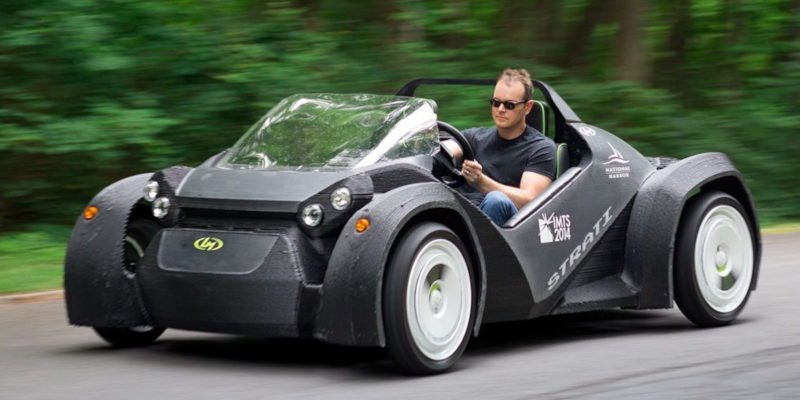
Reducing the need for outside specialists, companies save time and money while being more eco-friendly. Because parts can mostly be made on-site, 3D printed cars also reduce the need for importation, further cutting costs and reducing the industry’s carbon footprint.
As well as cars, Local Motors has also been developing the Olli, an autonomous 3D printed bus. While something of a misnomer, as the Olli has functionality closer to that of a taxi cab, the prospect of 3D printed vehicles entering the realms of public and semi-public transportation is an exciting development for the future of 3D printing in the automotive industry.
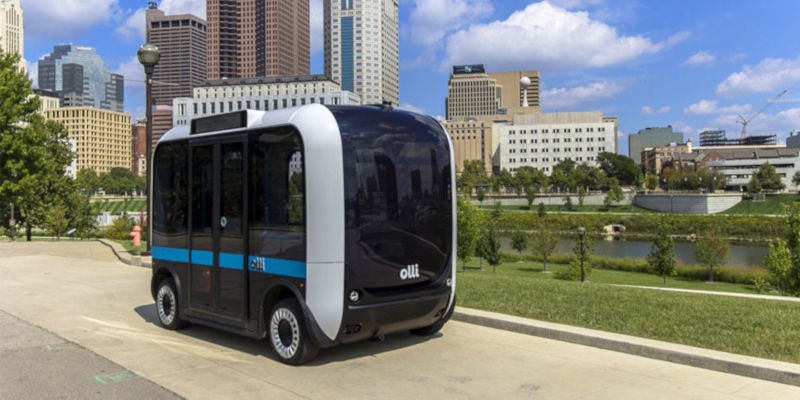
Part 3: 3D Printing in Formula 1 Cars
3D printing has been used in Formula 1 as early as 1998, when Renault purchased their first 3D printer for prototyping parts for their Formula 1 cars. 3D printed racing car frames and fixtures have been used for driver personalization as well as for performance, as lighter parts that shave milliseconds off lap times can make all the difference in a sport of such marginal gains.
As well as the body and parts of the car, interior fixtures such as seats and steering wheels have also been 3D printed to maximize vehicle control and driver performance at a much lower cost.
Formula 1 demands constant improvements to their cars to keep races exciting and their vehicles efficient. Rapid prototyping has provided a welcome boom, with 3D printed functional car parts now in regular use. In 2019, Renault reported that both of their Formula 1 cars had reached record lap times, which they attributed to the cars containing around 100 3D printed parts.
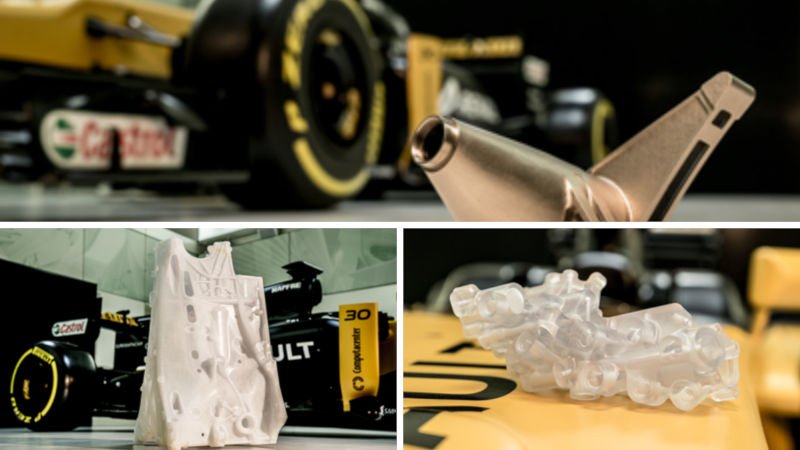
New regulations such as weight thresholds and tire sizes are often introduced in Formula 1, and the time saved in using 3D printed models means cars can be updated much faster. This gives manufacturers more time to test new or resized parts to maximize efficiency, ensuring faster lap times and faster improvements.
The same benefits can be applied to commercial vehicles to improve car efficiency. Though 3D printing is currently not fast enough to mass produce parts for consumer cars, new industrial 3D printers are becoming faster and more scalable every year. With 3D printing able to produce lighter parts that use less gas and save materials, it will also lower the carbon footprint of cars in everyday use.
Conclusion: The Future of 3D Printing in the Automotive Industry
To conclude, 3D printing complements the automotive industry well, by creating vehicles that are lighter, more customizable, and faster to build, test and repair, compared to traditional methods.
While a fully 3D printed car is not quite a reality yet, many automotive manufacturers are already integrating 3D printed car parts into their automotives, with an increasing number of parts used in consumer cars, supercars and Formula 1 racing cars. 3D printing capabilities are evolving every day, and the drive to create cheaper products with faster construction times without sacrificing performance will encourage major automotive companies to further adopt 3D printing to chase these marginal gains.
Many industry experts expect a continued boom in 3D printed automotives over the next five years, some claiming a significant increase in partially 3D printed cars by 2030. BigRep managing director Martin Back is more optimistic, claiming; ‘By the late 2020s, but I believe earlier than that, [Additive Manufacturing] will fully enable mass customization and assembly consolidation, making spare parts deliveries faster and reducing spare parts inventories while minimizing material waste.’
This year, Arno Held, the CEO of AM Ventures, stated his predictions; ‘I am convinced that by 2030, products designed and manufactured based on additive principles will be the reason why injuries heal faster and at a lower cost, why cars can drive further, batteries last longer and planes fly with much fewer emissions and I cannot wait to witness all this myself.’
With experts in both 3D printing and automotive manufacturing in agreement, the future of 3D printed cars may be brighter and closer than we think.