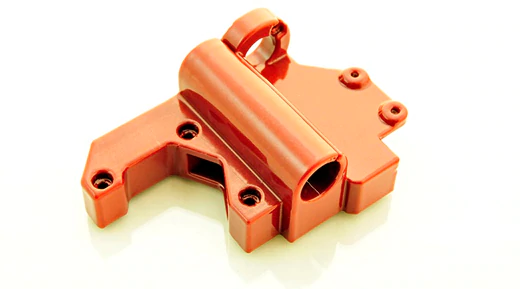
ASA and ABS Acetone Smoothing – Best Vapor Polish Method
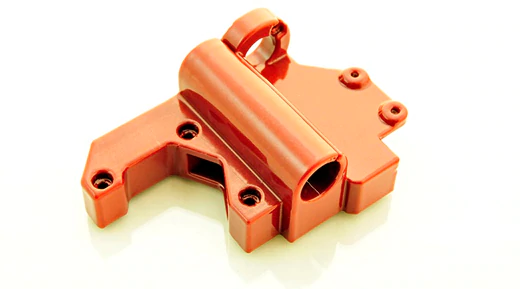
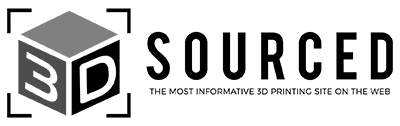
At 3DSourced we’ve covered everything 3D printing and 3D since 2017. Our team has interviewed the most innovative 3D printing experts, tested and reviewed more than 20 of the most popular 3D printers and 3D scanners to give our honest recommendations, and written more than 500 3D printing guides over the last 5 years.
FDM (FFF) 3D printers often produce a final object that while being mechanically sound, tends not to have that ‘professional look’ that you or a customer want to see.
Acetone polishing or smoothing is a safe and easy method of 3D print finishing for smoothing out surface inconsistencies without causing structural damage.
However, you need to know what you’re doing, since acetone is highly flammable and volatile!
In this guide, I will take you through the step-by-step approach to acetone smoothing of ABS and ASA, as well as discuss the differences for other filament types.
I’ll also share a few handy tips for avoiding common beginner mistakes so you can produce crisp 3D prints without the hassle – so let’s get started!
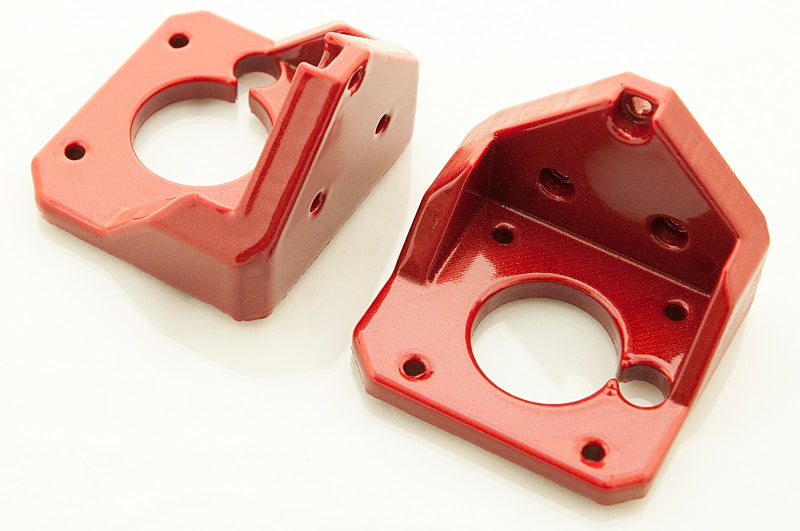
Vapor Smoothing ABS and ASA
Can I Acetone Vapor Bath my 3D Prints?
All ABS 3D prints can be acetone smoothed. Filaments that can be polished using this process are: ABS, ASA, PMMA, HIPS and Polycarbonate.
Other filament types are either unaffected by acetone or are damaged by it. If you’re looking for other 3D printing post-processing techniques, check out our PLA polishing article for details on smoothing out 3D prints that can’t be acetone smoothed.
