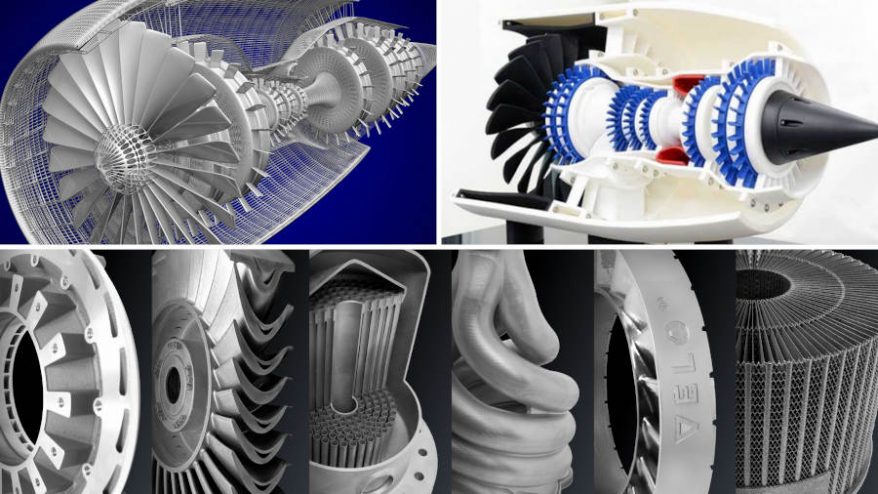
3D Printing in Aerospace: Everything You Need To Know
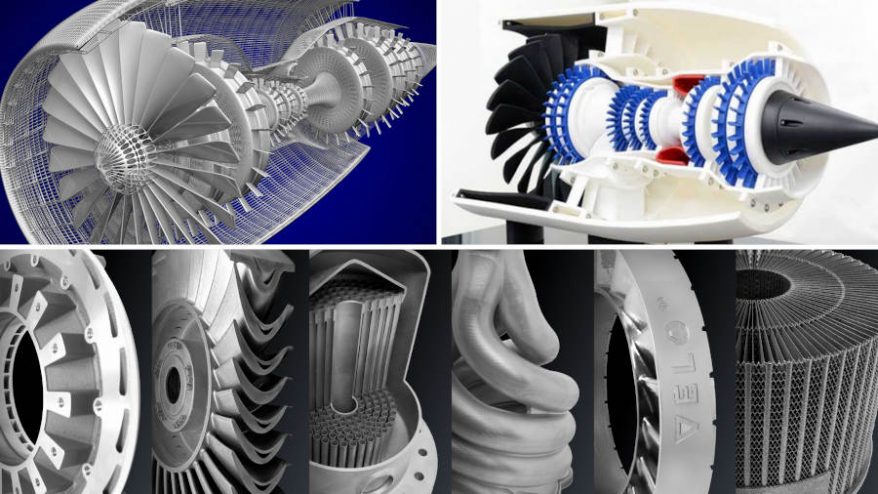
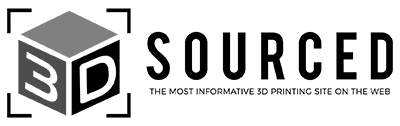
At 3DSourced we’ve covered everything 3D printing and 3D since 2017. Our team has interviewed the most innovative 3D printing experts, tested and reviewed more than 20 of the most popular 3D printers and 3D scanners to give our honest recommendations, and written more than 500 3D printing guides over the last 5 years.
The aerospace industry was an early adopter of 3D printing, reportedly using the technology as early as the 1980s. Aerospace has only continued to implement 3D printing into their production processes, and for good reason.
This is an industry where reducing drag by a few degrees, or reducing an aircraft’s weight by a few grams, creates enormous financial savings. Perhaps infamously, it was Robert Crandall, CEO of American Airlines in the 1980s, who suggested that removing one olive from every salad served would save his airline $40,000 dollars every year.
So, 3D printing can produce these often complex structures in a way that is faster, cheaper, and potentially lighter than traditional methods. Naturally, the industry paid attention.
