
How is 3D Printing Changing the World of Fashion?

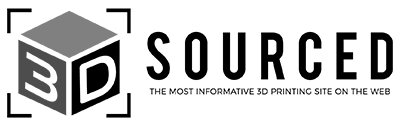
At 3DSourced we’ve covered everything 3D printing and 3D since 2017. Our team has interviewed the most innovative 3D printing experts, tested and reviewed more than 20 of the most popular 3D printers and 3D scanners to give our honest recommendations, and written more than 500 3D printing guides over the last 5 years.
Recent advances over the last seven years have proven both the potential, and viability, of 3D printed fashion. Opportunities have risen for the technology to move away from film sets and runways, to fashion retailers and the mainstream market.
With the removal of clothing factories, a minimal environmental footprint, and clothes poised to become a digital service similar to Spotify being only some of this technology’s potential implications; it’s worth taking a deep dive into the world of 3D printed fashion.
- This article focuses on luxury fashion. We also have a feature story on 3D printed clothing
How much fashion is 3D printed today?
Accessories
As 3D printing has developed, so too has its ability to produce increasingly high-quality fashion accessories. It has moved away from just being seen as a source of replacement buttons and is now established in the luxury items market.
Initially, 3D printing was used in the production of jewelry in a process called lost wax casting, usually taking the form of molds for rings, bracelets, and pendants. Eventually however, 3D printed parts made their way into the final products of many luxury items. Notably, Panerai unveiled the “Lo Scienziato Luminor 1950 Tourbillon,” a watch with a metal 3D printed case, and a value of over $170,000.
- We also have article on 3D printed jewelry.
Direct Metal Laser Sintering (DMLS) was used to make the watch’s case, using a high-powered laser to melt and fuse layers of metallic powder. Despite being available since 1995, the technology has typically been used in prosthetics and engineering components, making Panerai one of the first brands to use the technique in a luxury 3D printed fashion accessory.

However, where 3D printing especially caught the industry’s attention was its ability to create highly customizable consumer fashion items.
Potentially the most influential sector to have been drawn in by this opportunity is that of sportswear brands. Nike, Adidas, Under Armour and Reebok are all experimenting with implementing the technology into parts of their shoes, with an eventual goal to add further options for customer customization, and until then impossible product designs, across their ranges.
Garments
3D printed fashion’s most persistent challenge has been in finding a strong yet flexible material. Most 3D printer filaments have traditionally been rigid, and therefore unsuitable for clothing that has to both articulate and flex with the human body, as well as withstand everyday activities.
In 2013, threeASFOUR released their Mer-Ka-Ba collection for their exhibition at the Jewish Museum in New York. The collection featured entirely 3D printed dresses, with the technology’s capabilities on show through their avant-garde designs. Reports at the time describe the range as “both ethereal and geometric… The garb of angelic robots.”
However, the garments also proved to be highly impractical. The material was largely rigid and fragile, so much so that the models were unable to even sit down without shattering their dresses. In the years since, advancements in 3D printing have led to technologies that could allow 3D printed fashion to be more than a runway spectacle.

The Rise of TPU Garments in 3D Printed Fashion
For 3D printed fashion to develop, a material was required that was flexible enough to behave like conventional fabric, soft enough to be comfortable against the skin, and durable enough to be worn while completing normal activities. The most common material used for these fashion pieces is TPU, with its arrival allowing the industry to take its next step.
TPU (thermoplastic polyurethane) is a highly flexible, durable, and smooth material. Despite being invented in 1959, it only became usable as a truly elastic 3D printing filament from 2013, in the forms of Filaflex and TPU 92A-1.
- We also have a more complete guide to TPU filament.
Filaflex was used by Danit Peleg in her 2015 fashion collection, “Liberty Leading the People,” with its flexible properties giving her opportunities for development that rigid filaments could not.

A Flexible Revolution?
Using TPU, Danit was able to design and print lace-like patterns that she could work with in a similar fashion to cloth. The resulting garments were light, flexible, and strong, able to naturally form to the body without the risk of shattering if the model sat down.
This collection is also unique in that it was produced entirely in Danit’s own home using desktop 3D printers small enough to fit on most desks, offering a glimpse into a potential future for the technology’s democratization of fashion.
Since then, new techniques and blends of flexible polyurethane have pushed what 3D printed clothing looks like closer and closer to conventional fabrics.

A recent and notable example of this is Julia Daviy’s 2018 “Liberation collection,” a collection of 3D printed clothing specifically designed to move away from the largely abstract or futuristic look 3D printed fashion had become know for.
Her collection instead emulated conventional streetwear in a series of 3D printed skirts and dresses largely indiscernible from their fabric counterparts. All these items are again made of soft and flexible material, though Julia uses a different thermoplastic — 70A TPE (Thermoplastic elastomer – rather than TPU).

Taking 3D Printed Fashion off The Runway
Currently, 3D printed fashion remains almost exclusively reserved for runway fashion shows, with Julia Daviy and Danit Peleg making up the minority who have made their designs purchasable online.
3D printed clothing has proven itself to be comfortable, flexible, and as close to conventional fabrics as we’ve ever been, so why then is it not seen outside of the runway?
Cost
A combination of factors makes it incredibly hard for 3D printed fashion to compete with the conventional marketplace, with one of the main obstacles being cost.
3D printing high-quality clothing remains a time-consuming task, and requires expertise to properly assemble, adding to the expense. Danit Peleg’s commercially available jacket takes over 100 hours to fully print and assemble, costing $1,500, with only 100 items ever being made to sell.
Similarly, Julia Daviy’s 3D printed “Organic” skirt is a made-to-order item. With the use of large format and industrial 3D printers, she has been able to bring the production time down to only 20 hours. However, like Danit Peleg’s jacket, this item also remains far beyond the budgets of most consumers, being between $780 to $1,500 depending on the customization options.
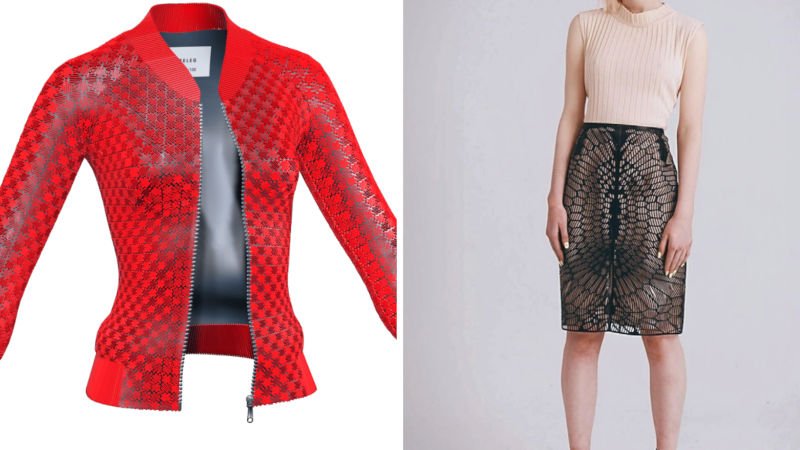
Despite this, cost alone is not keeping 3D printed fashion from stepping off the runway. Indeed, paying premium prices for designer clothing is not uncommon, with a Burberry trench coat costing easily over $1,900. So, what else separates 3D printed fashion from its competition?
The effectiveness of 3D printed clothing
Although great strides have been made in 3D printed material’s durability and flexibility, 3D printed fashion is still not as viable as its conventional competition. In almost every scenario, conventional materials are more effective than their 3D printed equivalents.
In Sweaty Situations
When exercising, polyester, spandex, and other moisture-wicking synthetic fabrics keep the wearer cool and dry. They achieve this by absorbing sweat from the body, then drying rapidly by evaporation, cooling both the fabric and wearer.
In contrast, TPU can actually trap sweat against the body by not allowing it to permeate and escape. This wet environment can cause chafing and an experience similar to sweating into a plastic bag.
In bad weather
In the cold, cotton and natural fibres offer better insulation than layers of filament, with no winter-specific 3D printed clothing currently available.

In the summer, the lightness and the mesh structure of most 3D prints could prove useful in keeping cool. However, extended exposure to the sun could discolor or even warp the garment. TPU phone cases are known to yellow in sunlight, and PLA prints have been observed slowly bleaching when kept outdoors, with some blends even melting in hot cars.
Alternatives such as PETG (Polyethylene Terephthalate) are suitable for all weather conditions but are rigid and currently unsuitable for general fashion garments.
Though conventional fabrics can also fade or bleach over time, they pose no risk of melting during a long drive.
And the Wears and Tears of Daily Life
Despite its advancements, 3D printed clothing still remains more fragile than their competition. If a TPU jacket is worn daily by a train commuter, the soft filaments and mesh structures are unlikely to outlast the proven durability of conventional fabrics; the soft material will quickly become scratched, and the mesh structures will be prone to snagging and eventually ripping, outlasted by common cotton-based materials.
Another issue for 3D printed fashion is convenience. Conventional fabrics can almost always be machine washed, whereas most current 3D printed materials have to be hand washed in order to maximize the garment or accessory’s lifespan.
With such fierce competition coming from the conventional industry, it seems that 3D printed fashion is not quite ready to compete outside the realm of haute couture and runways. However, with the technology developing so quickly, it may not be long before 3D printed fashion becomes commonplace. If 3D printed fashion becomes affordable, indistinguishable from traditional fabrics, and the predominant source of clothing, then what would change?
A Vision of the Future
Firstly, the fashion industry could have a greatly reduced carbon and environmental footprint. Less clothing would be wasted, as all clothing would be made-to-order and perfectly fitted with no textile scraps.
If customers are able to print designs in their own home, then both the environmental factor of shipping separate materials across the world, and the ethical risk that part of a garment’s production came from a sweatshop, are both bypassed.

- We also have a feature story on 3D printed shoes.
Additionally, if these fashion items are 100% recyclable then they could be reconstituted into a filament and reused once we get bored or grow out of an item. This potentially wasteless system could remove the strains of fast-fashion, and the concept of an overcrowded wardrobe.
It is still unclear as to whether 3D printed fashion will play a negative role in our rising awareness of microplastics, as this will depend on how our understanding and use of the materials develops. Filaments can be both biodegradable and recyclable, with PLA, currently the most commonly used filament, being a prime example. However not all are, and we can only speculate as to what new filaments will be used in future of 3D printed clothing.
To visualize how this future could affect us, consider the following scenario:
Going Digital
Tomorrow you’re attending a wedding. You decide to update your suit, so you go online and buy and download a design you like. The next day you only pack some toiletries, and drive across the country before arriving in your hotel room. There, you use the file you brought yesterday to print your suit and shoes. After attending the wedding, you place your suit into the hotel’s recycler where it is turned back into filament and ready for the next guest to use.
Whilst speaking at a Ted Talk in 2016, Danit Peleg closed by saying “Music was once a very physical thing. You would have to go to the record shop and buy CDs, but now you can just download the music. Digital music. Directly to your phone. Fashion is also a very physical thing. And I wonder what our world will look like, when our clothes will be digital, just like this skirt is.”
If 3D printed fashion continues to progress at the rate it is, then she won’t have to wait long to see if that vision becomes a reality.
Read more: the best fashion design apps and software