
What is 3D Printing / Additive Manufacturing?

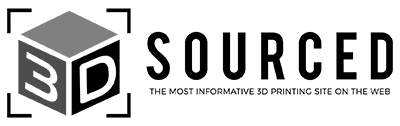
At 3DSourced we’ve covered everything 3D printing and 3D since 2017. Our team has interviewed the most innovative 3D printing experts, tested and reviewed more than 20 of the most popular 3D printers and 3D scanners to give our honest recommendations, and written more than 500 3D printing guides over the last 5 years.
To a complete beginner, 3D printing can sound daunting. “So… you build entire things at once, from thin air, like a Star Wars Replicator?!” This guide seeks to explain the question of what is 3D printing in language anybody can understand, and demystify the technology which promises to change the world.
First, we’ll explain how 3D printing works, and how it differs from every way we currently have of making things. Then, we’ll concisely explain the two main types of 3D printer you’re likely to come across.
We also have a short descriptions of the main uses of 3D printing, such as in the medical field, in the manufacturing of cars, and more, as well as the advantages and disadvantages of 3D printing.
How does 3D printing work? Additive vs subtractive manufacturing
Since the 1400s when Michelangelo was creating astonishing sculptures from marble, our way of making things has involved taking a larger block of material, and chipping it down to create a smaller, final piece. In the modern day this mostly continues, with CNC machines and laser cutters creating final pieces by removing parts from a larger material block. These methods are known as subtractive manufacturing, as they subtract bits to get to the final part.
3D printing is different. Instead, 3D printing builds parts up from scratch, by either depositing melted materials, or solidifying or melting resins or powders to form this part.
Rather than chipping extra material off, 3D printers deposit only the exact amount of material required — leaving minimal waste and saving money on excess material. For this reason, 3D printing is also known as additive manufacturing: it adds to create a part, rather than removing bits from a larger block. For plastics, this is significantly better for the environment.

3D printed parts are created three-dimensionally by printing tiny horizontal layers of material, layer-by-layer, on top of each other to gradually create a larger part. Each layer may be as small as 0.01mm tall — so hundreds of layers may be required to create the part. Budget 3D printers under $500 typically offer up to either 0.1mm or 0.05mm minimum layer heights.
To create precise and accurate details, such as diagonal indents or embossings or embedded text, smaller layer heights are used. But for simple geometries like cubes, large layer heights can be used with no loss of quality.
The 3D printing process
TLDR: What you’ll need:
- A 3D printer
- STL file or CAD software to design your own
- 3D slicer
- Materials: resin or filament
Additive manufacturing is possible because the 3D printer follows precise instructions coded in the 3D printer file — usually an STL file, but sometimes an OBJ or GCODE — determining which areas to print material in.
Therefore, to print you’ll first need a 3D file, which you can either design yourself on a number of different CAD software or free 3D modeling software tools, or download online on a special STL file hosting repository.
- Check out our guide of the best CAD software
- We also have a guide to the best free 3D modeling software
- Or, if you just want to get started straight away, check out our list of sites with free downloadable STL files
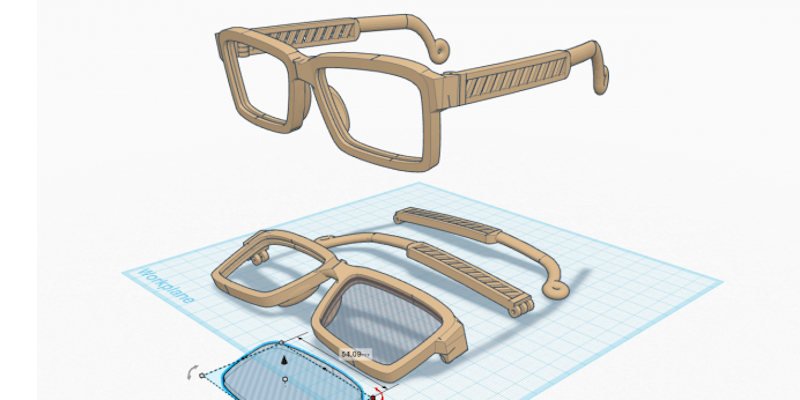
Once you have this file, you’ll need a 3D slicer to import the file into. A 3D slicer does as the name suggests — slices the file into tiny layers. Higher resolution 3D printers are capable of more accurate parts with lower layer sizes, and usually come at a higher cost, but even cheap 3D printers nowadays offer good accuracy.
