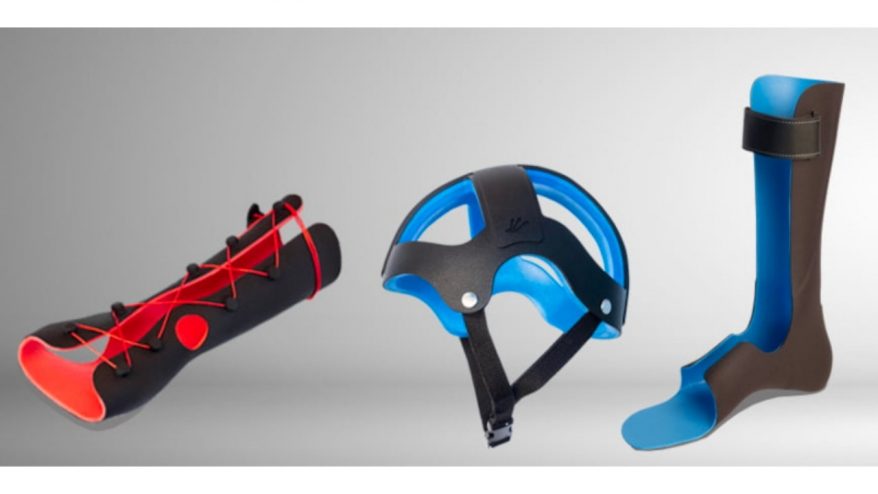
3D Printed Orthotics: 3 Most Exciting Projects
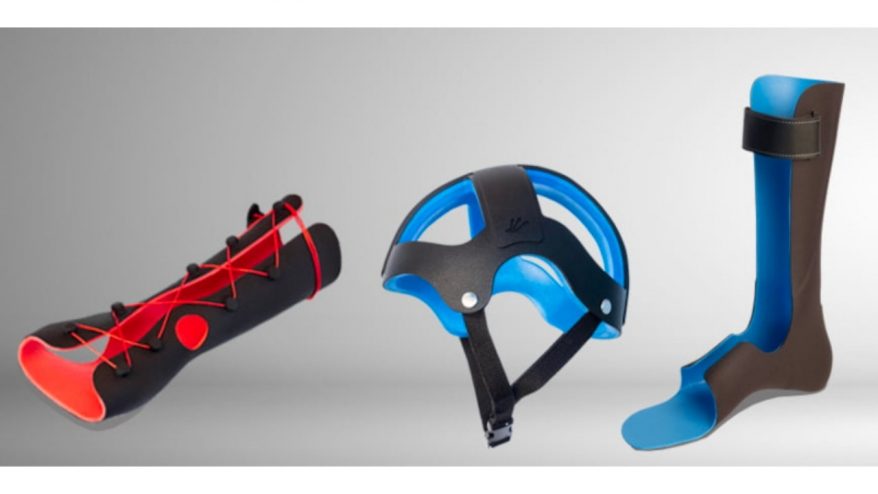
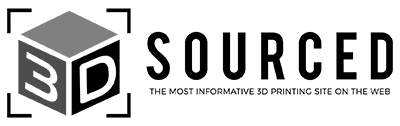
At 3DSourced we’ve covered everything 3D printing and 3D since 2017. Our team has interviewed the most innovative 3D printing experts, tested and reviewed more than 20 of the most popular 3D printers and 3D scanners to give our honest recommendations, and written more than 500 3D printing guides over the last 5 years.
An Allied Market Research report predicted that the orthotics industry would grow from $3,130 million in 2013, to $4,658 million in 2023.
It also predicted that the largest threat to this growth wasn’t external, instead explaining that the “high cost of the customized orthotic devices are expected to restrain the market growth.”
However, since the report’s publication, 3D printing has inserted itself further into the custom orthotics industry.
The result: cheaper, faster, and in some cases more effective orthotics treatments. So, with that in mind, here are three exciting ways that 3D printing is changing the orthotics industry.
1. 3D Printed Orthotic Insoles
Shoe insoles are perhaps the best-known type of orthotic. Over-the-counter insoles are used to treat common podiatry issues such as flat feet. However, there is a growing market for custom insoles.
Going custom ensures the most effective treatment and comfortable fit possible. Although this is overkill for most patients, going custom can be useful for patients with severe issues, or for athletes who may have mild issues but regularly put large amounts of force through their feet.
