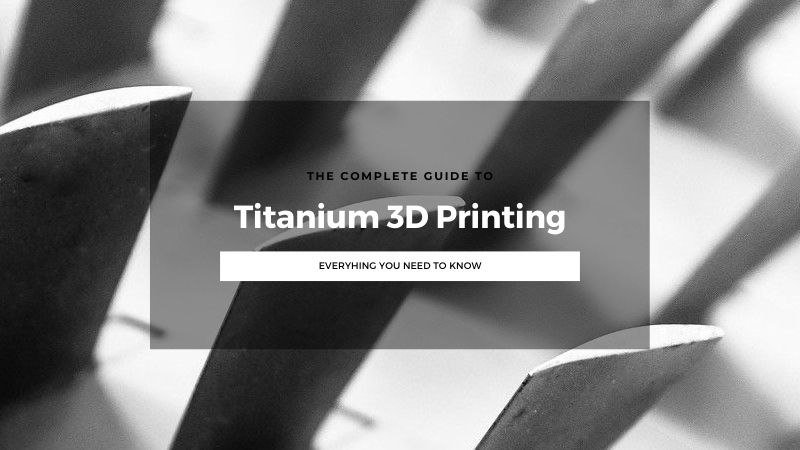
Why Titanium 3D Printing is Going from Strength to Strength
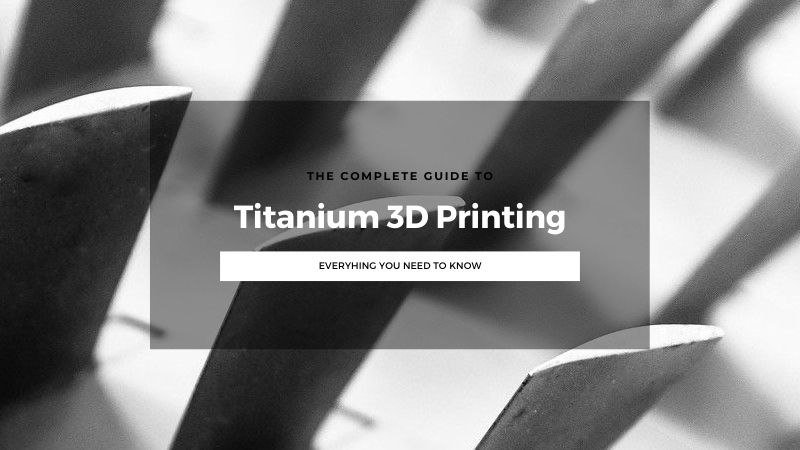
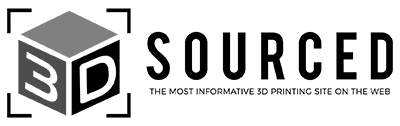
At 3DSourced we’ve covered everything 3D printing and 3D since 2017. Our team has interviewed the most innovative 3D printing experts, tested and reviewed more than 20 of the most popular 3D printers and 3D scanners to give our honest recommendations, and written more than 500 3D printing guides over the last 5 years.
As metal 3D printing continues to evolve, titanium is emerging as one of the most exciting printable metals. Metal 3D printing has opened up an array of avenues for manufacturing and rapid prototyping, with titanium becoming an industry favorite across a range of sectors.
Where 3D printing was once limited to plastic and resin, the emergence of 3D printing metal has changed the perception of what is possible.
Part 1: The History and the Science of Titanium 3D Printing
The History
Titanium has been a widely used material in manufacturing for centuries, being first discovered in 1791 in Cornwall, England. It can be found all over the world, with uses in medicine and construction making it integral to society.
Titanium is renowned for, and has become almost synonymous with, its strength. It has a remarkable strength-to-weight ratio, with commercial quality titanium being as strong as steel while weighing up to 40% less. What’s more, it is extremely corrosion-resistant with a very high melting point, making it among the most durable, yet common materials around.