The following photograph is of a shower tray system consisting of a frame and different color removable trays before ABS Acetone Vapour Smoothing. The frame is made of Black ABS, and all trays are made in ABS of varying colors.
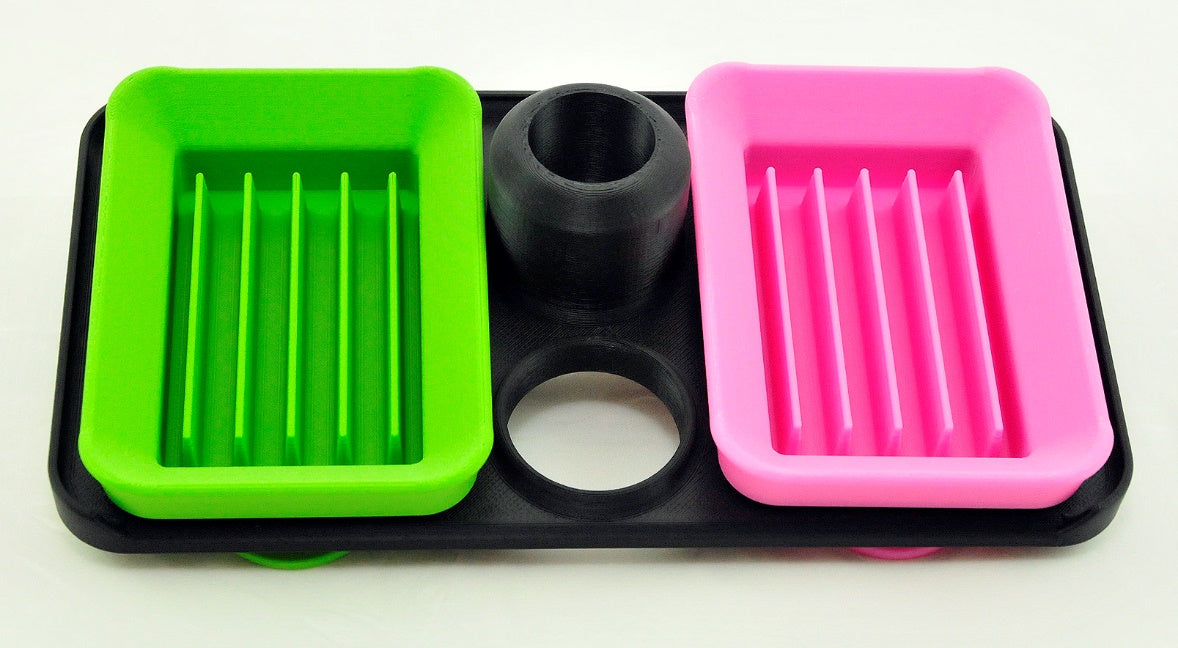
The following photograph show the same system after the ABS Vapour smoothing process.