But we also aren’t going on holiday in completely 3D printed passenger jets just yet. So, this begs the question, just how extensively is 3D printing used within aerospace today?

The Advantages – 3D Printing and Aerospace
Like in many industries, adopting 3D printing allows manufacturers to produce complex parts faster, cheaper, and more accurately than conventional methods. But the technology isn’t suitable for everyone, with manufacturers who produce simple components, or enormous runs of products, benefitting less from 3D printing’s advantages.
This is not true of aerospace however. With the complexity of its components, and its emphasis on efficiency and saving weight, 3D printing offers significant benefits, just like in our first example.
Avio Aero
Not content with simply getting by, Avio Aero has challenged themselves to also improve and innovate upon their aircraft designs.
“Avio Aero’s challenge is to develop new technologies and applications to reduce fuel consumption & CO2 emissions, produce lighter aircraft, and achieve better performance.”
And to achieve this, they’ve turned to 3D printing.
Operating out of purpose-built factories across Europe, Avio Aero has confidently adopted 3D printing into its manufacturing process. In fact, one of their industrial plants in Cameri, Italy, was also the largest 3D printing factory in the world when it was built in 2013. It features over sixty 3D printers, and two gas atomizers to produce metal 3D printing powders in-house.
Previously, Avio Aero had manufactured their products using traditional casting, and had much to say about the benefits of switching to 3D printing.
“Products are uniform… Mechanical characteristics are better; pieces are more resistant… Manufacturing is carried out in vacuum chambers with no harmful exhaust emissions. Moreover, to make a product weighing 1 kilogram through casting, about 4 kilograms of material is needed. While only a maximum of 1.5 kilograms is used with additive manufacturing [3D printing].”
With the technology’s benefits explored, let’s take a step back and look at how it is actually incorporated into the production of aircraft.
The Design Process for Aerospace 3D Printing
Rapid prototyping is an increasingly common use of 3D printing, with many large industries making use of the technology to produce models and test runs of new products or components.
The aerospace industry differs slightly then, in the fact that 3D printing here is used throughout their entire design process, right up until and including the manufacture of the final components.
This of course includes the traditional uses of 3D printed prototypes, such as scale models. But what about those less common pieces more specific to the industry?
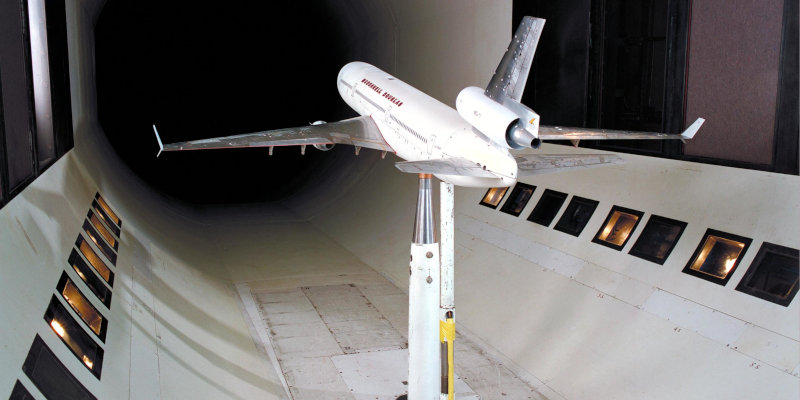
Surrogates?
One such area is that of 3D printed surrogate parts. These parts are cheap, but highly accurate replicas of very expensive aircraft components. These surrogates act as placeholders for aerospace training rooms, or as placeholders on a production assembly line. For example, during the production process of Bell helicopters, a surrogate wiring conduit is used when assembling the aircraft’s tail. Technicians will use these surrogates to test all the wiring paths before the real piece is installed.
This specific case saw significant improvements too, with Bell claiming that these 3D printed surrogates were produced in only two and a half days; far quicker than their previously used aluminum surrogates, which took six weeks to build.
With such savings, the question could again be asked, why stop at surrogate parts? Well, the answer is that they haven’t. In fact, modern passenger jets probably already feature more 3D printed parts than you may expect.