Custom insoles are usually produced with a plaster impression of the patient’s feet. This is used to hand-make the required insole, ensuring that it meets the patient’s prescription, and fits perfectly.
Unfortunately, custom insoles are expensive, making them inaccessible for some patients. A pair of over-the-counter insoles rarely cost more than $50, whilst custom pairs can run from $200-$800, with additional costs for consultations and medical fees.
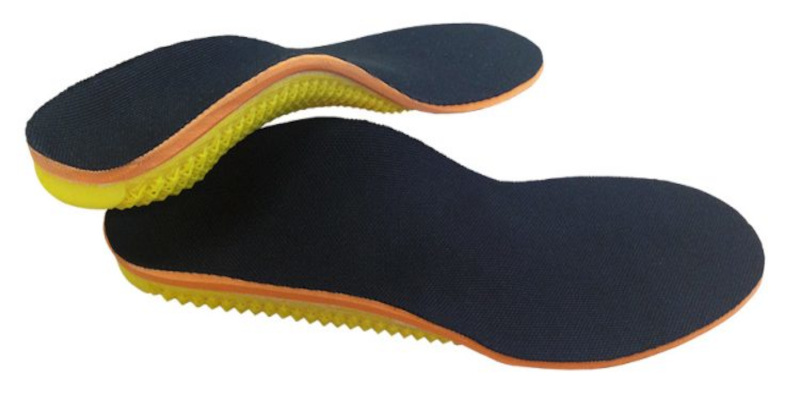
SLS 3D Printing of Insoles
Although not every podiatrist will have them available, 3D printed insoles have grown in both popularity and availability.
Usually, the medical assessment stage is identical, with dimensions of the patient’s feet taken with a 3D scanner or manually. However, instead of the insole being hand-made, it is uploaded onto 3D sculpting software before being 3D printed.
The resulting insoles perform indiscernibly from hand-made ones. To achieve this, most manufacturers use Selective Laser Sintering instead of FDM machines.

When describing their process, Phits, a manufacturer, explained that:
“[FDM was] completely inadequate for producing insoles because it is too slow, lacks accuracy, and most of all it doesn’t provide the necessary strength… We use a much more advanced technology called Selective Laser Sintering. During this process, a very fine powder (we use PA or Nylon) is hardened and bonded together layer by layer. The result is a very light, very strong final product.”
This sentiment isn’t just held by the manufacturers, with medical professionals also agreeing that SLS is really the only effective way to 3D print orthotic insoles.
Mark Ireland is a practicing podiatrist with his own Australian-based clinic. Whilst experimenting with 3D printing custom orthotics, he explained that:
“we quickly realized the FDM parts did not possess the mechanical strength we required from our products… We also trialed SLA but unfortunately faced the same outcome… Our parts need to have a high degree of accuracy and can involve complex shapes… They also need to have some flexibility without shattering… Furthermore, a low moisture absorption is also key due to the environment such orthoses are commonly used in. According to Mark, the selective laser sintering process is one of the few additive technologies that could meet these demands.”
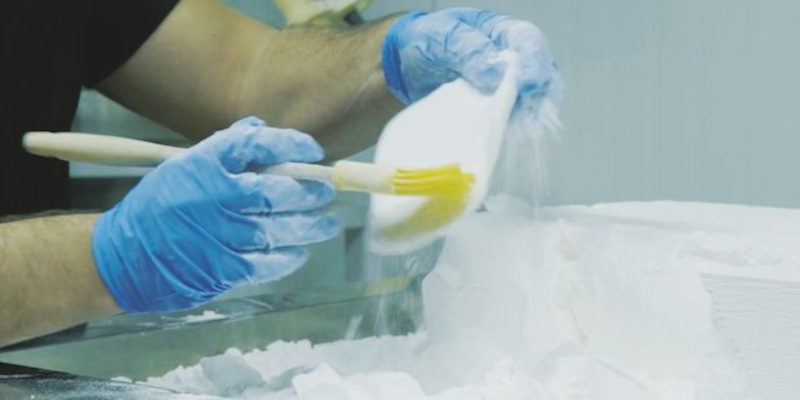
Replacing the conventional method?
The efficiency of 3D printing allows patients to receive their insoles faster. Additionally, manufacturers are able to produce their orthotics with the same level of accuracy, but with less material waste and working hours.
Unfortunately, these savings haven’t made 3D printed insoles significantly cheaper. As an example, the Blackberry Clinic in the UK charges £3260 for a pair of Phits orthotics.