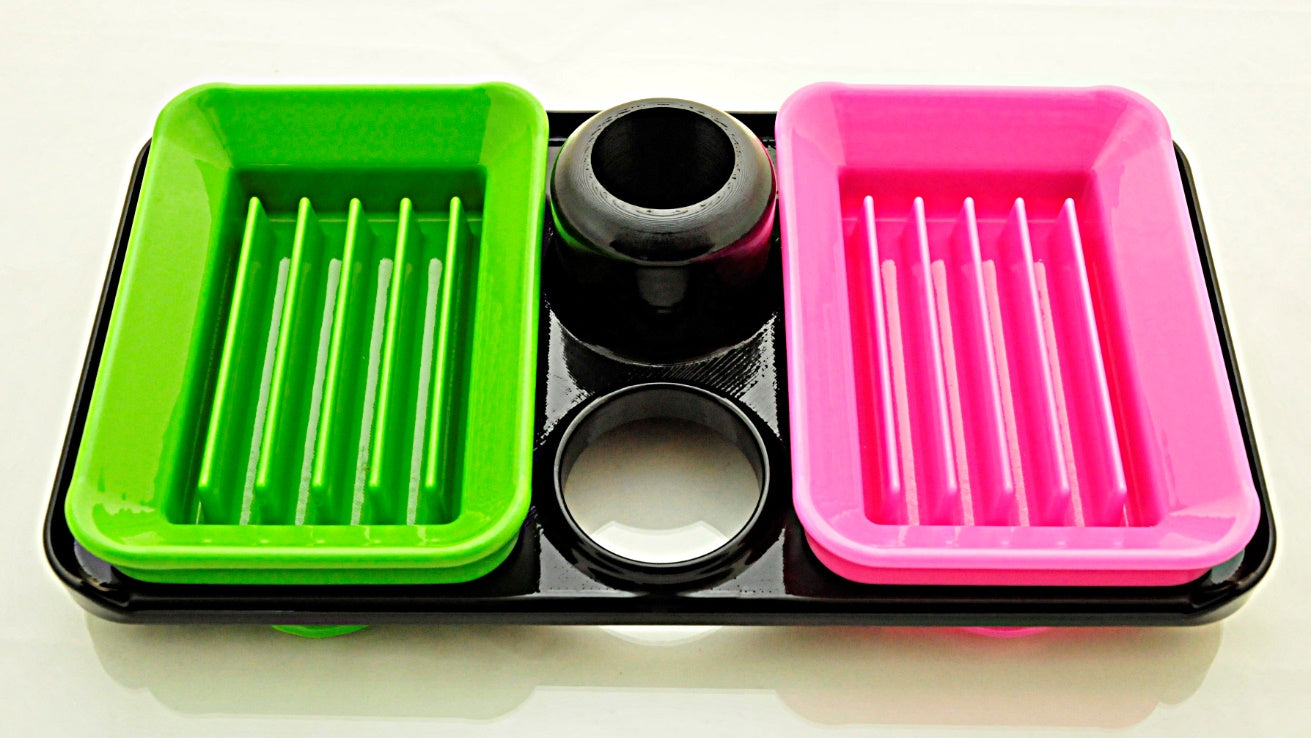
Not only do the finished parts look better, they now have a higher resistance to water ingress, and they can often be stronger than their non-polished earlier selves once fully hardened.
This is definitely our preferred method when we’re asked how to finish 3D prints – there’s just no better way to easily smooth ABS prints.
Safety Warning
Before continuing further, please make sure you acquaint yourself with the safety regulations pertaining to acetone (propan-2-one) and its use. It is your responsibility to use this solvent safely.
Obvious things to note for safety are:
- Only use in a well-ventilated area
- NO NAKED IGNITION SOURCES – acetone is extremely volatile and the vapors are Highly Flammable
- *NEVER EVER* heat the acetone!! [See above]
- Avoid breathing the fumes
- Avoid skin contact
- Keep away from animals and children
- Be careful that you do not spill any liquid onto surfaces that might be damaged by acetone – most common household plastics are susceptible to some kind of damage from liquid acetone
The Principle Behind Vapor Polishing
You can acetone smooth ABS filament & ASA filament, both with acetone liquid or as vapor.
They dissolve readily in the liquid, and a concentrated atmosphere of the vapor will eventually have the same effect. It’s that ‘eventually’ part we are interested in (and not the acetone 3D print mess you’ll be left with if you leave it too long).
We want to melt the surface of the object just enough that the surface tension of the molten plastic smooths out any surface inconsistencies and then halt the process at that point before any structural damage occurs.
In some cases, it is possible to quickly dip an object into acetone liquid to get a polished surface, but this can be very messy and gives inconsistent results.
If you use the vapors instead you have much more control over the ABS smoothing and the final results. As the vapors can get to all exposed surfaces equally, there are fewer areas of uneven melting. There are also no run-off channels or drip marks induced into the surface of the object that direct exposure to acetone liquid may cause.