Once you have resized your model to the size you want to print (most 3D slicers like Cura will tell you how much material and time you current model’s size will take to print), you simply slice the model, and then either export the sliced file on to a USB or SD card and plug it into your printer, or print remotely via WiFi if your printer has this capability. Cura has presets for dozens of 3D printers, making it super easy to get set up and print without much experience.
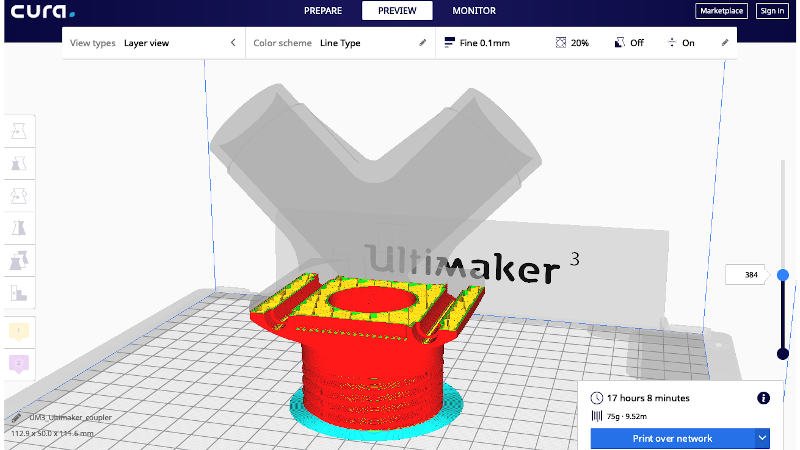
Different types of 3D printing
There are several different 3D printing technologies, each designed for different materials, techniques, and with different advantages and disadvantages. Explaining the nuances of every type would take too long, so we will explain the basics, with optional links to our in-depth descriptions of each technology for those who want to find out more.
- We also have a guide explaining all the types of 3D printers.
The main two types of 3D printers used by hobbyists and makers at home are FDM 3D printers and resin 3D printers. For plastics, much rapid prototyping is done on SLS 3D printers, though hobbyists will find these expensive and complex.
- We offer a FREE eBook for those who want to read all about every 3D printing technology offline and in detail. You can download it for free here.
FDM 3D printers
The simplest to use, set up, cheapest, and most accessible 3D printers, FDM 3D printers are the printer of choice for most makers looking for a low stress, fun printing environment.
They use plastic filaments, long thin tubes of plastic wrapped round a spool, which is melted by a hot end in the printer’s extruder. Once melted, the plastic is deposited out of the nozzle onto the print bed, layer-by-layer, to create the finished part. If you have ever iced a cake using a piping bag, this may sound similar. FDM 3D printers deposit layers of the melted plastic like you would icing on top of a cake, and then once one layer is done, rise up one layer height, as you may do when icing a tall swirl.
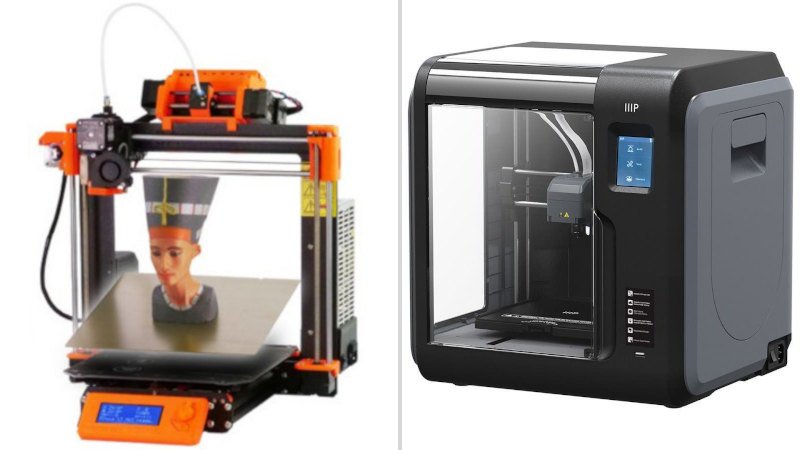
FDM printers are cheap, starting at around $200, and running costs are also low, with PLA filament starting at around $20 per kilo. They often come as DIY 3D printers you need to assemble yourself, though some are plug’n’play — just plug them in and they’re ready to go.
The materials are not irritant on skin, and overall these are probably the safest printers to have, especially if you have kids around, as only the heated bed and hot end get hot, and can be kept away from prying hands with an enclosure.