Despite being 3D printed, this pricing matches up to be perfectly average for the custom orthotic insoles market.
Exactly why the improved production process hasn’t also reduced costs isn’t clear, but the future of 3D printed insoles remains promising. Currently, there doesn’t seem to be any significant obstacles against its continued use, with the technology poised to entirely replace the conventional method in the near future.
2. 3D Printed orthotic casts
3D printed orthotic casts are perhaps the most visibly striking item on our list. But they’re not all glitz and glamor, with their design offering significant advantages over their plaster counterparts in almost every way.
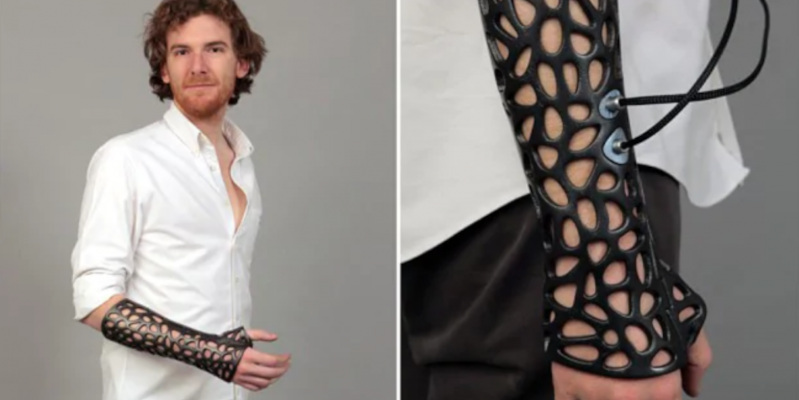
When someone fractures a bone, it must be immobilized to ensure that it heals in the correct position. Some patients will be given a temporary splint at the site of their accident, but almost all patients will need to visit the ER as soon as possible to get a cast fitted.
Read more: our feature story on 3D printed casts
Provided that surgery isn’t required, the patient will be fitted with a plaster cast at the ER. Interestingly, the nature of treating fractures means that 3D printed casts are unlikely to ever replace this step. Fractures are medical emergencies and notoriously painful. If left untreated for even a day, the potentially misplaced and sharp bone can cause further injury, and even life-threatening internal bleeding.
As plaster can be applied immediately, it is perfectly suited to deal with this emergency – whereas a 3D printed cast would require hours to scan, design and finally print. During this time, the patient’s fracture would be left untreated.
However, after their initial cast, patients can almost always expect to get additional casts made, including 3D printed ones.
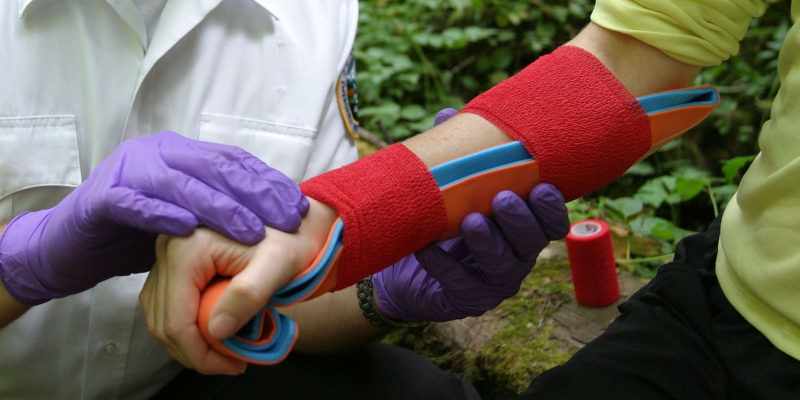
Replacement 3D Printed Casts
As the fracture heals, their doctors will have to regularly cut off their casts and make new ones. This is done to visually check on the fracture, ensuring that it’s free of infection and is healing properly.
Additionally, immobilized limbs will always become smaller over time, requiring new smaller casts to be made. This is because the swelling caused by the injury reduces over time, and because of the unused limb’s muscle atrophy.
Describing the process, Dr. Arun Sayal of the North York General Hospital in Toronto explained that:
“If the fracture starts to heal normally, you might be moved into a fiberglass cast… It’s a little harder to mold fiberglass, so often the emergency department will use plaster.”
These synthetic casts are so popular because they’re waterproof, allowing the patient to bathe normally.
But what about that 3D printed option?