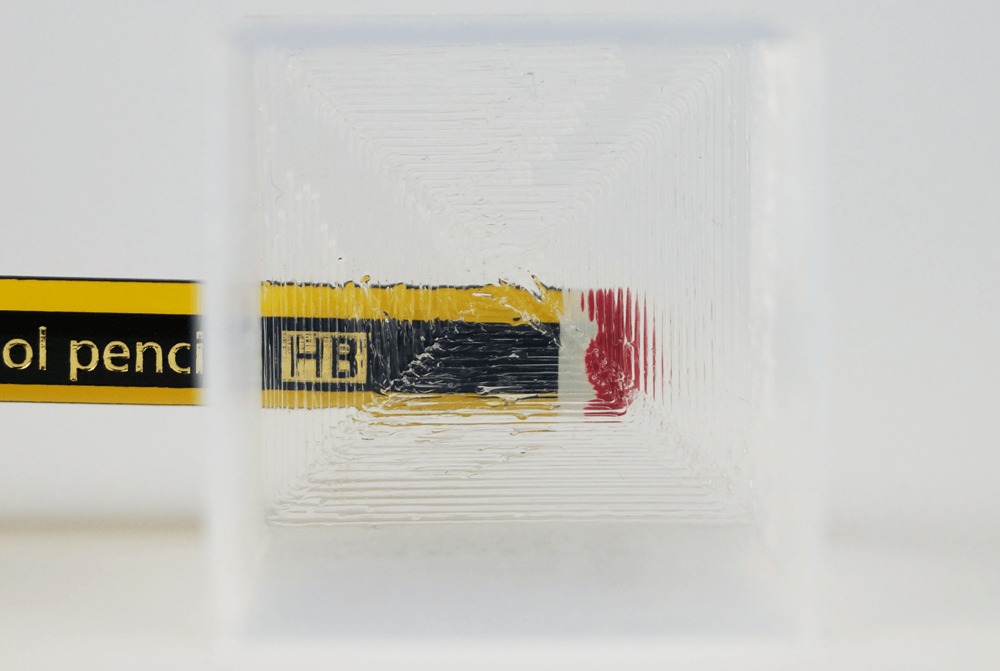
What You Will Need –
- A well-ventilated area to work that has no exposed ignition sources.
- Wear the appropriate PPE – Safety glasses/goggles, mask, gloves, etc…
- An acetone-proof container (a large glass vase or a tin) big enough to hold the parts you wish to polish – preferably with at least 30mm clearance in ALL directions around the object to be polished – top, bottom, and sides.
- A loose-fitting lid, also acetone-proof. If your lower container is not transparent, you may wish to use a sheet of glass as a lid – this removes the need to keep removing the lid in order to see how the polishing is progressing (and not letting the vapours escape or dust get in).
- A flat, non-porous plate such as glass or metal, to raise the object being polished above any liquid acetone in the bottom of the container – This really needs to be at least 10mm above the surface of any liquid acetone in the container and much larger than the object to be polished as this reduces the chances of liquid acetone creeping up the sides and onto the object itself.
- Some sheets of plastic-free kitchen roll to use as a ‘wick’ for the liquid acetone.
- Somewhere dust-free to allow the surface of the polished object(s) to harden.
- A TIMER! Seriously.
You will walk away, forget it, only to return later to find that amazing print that you were once so proud of has now turned into a hideous misshapen lump of plastic, or at worst some kind of acetone ABS mess.
It might not happen this time or the next, but it will.
Getting Started
Make sure your container is free from contaminants (this will be your acetone bath), then place a few sheets of the kitchen roll up the side and along the bottom of the container. This will allow the liquid acetone to wick up the kitchen roll, helping to produce a strong concentration of vapor at all levels within the container.
Find somewhere to work that has surfaces and materials that will not be damaged by acetone or the fumes. Acetone is a superbly-powerful solvent – you don’t want it dissolving things that you’d rather keep. It is a low-density liquid that has very little surface tension, so it splashes and ‘wets’ surfaces very easily.
To hold the kitchen roll sheets in position, place your metal support (plinth) onto them. Make sure that you arrange the kitchen roll in such a way that when it gets wet with liquid acetone it cannot fall down onto your printed objects, as that will destroy any chances of achieving an acceptable finish.
The following photograph shows the setup used in the acetone bath ABS of the soap trays seen above.