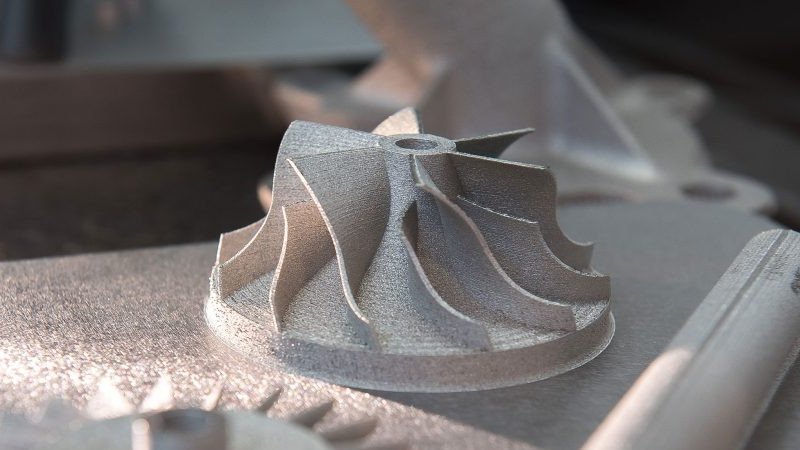
However, this often proved to be a crutch. Prior to the development of metal 3D printing technologies, titanium was typically manufactured using one of two methods: milling, or melting and molding.
Milling titanium involves using a CNC milling machine, similar to a drill, to cut into a block of metal, wearing away sections in order to fashion a product. This comes with a range of potential pitfalls, such as lots of waste metal, and being very time-consuming.
Melting and molding is exactly as it sounds: heating the metal into a molten liquid, and pouring it into a mold where it then cools and hardens. This too raises difficulties in the increased danger of the process, as well as the immense energy requirements to melt a metal with a notoriously high melting point.
This is where 3D printing comes in. In 2006, DARPA, the Defense Advanced Research Projects Agency of the United States military, awarded a $5.7 million contract to a consortium to develop new methods of producing titanium powder for numerous military applications. Specifically, they looked into aircraft and naval parts, armor plating and missile components. This development has become a central part of the titanium 3D printing process.
The Science
The most common titanium 3D printing technology is Direct Metal Laser Sintering (DMLS). Similar to most processes, a component is designed using 3D modeling software, and the printer constructs the image in layers, with the final product cured by a laser or with UV rays.
- We also have an in-depth article describing DMLS 3D printing.
With titanium printing however, a roller coats the baseplate in powdered metal. A laser then heats the material, melting it together to form a shape. The plate is then lowered slightly, with more powder deposited on top for the next layer to be formed.
DMLS offers a number of advantages over other titanium manufacturing methods. Firstly, the amount of wasted material is greatly reduced making it far more efficient.
It does come with its own problems, however, namely the increased possibility of striation. Striation occurs when 3D printed metal develops cracks or poor adhesion between layers during the printing process, which can undermine the structural integrity of the finished component. This has held back the development of more complex designs.
While there is still progress to be made in this sector, the promise already shown by titanium 3D printing is exciting.
If you are interested in purchasing a 3D printer for titanium printing, we may be able to help:
*One of our trusted partners will be in touch following a quote request.
Part 2 Applications of Titanium 3D Printing
Aircraft
Titanium is an invaluable resource in the aviation industry and has been gradually replacing aluminium for years. This is due to its high strength-to-weight ratio which improves the safety of the aircraft while minimizing weight, as well as its resistance to heat.met
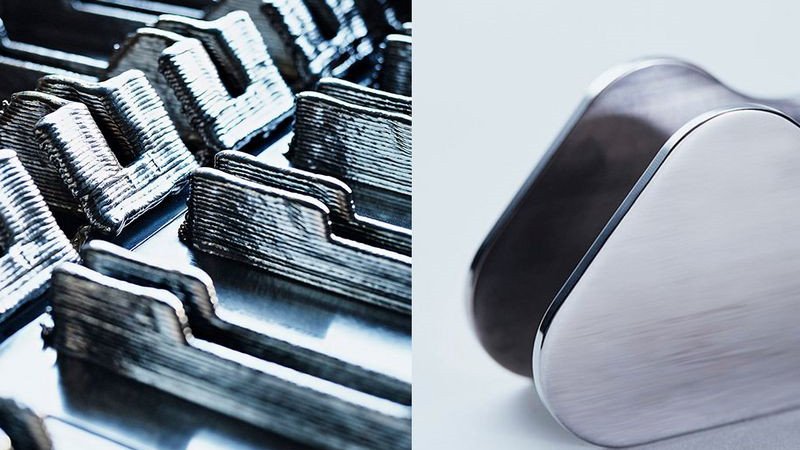
In commercial aircraft, titanium is now being used for constructing everything from small components and fittings, to the frame itself, and researchers are now experimenting with using it in the construction of turbine engines.
3D printing is starting to make headway in the industry too. In 2015, Boeing began using 3D printed titanium brackets in their 787 Dreamline aircraft, and Airbus are also beginning to incorporate 3D printed titanium brackets for their nose landing gear.