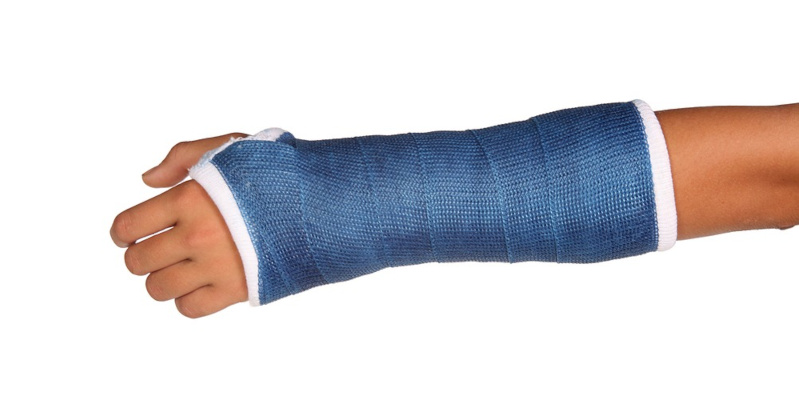
Active Armor Casts
Active Armor offers a range of custom 3D printed casts. As a medical device, a doctor’s prescription and agreeable insurance is needed to begin treatment.
Like all rigid casts, Active Armor cannot be used early in treatment. Instead, they are usually fitted once most of the patient’s swelling has gone. Although muscle atrophy will continue, it usually isn’t enough to make these rigid casts ineffective.
The process begins with the removal of the plaster cast and a scan of the injured limb. The doctor will verify the scan with a physical measurement, then the scan will be sent to a printer. The patient will get another plaster cast in the interim.
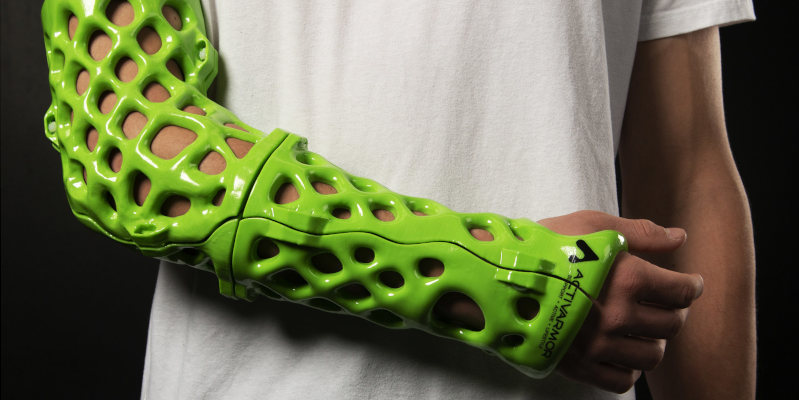
Once the manufacturer has printed and shipped the cast, it will be attached for the first time by the doctor, where they will do a final check to ensure that it has an effective and snug fit.
These 3D printed casts are significantly more comfortable than plaster ones. Their design leaves plenty of skin exposed. This is useful for doctors to observe the fracture healing, and also allows the patient to actually scratch their itchy skin. This also avoids the notorious smell that can arise from wearing waterproof casts for too long.
Read more: our feature story on 3D printing in medical
Additionally, 3D printed casts can be completely removed by the patient whenever they wish. In practice, there is little reason to do this whilst they are nursing a serious injury.
However, it does allow for more flexibility with washing, massaging muscles, cleaning the inside of their cast, and just allowing their skin to air.
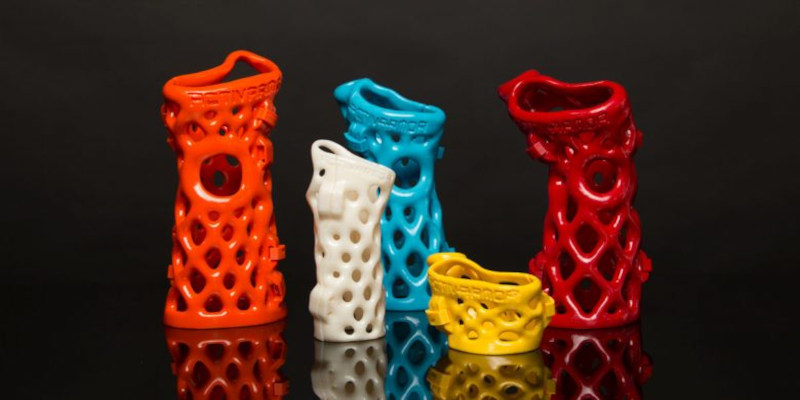
Limb Shrinkage?