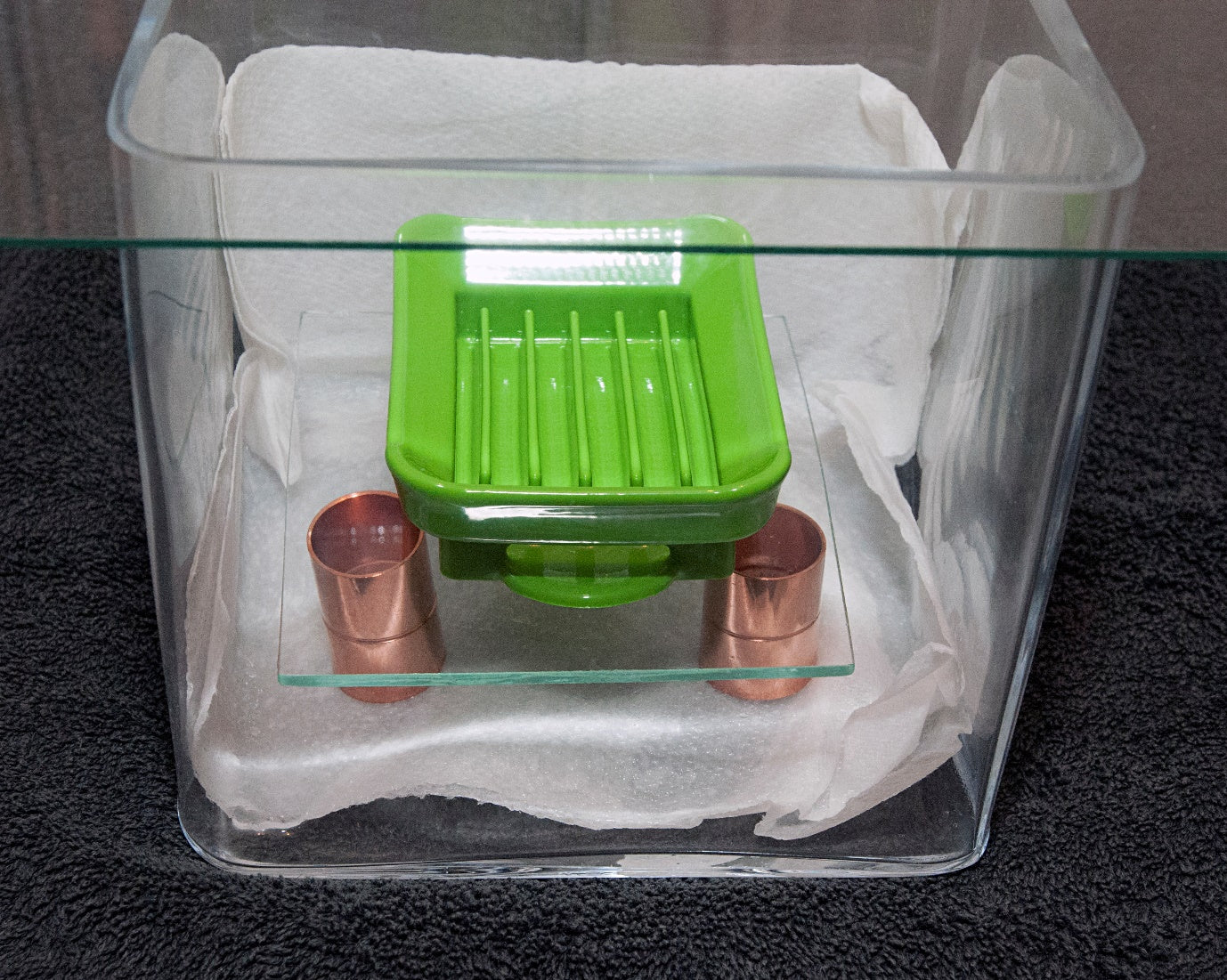
The soap dish is sitting on top of a plinth made from a small piece of glass stood on three 22mm diameter copper plumbing joints – an arrangement that stops any chance of liquid acetone reaching the dish via capillary action (or surface-wetting).