In commercial flight, weight is everything as even minute increases can exponentially increase fuel costs and reduce profits. The lighter the aircraft, the more money is saved.
Medicine and Dentistry
Orthopedic surgeons are beginning to use titanium 3D printing in patient care. A recent Smartech report states that titanium 3D printing in medicine will account for $520 million of revenue by 2022, and nearly $1.1 billion by 2026 in the private US market.
Surgical implants such as joints, bone fragments, or even plates and screws, use titanium for its corrosion-resistance and lack of toxicity. Titanium is one of the safest and most durable materials for medical implantation.
This is also true of the dental industry. The National Institute of Dental and Craniofacial Research estimate that 92% of adults between 20 and 65 have significant tooth decay in the United States, with dental fillings among the most common procedures performed.
Customized 3D printed titanium fillings save both money and time, and reduce patient discomfort. This is achieved through the customization creating better fits, and 3D printing reducing waste and improving manufacturing accuracy. Titanium is a large part of the revolution in medical 3D printing.
- We have also written a feature story on Medical 3D Printing.
Automotive and Motorsport
The strength and weight reduction attained by using titanium has caught the attention of car manufacturers, both commercially and competitively. The industry is, however, very conscious of its costs, meaning titanium 3D printing is not as commonplace as it is in aerospace due to the cost of the material.
- We have also written a feature story on 3D printing in the automotive industry.
- We also have a ranking of the most exciting 3D printed cars.
Despite this, a number of companies have experimented with the technology. The Italian supercar manufacturers Bugatti have begun using 3D printed titanium brake callipers in the production of the Chiron.
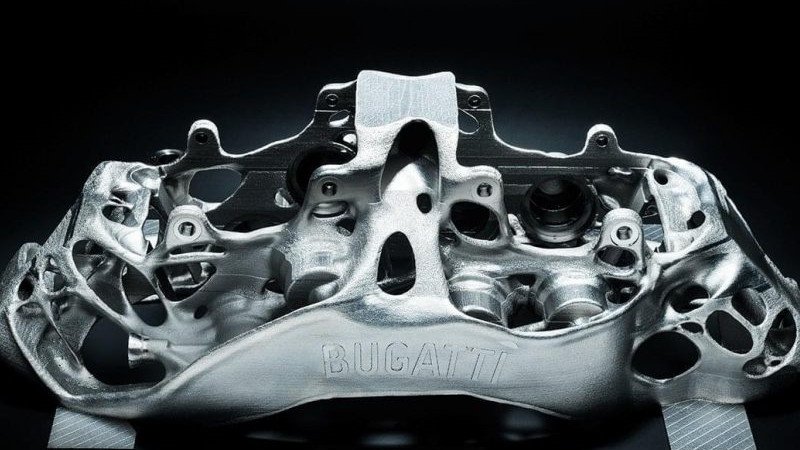
Famous for not just high-performance, but hyper-performance, Bugatti embracing the possibilities of 3D printing indicates just how confident experts are in the possibilities of the technology.
Part 3: Benefits and Limitations of Titanium 3D Printing
Benefits
Strong Material
Titanium has a much higher tensile strength than most naturally occurring elements, and certainly more than any currently usable 3D printable metals. This gives it a distinct advantage in its applications in certain sectors, such as construction and transportation.
In these areas where both durability and low weight is key, titanium is the perfect choice, and metal 3D printing processes are the best way to perfect manufacturing in the least wasteful and most cost-effective way, more so than traditional methods.
Light Weight
Titanium’s lower density gives it an edge where a heavier alternative would be impractical and expensive. The medical sector, for instance, needs its implants to be as light and unrestrictive as possible so as to cause as little discomfort as possible.
This is also beneficial in industries such as aerospace and automobiles, where weight increases lead to exorbitant fuel costs, and titanium is vital for keeping costs down.
Traditional steel implants have proven ineffective at this, and with 3D printing allowing for increased personalization, the industry has not ignored the potential.