There are dozens of different 3D printer filaments. Each have different melting points and characteristics, for example ABS will warp and crack if you do not use a heated bed and heated chamber, whereas PLA is fine without either. We explain all these differences in our 3D printer filament guide, but your 3D slicer will also have some pre-sets for each type of filament.
- Check out our recommendations of the best FDM 3D printers.
- To find out more about the technology behind it, check out our guide to fused deposition modeling.
Resin 3D printers
A few years ago resin printers started at several thousand dollars, but new low cost LCD 3D printers by brands like Anycubic and Elegoo have brought prices down to $200 and below.
Resin 3D printers include SLA, DLP and LCD printers, all of which use light to cure resin, but each differ slightly. If you’re a hobbyist maker, you’ll probably be using an LCD printer. SLA was the first technology invented, way back in the late 1980s by Chuck Hull. DLP, and especially LCD, are newer offshoots seen on lower priced printers.
These printers use resin vats to hold liquid resin, and use a projector, UV laser or LCD screen to selectively cure resin and form solid parts, one layer at a time.
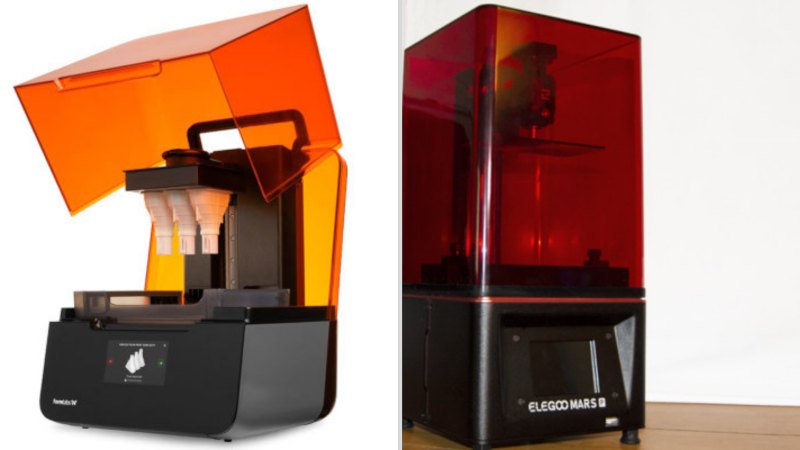
Resin printers are generally faster, much more accurate than FDM printers, and create parts with far smoother surface finishes and crisper edges. Though stats may show similar layer heights, or Z-resolutions, between FDM and resin printers, resin parts are noticeably better quality, with more precise X and Y resolutions. For this reason, resin printers are often used to make wax molds for 3D printed jewelry casting, and also for hearing aids and dental uses.
The resins however are more expensive, the printers are more complex, and some resins can be irritant — so more stringent safety precautions should be taken. You’re generally more restricted with the types of materials you can use than with FDM printing, and parts will degrade if left out in the sun.
Brand new beginners to 3D printing would therefore be better off going with an FDM printer to learn the ropes, before diving into the deeper end with a resin printer. But resin printers offer accuracies and surface finishes far beyond FDM. You can check out our article on is a 3D printer hard to use & learn for more.
- Check out our recommendations of the best resin 3D printers.
- We also have an in-depth comparison between SLA, DLP and LCD.
Other types of 3D printer:
- SLS 3D printers
- PolyJet / Material Jetting
- Binder Jetting
- Multi Jet Fusion
- Directed Energy Deposition
- Direct Metal Laser Sintering
- Electron Beam Melting
Who invented 3D printing?
This is debated, based on how you define ‘inventing’. Academic articles describing a then-nonexistent method of creating parts layer-by-layer have been published since the 1970s. In 1981, Hideo Kodama published a paper discussing a ‘rapid prototyping’ technique, and in 1984, three French engineers applied for a patent for the stereolithography process. However, they dropped the application as they felt there wasn’t any money in it.
American Chuck Hull filed the patents for stereolithography shortly after, was granted them in 1986, and commercialized the tech, founding 3D Systems. As of January 2021, 3D Systems is worth $1.3bn.
Chuck Hull is considered the father of 3D printing, and the first to sell a working 3D printer over 30 years ago.
- For more market values, view our ranking of the most valuable 3D printing companies.
- For more information, you can read our in-depth 4,000-word history of 3D printing.