Things to Consider Before Applying Acetone to Your 3D Print
Not all filaments are the same, even from the same supplier. For instance, due to secondary effects from the pigments that go to make up the colors of ABS filaments, different colors polish at different rates. This means you will need to monitor the polishing of different colored objects so that you can remove them at the correct time.
The polishing process not only softens the surface of the object, the fumes also penetrate into the body of the object. Depending on the period of exposure, you will need to ‘air’ the object for a period of time that is commensurate with the time that the object was exposed to acetone vapour.
Usually, this takes a few days. However, in some cases, the full mechanical strength of the object may not be realized until a significant time has passed – for high-density objects, this can take weeks, or even longer!
The polishing process continues for a while after you remove the object from the container – usually for about ten minutes. So don’t be tempted to leave it in too long.
The following photograph shows what happens to a part when exposed to the fumes for an extended period.
The hole in the center at the bottom is supposed to be round, and the lower edges are all supposed to be straight.
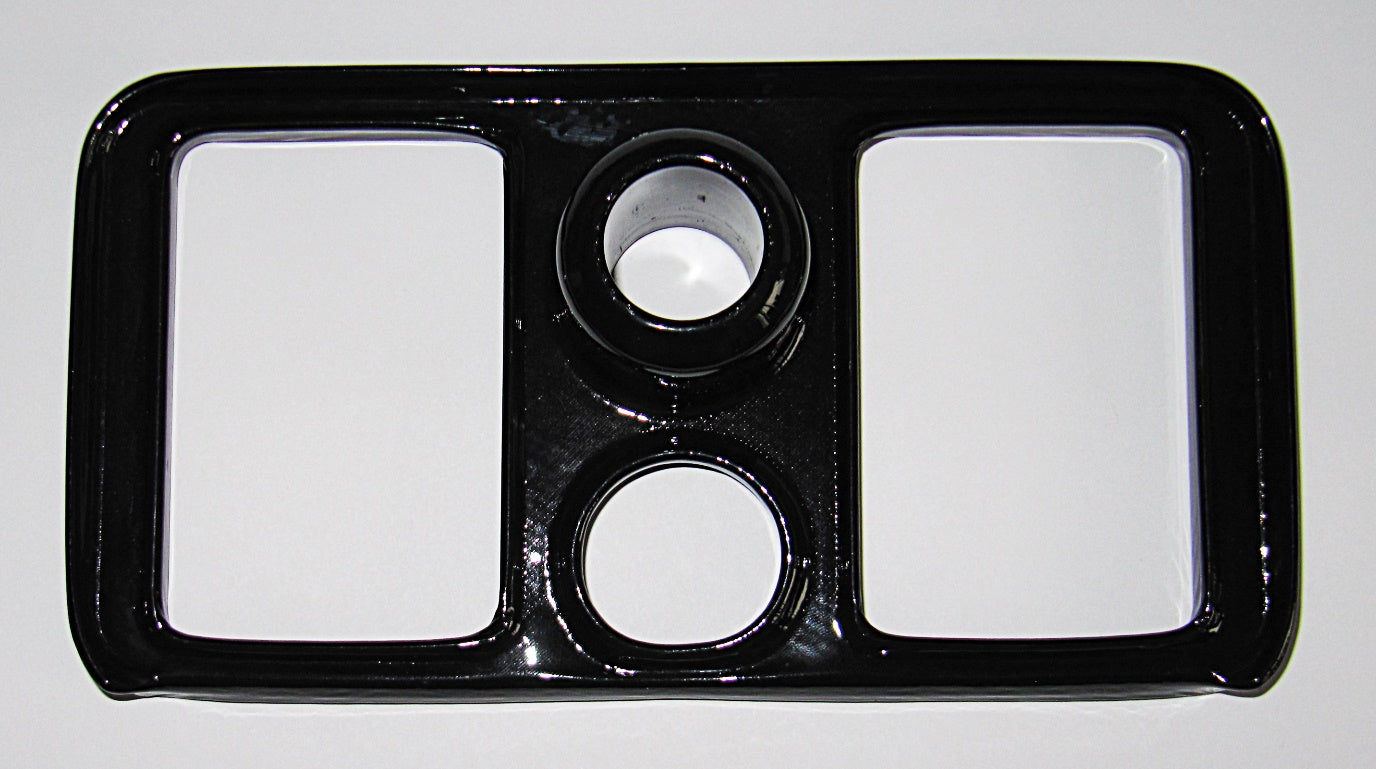
The ambient temperature affects the speed of the process – you are evaporating a volatile liquid after all.