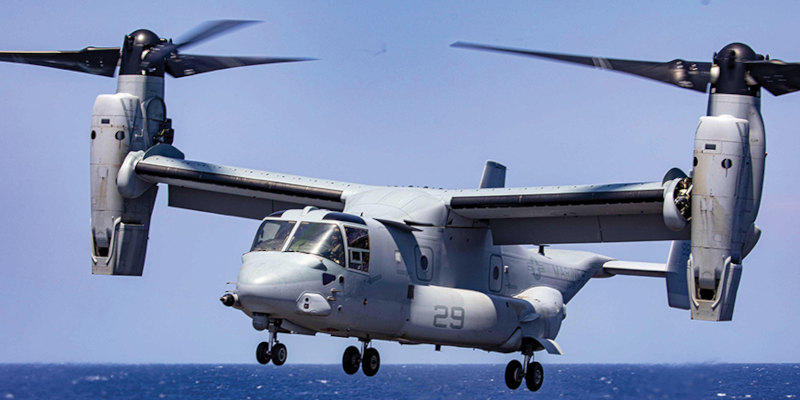
Integrating 3D Printed Parts Into Aircraft
Currently, commercial aircraft either already feature, or have the option to replace many of their components with, 3D printed counterparts.
Nozzles, control consoles, aircraft doors, and even headlights can currently be 3D printed. A variety of 3D printing techniques and materials are used too, allowing the industry to produce parts out of metal, resin, nylon, and even composites. For example, material jetting, a technique where the material is applied in layers and cured with UV light, can be used to create aircraft headlights.
Custom 3D printing manufacturer Hubs (formerly 3D Hubs) even released a list of recommended materials and use applications specifically for 3D printing aerospace components.
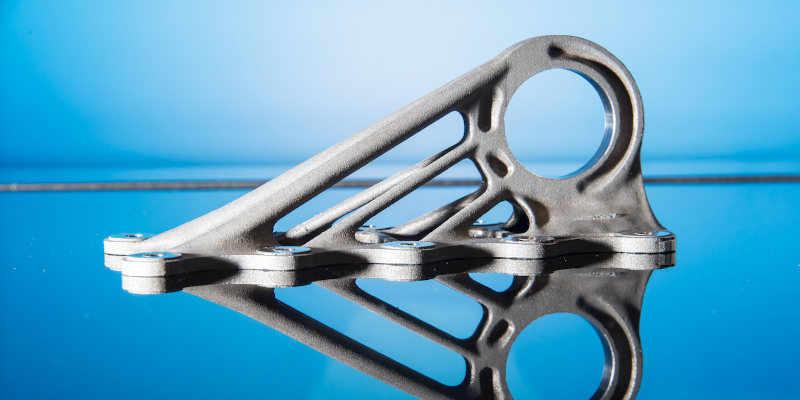
Although this is an exciting development, it’s worth being tempered with the fact that 3D printing is not currently the most effective way to produce entire aircraft. This is for two reasons.
First, and perhaps most simply, not all aircraft parts can currently be 3D printed. This is especially true for more complex mechanical components.
Additionally, although 3D printing has proven itself to be invaluable when producing low-to-medium level production runs of components, the technology struggles to keep up when dealing with massive volumes. In these cases, conventional construction methods either outpace, or aren’t significantly behind the production speed of industrial 3D printers, casting doubt over the benefits of completely retooling.
This doesn’t mean that 3D printing hasn’t seen an unprecedented level of integration however, with some of the biggest names in aviation standing behind the technology
Boeing & GE Adopting 3D Printing in Aviation
GE Aviation’s GE9X engines are currently the largest commercial jet engines available today. In each engine, more than 300 3D printed parts are used. In addition to the cost and weight benefits, 3D printing also allowed the company to implement otherwise impossibly complex designs into the engine.
In a marketing video, GE Aviation claimed that “you’ll also use advanced manufacturing techniques like 3D printing to build components that were quite simply impossible to make until now.”
The use of 3D printing here, in addition to their own engineering, means that not only is the GE9X the largest jet engine available, but it is also the most efficient!
The engine was developed specifically for Boeing’s new 777x aircraft, set to be introduced to their fleet in 2024. After successfully completing its first flight in 2020, Boeing described their new aircraft as being:
“The world’s largest and most efficient twin-engine jet, unmatched in every aspect of performance. With new breakthroughs in aerodynamics and engines, the 777X will deliver 10 percent lower fuel use and emissions and 10 percent lower operating costs than the competition.”
Although we can only speculate for now, the achievements 3D printing has been able to bring to this engine, surely indicates its continued adoption throughout the industry.
Airbus & The Future Of 3D Printed Aircraft?
Although we’re not quite ready to produce 3D printed passenger jets just yet, Airbus’s recent projects have also left some speculating as to whether 3D printing could soon bring about sci-fi levels of innovation to the industry.
Despite being slow to begin using the technology, Airbus is now one of the boldest advocates for 3D printing within the industry. Their A350 XWB airframe now features over one thousand 3D printed parts, including fully 3D printed landing gear brackets.
However, what is perhaps most exciting, is their eVTOL (electric take-off and landing) vehicles. Or, to put it another way, their flying taxis.
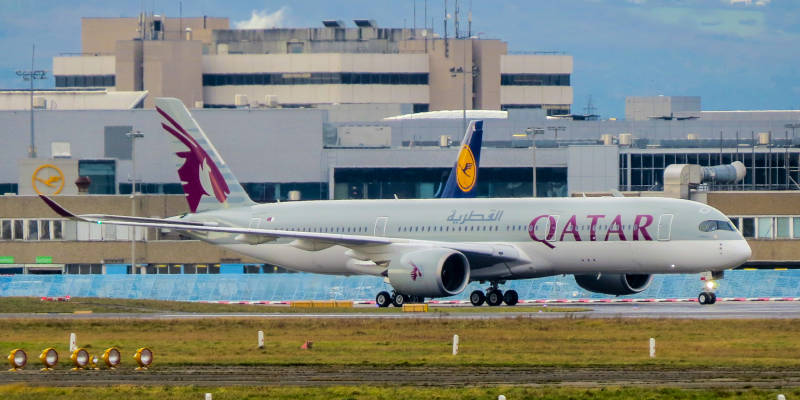
3D Printed Flying Taxis
The CityAirbus project vehicles are concept demonstrators. Airbus’s aim is to revolutionize urban mobility by moving road traffic from the ground and into the sky.
On the project’s website, Airbus states that:
“The idea for a compact ‘flying taxi’ first came from our desire to take city commuting into the air in a sustainable way… We are on a quest to co-create an entirely new market that sustainably integrates urban air mobility into the cities while addressing environmental and social concerns.”
And progress seems to be going well, with their first-generation vehicle successfully completed its first autonomous flight in 2020.
The vehicles feature no pilots, instead being remotely controlled by what will eventually be a city-wide air traffic controller.
Interestingly, Airbus has not widely released full details of how their CityAirbus drones are produced. However, this hasn’t stopped strong speculation that the CityAirbus drones make heavy use of 3D printing in their design.
Notably, Castor, a company that provides software solutions for industrial 3D printing manufacturers, reported that not only were the CityAirbuses 3D printed, but that they were also produced in partnership with Local Motors Group.
And not without cause.

Airbus is indeed partnered with Local Motors, with both companies even hosting the Airbus Cargo Drone Challenge in 2016. Here, entrants could enter cargo drone designs, with the winning design being given the chance to be manufactured.
Additionally, Local Motors specializes in 3D printed vehicle manufacturing. In fact, they are best known for their “Olli” self-driving 3D printed car. Much like CityAirbus, Olli was conceived out as a desire to produce more accessible and sustainable ways of getting around urban environments.
Ultimately though, these parallels will remain as speculations until Airbus reveals otherwise. What this project definitely does show us however, is that 3D printed passenger vehicles do hold the attention of the aerospace industry’s biggest players, and that 3D printing and aerospace are a burgeoning match made in the skies.