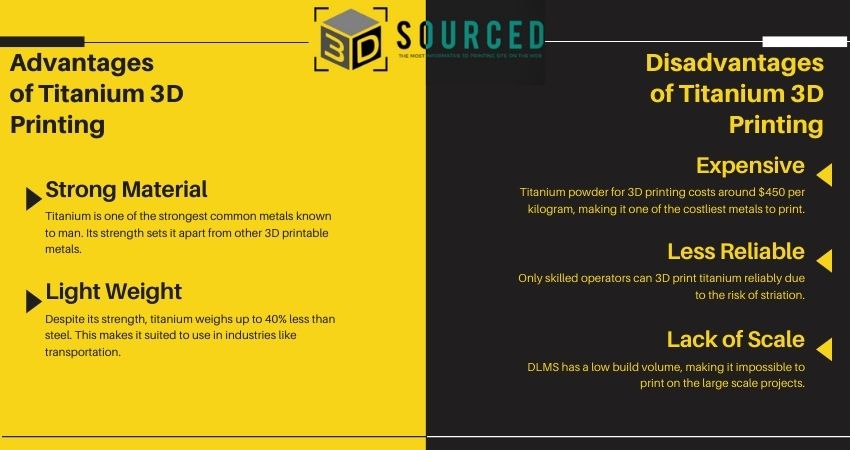
Limitations
Expensive
Unfortunately, just because it is common doesn’t mean it’s cheap. As the titanium needs to be optimized for the 3D printing process, added onto cost of extraction and purification, titanium powder will cost around $450 per kilogram. This is a key barrier to wider titanium 3D printing adoption, though costs have fallen over recent years.
Less Reliable
On a similar note, the difficulty involved in 3D printing titanium requires high skilled operators to produce a reliable product. And without proper attention, you could seriously undermine your own work.
More than other materials, titanium is extremely susceptible to striation, where cracks and separation can affect the product. These will make the part completely unusable in industries like medicine, where nothing less than perfection is acceptable.
Lack of Scale
The main aspect working against titanium 3D printing in its common form is the potential for scalable printing. The technology simply cannot function beyond printing small parts.
DMLS printers currently are limited to small build volumes, making them unsuitable for printing beyond small individual components. While new techniques are in development to change this, the reality is a handicap on the progression of titanium 3D printing.
Conclusion: What are the Possibilities for 3D Printing Titanium?
The current limitations mean that the possibility of large-scale titanium 3D printing is not reliable, but the development of new techniques could soon push back those boundaries and open new horizons for metal in 3D printing.
DMLS is the most accessible metal 3D printing technology, but recently, new progress has been made using an alternative called Direct Energy Deposition (DED). A similar technique, Rapid Plasma Deposition (RPD), was used by Boeing to produce the titanium bracket for their planes, and involves melting titanium wire with plasma.
The process was reportedly 50 to 100 times quicker than traditional construction methods, used up to 50% less material, and Boeing estimate the technique could reduce the cost of a 3D printed plane by $3 million.
A 3D printed aircraft is, strangely, far more likely than a 3D printed car. Despite the size difference, titanium’s price is a strong deterrent to car manufacturers as that cost is passed along to the consumer, and might discourage customers. Airlines do not have similar concerns and the decreased weight of the plane would trump the initial cost in the long run through lower fuel costs.
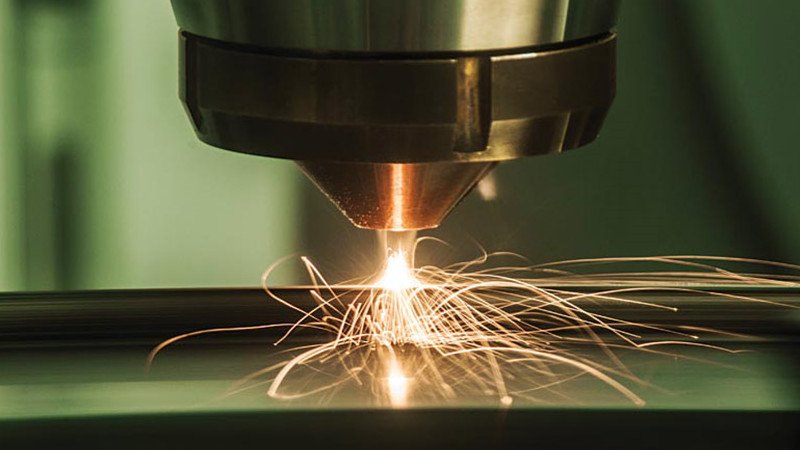
Similarly, the aerospace industry is another potential avenue of development.
We have discussed previously in our 3D printed meat article about the possible application of 3D printing technology in the construction of structures in space for human habitation, and titanium could be vital to this effort.
While steel is the popular construction material on Earth as it is equally as strong but cheaper than titanium, titanium’s lighter weight makes it far cheaper to send into space. A lighter material means greater quantities can be sent with each launch, bringing down costs and increasing construction efficiency.
While titanium 3D printing is not yet widely usable, the benefits it provides make it a promising development for the future. Despite the technical difficulty, skilled 3D printing manufacturers have already seen what titanium has to offer.