- Too cold and it can take ages.
- Too warm, and the process goes too fast.
- Too hot, and you may be looking for a new place to work/eyebrows, so NEVER apply heat.
Finally – you need to have somewhere totally dust-free to place the polished object while the surface hardens. If you don’t, any dust that falls onto the surface will become embedded in it. Permanently.
Polishing
This is the really easy part.
- Without getting any on your plinth, pour the acetone over the kitchen roll sheets you placed up the side of the container. You need to have enough acetone to cover the bottom of the polishing container to a depth of a millimeter or two.
- Ensure that there is no liquid acetone present on your plinth.
- Make sure that you have a fool-proof way of removing the object from the container after polishing without the need to touch it, or you will leave marks all over the surface where you make contact.
- Quickly place the object in the center of the plinth – try not to touch it again – you have just a few seconds to adjust the final position. The polishing process has already started – it is that quick! You don’t really want to leave fingerprint impressions on your work, do you?
- Place the lid on the container and start your countdown timer. I personally set the timer to 15-minute intervals for finely-detailed objects, and 30 for large solid objects.
Depending on how rough the surfaces of the object are, and how polished you want the object to be, the process can take from around 15 minutes to several hours.
There is ALWAYS a trade-off between the required surface finish and the loss of fine details. Only you can decide what is acceptable.
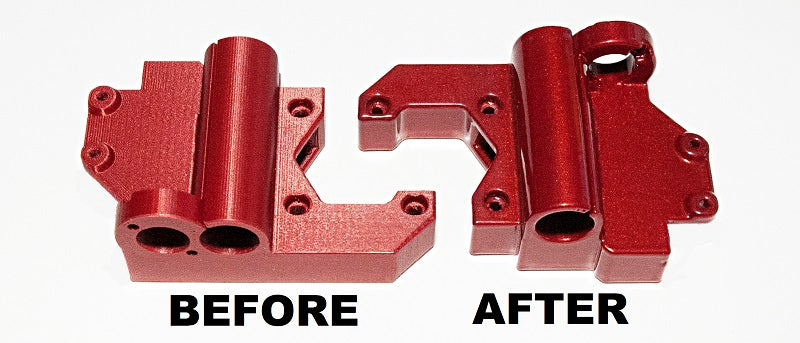
Once you are satisfied that the polishing is almost complete, carefully remove the object to a totally dust-free environment that has good ventilation. This stops most of the ever-present dust particles that are suspended in the air from falling onto the semi-molten surface of the object.
Note: The reason you remove the object from the container at the point just before you get the surface finish you require as the polishing process continues for a short while even after the object has been exposed to fresh air.
You can always put it back in the chamber later if you are not satisfied, but once the process has gone too far, the damage is irreversible.
After about 30 minutes, a ‘skin’ will have formed on the polished object that will stop dust particles from becoming embedded in the surface of the object.
Remove the object from your dust-free chamber without touching it, and put it somewhere that has good ventilation to allow the acetone to further leach out of the object. The object at this point has little to no structural integrity so be careful how you do this.
Depending on the solidity and size of the object, the process of removing the acetone can take from a few hours to many weeks before the full strength of the object has been regained.
Once you are certain that a good skin has formed on the object, you can speed up this process of solvent evaporation considerably by using a fan continuously blow air across the surface of the object – smoothing 3D printed parts effortlessly.
Summary
To recap, the filaments that can be polished using this process are: ABS, ASA, PMMA, HIPS and Polycarbonate.
Other filament types are either unaffected by acetone or are damaged by it.