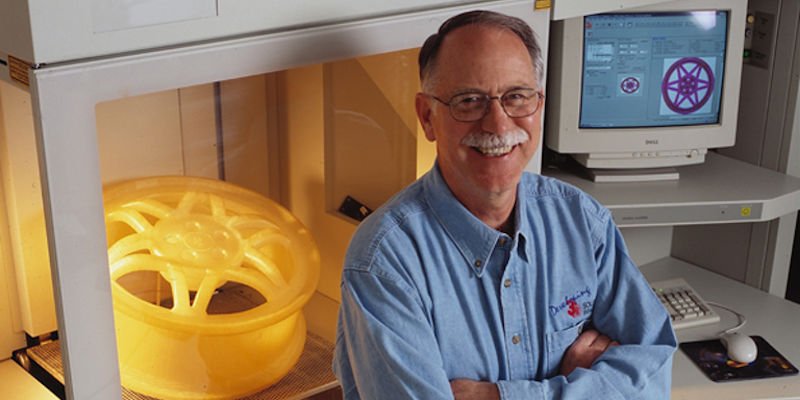
3D printing uses and applications
The first uses for 3D printers were mostly testing new prototypes for car parts and iterating and making small improvements based on these test parts. However, since then, 3D printing has advanced to have huge impact on a wide variety of industries.
The following are some industries 3D printing is improving and changing. Click any of the links below to be taken to our feature stories we have covered on 3D printing’s impact in the industry.
- Medical
- Dental
- 3D printing organs — bioprinting
- 3D printing houses
- 3D printing cars
- Car parts for classic cars
- Boats
- Clothing and fashion
- Shoes and sneakers
- Jewelry
- Rapid prototyping
- Food
- Guns
- In crises e.g. COVID-19
Advantages and disadvantages of 3D printing
3D printing advantages
- Custom, one-off parts: never before has such versatility in production been possible. One-off models can be made with the exact same efficiency as a hundred, making 3D printing perfect for testing new prototypes quickly to improve products.
- Lots of different materials: FDM printers alone can print materials ranging from PLA and ABS, to Polycarbonate, Nylon, Carbon fiber and PEEK. Resin printers can print dental, castable and even ceramic resins, and other 3D printers can print metal, ceramics and clay, wood, and even paper.
- Complex geometries and shapes possible: Whereas traditional molds cannot create certain shapes, 3D printers use supports that can be removed in post-processing, allowing for the production of parts with steep angles and overhangs.
- Better for the environment: Subtractive manufacturing chops away at larger blocks, wasting these unused materials. With 3D printing, only the exact quantities of material required are used, using less plastics and wasting less surplus material. Moreover, many plastics used in FDM printing are recyclable, and PLA filament is even biodegradable.
- Low starting costs: 3D printers can create almost any shape, from a huge variety of materials, and can be post-processed further if necessary. It’s almost like having a mini factory in one machine. Anyone can start making parts, models and toys from scratch for just a couple hundred dollars — the limits are just your own creativity.
- Print on-demand, no inventories: Carrying inventories is inefficient; trying to plan when people will buy means you’re spending on buying stock that could be used for better things. With 3D printing, parts and products can be made on-demand only when needed, keeping your production lean and efficient.
3D printing disadvantages
- Slow and not very scalable yet: 3D printing is still far too slow to challenge injection molding or CNC in producing large amounts of goods. It is still firmly rooted in its niche for one-off and very small batch production, as not enough parts can be produced quick enough for mass production.
- Post-processing required: Unless you’re printing very simple shapes, you’ll likely need supports that reinforce the part during printing and prevent gravity deforming your part before it has solidified and cooled. These need to be removed, which can cause slight imperfections on the surface of your prints — though soluble supports like PVA and HIPS can be used to avoid this. Other post-processing like painting, sanding, and other forms may also be required.
- Less accurate at lower prices: Though vastly improving year by year, you cannot expect the world on a 3D printer under $500. These entry level 3D printers are fine for hobbyists, but for business looking for a rapid prototyping 3D printer or to use as part of a 3D printing service, you’ll need to spend the bigger bucks.
- Some materials weaker, and degrade: Some materials, such as resins, degrade in sunlight or under medium-high heats, such as resins. Additionally, filaments like PLA are brittle, and break under strong impacts. Most frustratingly, many materials used in FDM 3D printing are hygroscopic, meaning they absorb moisture and water from the air. This can quickly worsen your part print quality as it creates water bubbles and bubbly surfaces, so it is vital to store your filaments in an airtight and dry location. We recommend filament dryers and containers.
To find out more, check out: