
3D Printed Boats: The Future of Maritime & Shipbuilding

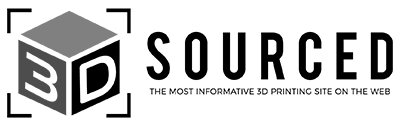
At 3DSourced we’ve covered everything 3D printing and 3D since 2017. Our team has interviewed the most innovative 3D printing experts, tested and reviewed more than 20 of the most popular 3D printers and 3D scanners to give our honest recommendations, and written more than 500 3D printing guides over the last 5 years.
Whereas several hundred thousand pairs of 3D printed shoes already grace the feet of runners and streetwear fans worldwide, industries such as 3D printed boat building are still in their infancy. However, 3D printed boats are hugely promising, and look set to change the boat building industry over the next decade.
- If you enjoy this article, read our other 3D printing feature stories here.
3D printed boat production promises to produce boats fast and cheaper than ever before. Additive manufacturing can create more efficient military boats, more environmentally friendly private yachts, and even autonomous boats that reduce congestion in canal cities. With the world’s largest 3D printed boat created in 2019, there are sure to be many more exciting innovations in the coming years.
Read more: the best boat design 3D software
Advantages of 3D Printing in Boats
A conference paper on the use of 3D printing in marine applications states that 3D printed boats “can be produced lighter, the parts can be customized without loss of material and the parts can be replaced easier.”
Let’s take a closer look at the benefits of 3D printed boats.
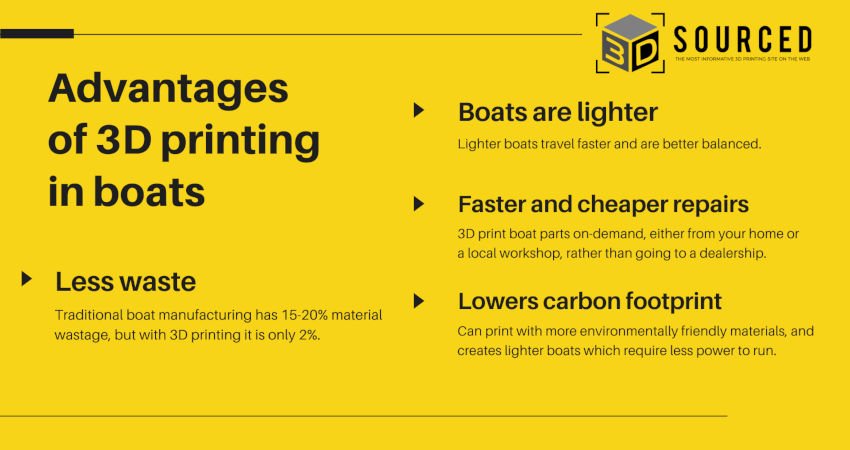
Less Waste
Traditional, subtractive boat manufacturing methods like CNC milling use a lot of materials, resulting in high levels of waste. In contrast, 3D printed models and parts waste less, and are cheaper to make.
3D printing minimizes waste, only using what is required for a part, with any excess material reusable in other printing jobs. Naval architect Gregory Marshall says that “Typically in a shipyard, you see about 15 to 20 percent raw material wastage. With 3D printing, it’s around 2 percent, so it’s a huge savings in material, a huge savings in labour.”
Lighter Boats
One of the main benefits of using additive manufacturing in boat production is that the boats developed can be lighter and faster. This is because 3D printers print in 10% to 30% infill, which produces somewhat hollow materials that are light but still very strong.
Lighter 3D printed boats are also better balanced, as well as travel faster. The researchers at Rammses Project have produced a 3D printed boat propeller which, when produced at full scale, they believe will weigh over 40% less than conventional components. Marshall also predicts that by 2030 yachts will be 3D printed using titanium, which is lighter than steel.
Faster and Cheaper Repairs
3D printing can be used to efficiently produce spare boat parts – already widely used in the automotive industry. This is particularly beneficial as boat hull parts are often damaged and dirtied at sea, wherein 3D printing offers faster repairs at a lower price.
A paper written by researchers from the University of the Aegean states that 3D printing can be used to streamline the spare parts supply chain by allowing spare parts to be 3D printed by the end user at the place it is needed. Rather than going to a shop and having to purchase parts that take days to arrive, you can instead 3D print the part from your garage or studio.
Lower Carbon Footprint
3D printed boats can be more environmentally friendly than regular boats. For example, the Ramsses Project, which aims to develop more sustainable shipbuilding techniques, is researching the use of 3D printing boat propellers using metal alloys such as cupro-aluminium, rather than steel.
This will result in lighter, more efficient propellers, which is important as the maritime sector is lagging behind many other industries when it comes to lowering carbon emissions. Searious Business, a Dutch association fighting against plastic pollution, even plans to print a 3D boat from plastic waste, which we cover further down this article.
The World’s Largest 3D Printed Boat: 3Dirigo
The most significant step so far in 3D boat printing is 3Dirigo, a 3D printed boat created by a team of researchers at the University of Maine. The project earned three Guinness World Records: the largest 3D printed solid part, the largest 3D printed boat, and the largest prototype polymer 3D printer.

3Dirigo, a patrol boat, weighs in at 2.2 tonnes and measures 7.62 meters in length. The printer produced the UMaine 3D printed boat in just 72 hours, using a blend of plastic and cellulose derived from wood resources.
The 3D printer, which is capable of both additive and precise subtractive manufacturing, was developed by Ingersoll Machine Tools alongside the UMaine team. It was designed to create rapid prototypes for defence, civil and infrastructural applications and can 3D print objects up to 100ft long, 22ft wide and 10ft high. It prints an incredible 500 pounds of material per hour.
UMaine-affiliated projects recently received two grants of $20M and $500K to develop 3D bio-based printing materials for large-scale additive manufacturing and the shipbuilding industry. The researchers found that boat molds and parts can be produced faster and cheaper by 3D printing 50% wood-filled plastics.
The printer used to create the UMaine 3D printed boat will also be used by the US Army Combat Capabilities Development Command to manufacture deployable shelter systems. UMaine also presented a 3D printed army communication shelter alongside 3Dirigo.
Other 3D Printed Boat Projects
While the University of Maine 3D printed boat is the most significant and advanced 3D printed boat project, there have been several other important projects over the last few years.
LSAM Marine Boat Hull
In late-2017, India-based company Thermwood Corporation revealed its 3D printed boat hull pattern for a fiberglass motorboat. The hull took the company’s LSAM 3D printer 30 hours to produce and weighed an astonishing 1,363 kilos.

The LSAM machine featured exchangeable print heads and can be switched from a 3D printer to a 5-axis CNC mill, an industry first. The hull was 3D printed using ABS filament reinforced with carbon fiber, before switching to the CNC mill print head to improve the accuracy of some areas. Once the hull pattern was printed, it was coated with a finish and a fiberglass mold.
Thermwood says that 3D printing offers more potential advances in marine engineering, such as 3D printing the hull and deck pattern as a single piece, resulting in significantly faster building time and lower tooling cost. It is also exploring the possibility of printing molds for large boats and yachts directly, rather than printing a pattern from which the mold is taken.
Following on from this project, Thermwood now uses the LSAM 3D printer to prototype speed boat hulls, submarine hulls and helicopter wings for the US military and private industry. This is part of a collaboration with the Carderock Division of the Naval Surface Warfare Center, the Navy’s research and engineering center for ships and ship systems.

WAAMpeller: The World’s First 3D Printed Boat Propeller
The world’s first 3D printed boat propeller, the WAAMpeller propeller, was introduced at Demen shipyard in the Netherlands. The propeller was manufactured using Wire Arc Additive Manufacture (WAAM), one of the fastest additive manufacturing methods in use, with the machine printing tens of grams of printing material per minute. WAAM technology can be integrated with robotics, so it’s not limited to small volumes like desktop 3D printers.
The propeller was rigorously tested by the Breau Veritas Society and passed all trials in speed, traction, and brake tests. WAAMpeller was installed on a Damen Stan Tug 1606 and then put through speed trials and bollard pull-and-crash stop testing.

Kees Custers, Damen Project Engineer, said that “The testing was a success…the WAAMpeller displayed the same behaviour as a conventional casted propeller in all of the tests. This includes the same level of performances in the crash top scenario, which, going from full throttle ahead to full throttle reverse, is the heaviest loading that a propeller can experience.”
The success of WAAMpeller is particularly exciting as it shows that not only does 3D printing make the manufacturing process easier, but it is also capable of producing certified products quickly and efficiently.
Allard Castelein, CEO Port of Rotterdam, said that the project is special as it “has shown the shipbuilding industry the potential of 3D printing techniques for the production of vessel components.” His views were echoed by Kevin Hamilton, a senior technical consultant at Autodesk who was involved in the project from beginning to end, who said that: “This repeatability provides the potential to radically transform the whole industry.”
3D Printed Boat Produced from Plastic Waste
One project that could have a huge impact not just on boat building but also the fight against environmental damage is Serious Business’ aim to develop the “One Minute Boat”, a 3D printed boat from plastic waste, specifically bottles made of polyethylene terephthalate (PET).
The boat, which will be about 55 feet long, will weigh 20 tons, equivalent to the weight of plastic that is dumped into the world’s oceans every minute. While development of the final model is yet to begin, Searious Business has already developed a 2-meter long prototype which was presented at the finish of the 2018 Volvo Ocean Race in the Netherlands. Approximately 1,000,000 used PET bottles will be used to make the hull and superstructure of the final boat.
The company’s proposal states that the estimate energy required to build the boat will be about one third of conventional methods. It also states that the boat could be used for scientific expeditions, company events and educational purposes. Searious Business is currently seeking investment to further develop this exciting project.
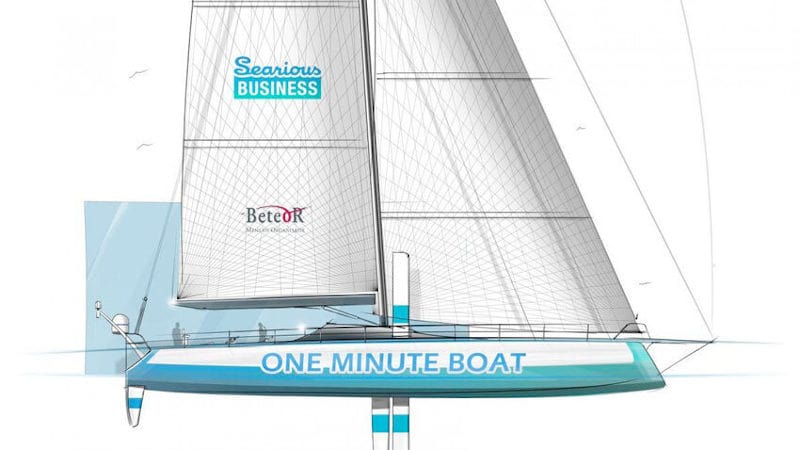
3D Printed Yacht Hull: HanseYachts
The world’s first 3D printed yacht hull was developed by HanseYachts AG, a German luxury yacht manufacturer, back in 2016. HanseYachts built their own 20-meter large 3D printer to create the prototype, and printed the yacht hull using a wood-filled filament.
Karl Dehler, one of HanseYacht’s chief developers, said that 3D printing allows the company to manufacture more powerful hulls, while also reducing production times – helping satisfy customer demand. Dehler also stated that “a result of the 3D print, the Hanse individualization concept can be implemented in every possible way.”

Dr. Jens Gerhardt, CEO of HanseYachts, is optimistic. He said that “When partners within our industry tell me that 3D printing will never be successful, I often like to remind them of the introduction of GRP in the 60s, which was highly controversial at the time as a building material for boats.”
“Already in that time Dehler had experimented with modern materials and against all expectations quickly established itself as the first German large-scale manufacturer of fibreglass yachts. Still today we see the power of innovation as a core competitive advantage of our yard and we are proud to set a new milestone in the international boat industry.”
Autonomous 3D Printed Boats
Another interesting 3D printed boat industry project is the design of autonomous boats. Researchers believe that by transporting people and allowing infrastructure services such as deliveries and waste management to be autonomously performed overnight on the water, 3D printed boats can help reduce traffic in congested cities.
The boats are designed for use in cities that have a large amount of waterway travel, such as Venice, Amsterdam, and Bangkok. They could be used to taxi people, deliver goods, and perform city services overnight. Beyond that, the boats could even be programmed to self-assemble structures such as floating bridges and platforms for food markets.
This would help to reduce congestion on both canals and roads. The boats could even be equipped with sensors to monitor cities’ waters and provide inside into human health in these urban settings.

The project is a collaboration between MIT’s Computer Science and Artificial Intelligence Laboratory (CSAIL) and the Senseable City Lab in the Department of Urban Studies and Planning (DUSP).
Javier Alonso-Mora, an assistant professor in the Cognitive Robotics Department at Delft University of Technology, has said: “Twenty percent of the surface in the Netherlands is water, and robots can be an efficient mode of transportation and logistics. This is a first step in that direction, with a very nice prototype that is able to move in all directions and connect with other boats to build temporal structures. Together with the team at MIT we are now looking at the next steps in autonomy, including multirobot coordination and urban navigation.”
This innovation is part of the RoBoat project, a collaboration between the Senseable Lab and the Amsterdam Institute for Advanced Metropolitan Solutions (AMS). A rectangular prototype equipped with sensors, GPS controllers and micromodules was tested in Amsterdam’s canals in 2016 and moved forward, backwards, and laterally following a pre-programmed path.
The prototype was printed in 16 pieces over 60 hours and then fused and sealed with layers of fiberglass. The rectangular shape allows it to move sideways and attach to other boats to assemble structures. There are four thrusters positioned at the centre of each side, rather than the corners, to generate both forward and backward movement.
Conclusion: The Future of 3D Printed Boats
While the boat building industry has been relatively slow to adopt 3D printing technology comparison to others, things are changing. 3D printed boats allow for cheaper, better performing, and more environmentally friendly products, and the 3Dirigo project is an example of just how quickly 3D printed boat technology is evolving.
Researchers and engineers are only just scratching the surface of 3D printed boat technology. Speaking at a presentation at the 2017 Superyacht Design Symposium, Gregory Marshall said technology for 3D printed yachts and superyachts could be in place by 2030.
Marshall has stated that “3D printing can disrupt almost every aspect of our industry. Whatever we can imagine, we can now manufacture.” Similarly, the authors of this conference paper conclude that 3D printing “will lead to major changes and innovations in the future”.
So, the future is bright for 3D printed boats, with rapid growth likely over the coming years. 3Dirigo, the most complete 3D printed boat project to date, is an exciting indication of things to come. From self-driving canal taxis to futuristic super yachts, we’re excited for the future of boats, and even 3D printed ships, in the future.