3D printed casts are expensive, or are at least far more expensive than the comparatively disposable price of plaster casts. This becomes an issue when reminded that muscle atrophy will continue as the fracture heals.
Unlike plaster casts, 3D printed casts cannot be cheaply cut off and remolded. To combat this, most patients are advised to apply tape to the inside of their cast whenever an area becomes loose.
But aside from this, they’ll just have to hope that their fracture heals before their injured limb shrinks too much.
3. HeadStart Medical and Orthotic helmets
Despite looking like toddler-sized crash helmets, these are actually specialized orthotics.
Plagiocephaly, also known as “flat head syndrome,” occurs in about 1 in 5 infants. The condition is caused by infants laying or sleep in one position for too long, causing their soft skulls to become misshapen. This condition usually resolves itself over time, however parents may decide to explore orthotic treatment.
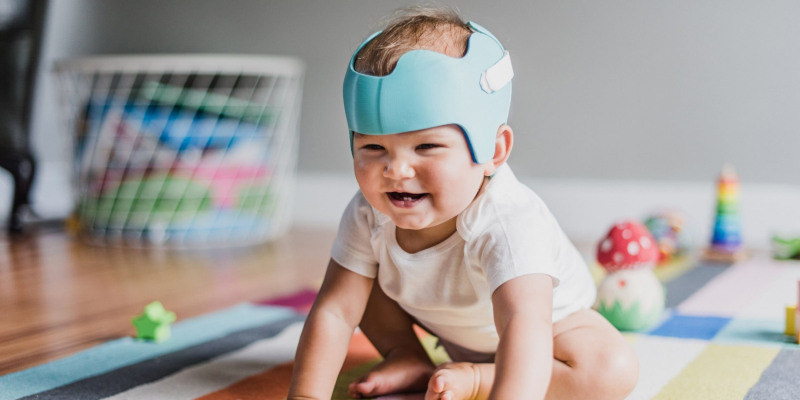
An orthotic plagiocephaly helmet, similar to oral braces, gently forces the infant’s head into a symmetrical shape, ensuring that it fuses correctly.
Conventionally, these helmets are all custom-made using measurements of the baby’s head.
However, 3D printing the helmets makes the production process faster and cheaper – but most importantly, 3D printing results in much lighter helmets. This reduced weight allows treatment to begin earlier, as the children’s head and neck don’t need to be as strong yet.
Starting earlier allows the treatment to be more effective, potentially reducing the impact of Plagiocephaly on an international scale.
However, despite the merits on display here, the treatment itself has come under criticism.
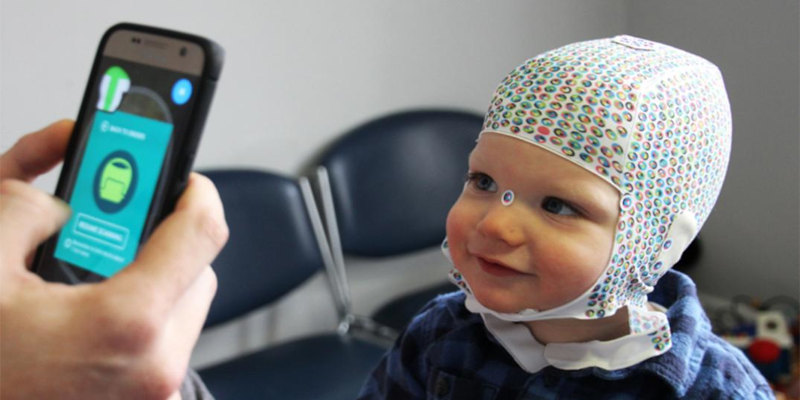
A Treatment Under Fire
The process can be invasive, with babies younger than six months having to wear the helmets for 23 hours every day. Additionally, as the babies grow, they’ll require regular doctor’s visits to shave down the orthotic. Predictably, this growth and constant rubbing usually result in moderate to severe rashes.
But perhaps the most damning criticism comes from the fact that it is unclear whether orthotic helmets actually work!
However, there is no clear government-led evidence suggesting that these helmets correct Plagiocephaly.
With the treatment usually costing over $1000 for the initial helmet, and then more for follow-up consultations, some may see it as a large investment for a condition that may resolve itself over time.