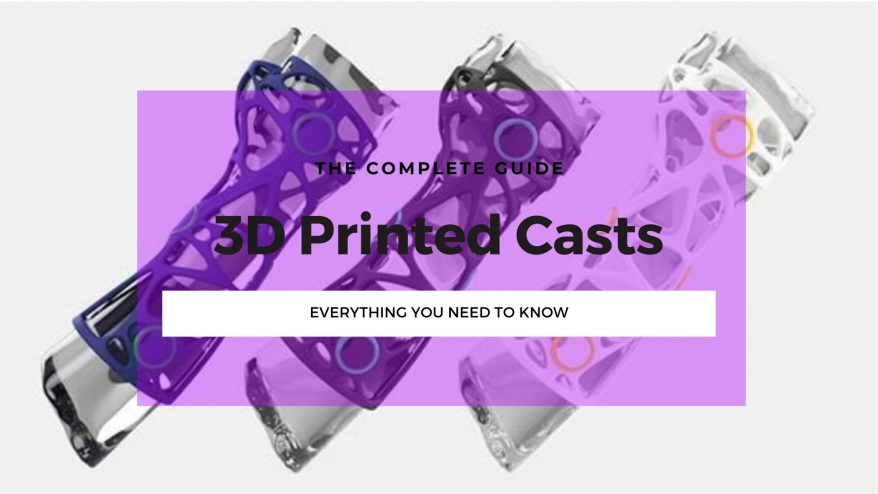
How 3D Printed Casts Are Fixing Our Broken Systems
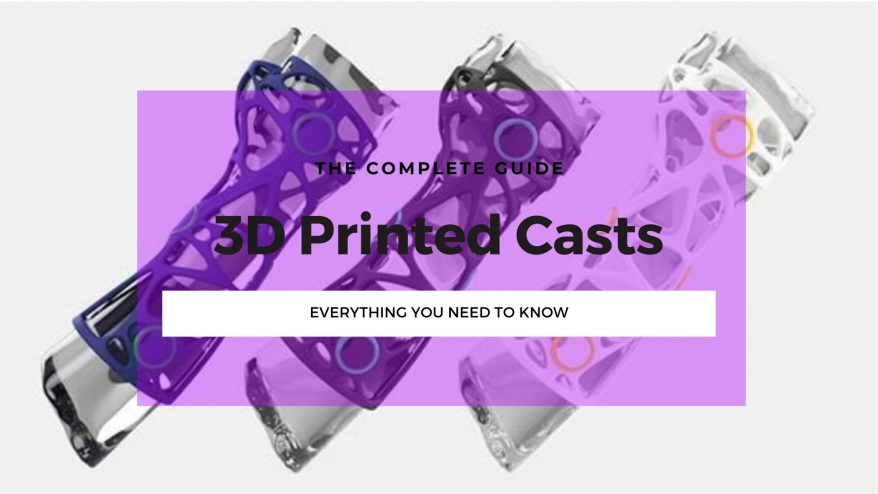
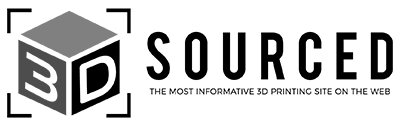
At 3DSourced we’ve covered everything 3D printing and 3D since 2017. Our team has interviewed the most innovative 3D printing experts, tested and reviewed more than 20 of the most popular 3D printers and 3D scanners to give our honest recommendations, and written more than 500 3D printing guides over the last 5 years.
3D printed casts have begun to fix a broken system — our human bodies. Whereas traditional methods of fixing fractures have worked well, we are beginning to see a modernized revolution with 3D printing.
Orthopedic casts are used for helping the healing process of broken bones. Acting essentially as stints, they fix limbs in place to prevent the bone from healing abnormally.
Modern casts are made primarily of plaster or fiberglass, and the earliest recordings of this were seen during the Crimean War. Surgeons would use Plaster of Paris as a quick method of setting soldiers’ broken bones on the battlefield. This then began to find mainstream medical adoption in the early 20th century.
Today, standard casts are produced by applying specialized cotton bandages that have been coated in Plaster of Paris. When soaked in water, the plaster begins to harden. Application can take as long as 45 minutes and the cast can take between 24 to 72 hours to fully set.
Removal of the cast is also an arduous procedure. The hardened plaster can only be safely broken by cutting with a specialized electric saw. This has its own set of risks, and highlights one of the biggest shortcomings in modern medicine.
Part 1: The Development of 3D Printed Casts
Naturally, there is much room for improvement in this system, and 3D printing visionaries have seen the potential for additive manufacturing to fix these problems.

Some of the earliest 3D printed casts were introduced in 2013, among them the Cortex Cast, engineered by brothers Jake and Ollie Evill.
Most 3D printed casts are produced in 3 steps:
Step 1: X-ray
A standard x-ray is taken of the patient’s limb to identify the exact position of the broken bone.
Step 2: 3D Modeling
The patient’s arm is scanned using a 3D scanner to create a 3D model. Based on the exact dimensions of the patient’s arm, a perfect-fitting cast shape can be made.
Step 3: Printing
Using strong but lightweight plastic, the cast is 3D printed and can then be fitted to the patient in seconds.
Despite being around for close to a decade, 3D printed casts have yet to see significant adoption. This is mainly due to a lack of concrete data on the practical benefits of the casts, but that has begun to change.
A 2020 study by Chinese researchers compared 3D printed casts for arm fractures against traditional plaster casts and external fixed splints. The results showed that, when compared to plaster casts, 3D printed casts scored highest for comfort and lowering pain.
Now, we are starting to see 3D printed casts become more common, with Children’s Hospital Colorado announcing that they are the first pediatric institute in the United States to offer 3D printed casts to children.
3D printing is showing yet again that it has the potential to improve care and patient outcomes, and push back the restrictions of previous medical methods
Part 2: How 3D Printed Casts Are Improving Outcomes
While plaster casts have been a useful development for the treatment of broken bones, there are a number of significant drawbacks that have been overcome.
Ease of Fitting and Removal
Applying a plaster cast can be a long, laborious and sometimes messy process. It requires a lot of careful and precise measuring, and the manual application of bandages can be painful if not done carefully.
3D printing overcomes this. Once the cast has been printed, it can be quickly and easily fitted in a matter of seconds with a couple of clips to hold it in place.
Removing the cast is similarly simple, and does not require dangerous electric saws to cut away layers of hardened plaster and fiberglass. The entire process is safer and more streamlined.
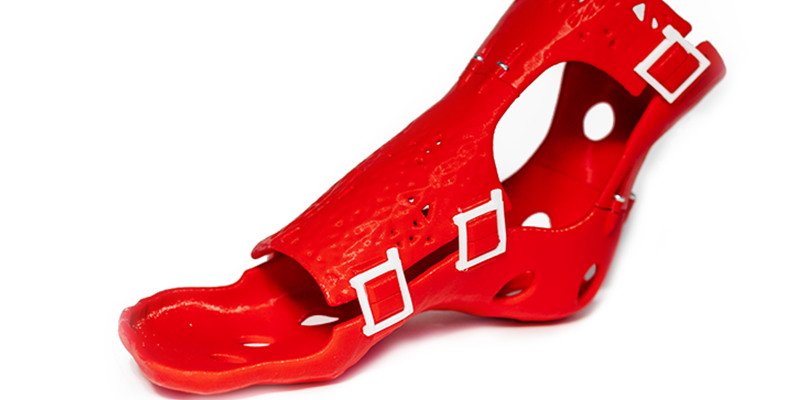
Breathability and Infection
One significant drawback of plaster is that it is not breathable. The solid plaster prevents air contact with the skin. This can lead to blocked pores, and some patients can develop nasty skin infections in wounds. What’s more, the constant warmth, sweat and pressure can cause very uncomfortable itching.
However, 3D printed casts are made using a lattice. The plastic is built with large open sections, with the plastic struts providing the necessary structure without completely covering the arm. This is one of the biggest factors contributing to the higher comfort rating for 3D printed casts reported in medical studies.
Waterproof
A frustrating issue for cast-wearers is you cannot get it wet. Be it in the rain, the bath or the shower, you have to take extra care to avoid soaking it as this can affect its strength.
Almost all 3D printed casts are made using waterproof plastic so you don’t have to hold your arm or leg outside the bath in order to wash. Some even say you can go swimming wearing it, so the fun doesn’t have to stop either.
Personalization
Perhaps the biggest hinderance to plaster casts is that while each cast is tailored to your arm, the method for how it works is a one-size-fits-all approach. Their crude application means that pressure is often applied unevenly across the limb, slowing the healing process.
What is fantastic about the lattice design of 3D printed casts is that they can be custom-designed. The lattice can be designed to add strength to the specific areas that need support, and sparser elsewhere. This personalized approach maximizes recovery speed and comfort for each patient.
Part 3: The Best 3D Printed Cast Projects
Cortex Cast
New Zealand-born engineers Ollie and Jake Evill developed the Cortex Cast in 2013, among the first 3D printed orthopedic casts in the world. The cast is lightweight, breathable, highly technical, and provides localized support for broken bones that was not previously possible.
Their work earned them 2nd place at the International James Dyson technology awards, with their vision for design leading them to work as designers on the recent Hollywood blockbuster Blade Runner 2049.
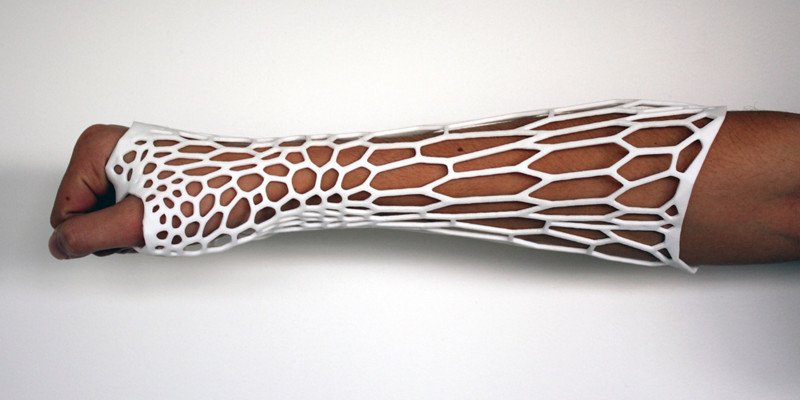
CastPrint
CastPrint is a 3D printed cast business established in Latvia by entrepreneurs Janis Olins and Sigvards Krongorns. What makes them special is that not only have they developed casts for regionalized sections of the arm: wrist, thumb and fingers, but they are also among the first to produce 3D printed casts for leg injuries as well.
They have expanded their business to the point that their technology is commonplace in the Latvian healthcare market, and in the last year have expanded into the United Kingdom, with several private healthcare firms incorporating their casts into everyday practice. Sooner rather than later, CastPrint will surely dominate across the continent.

Xkelet
Xkelet have pushed 3D printing casts into the fast lane. Not satisfied with their current 2-hour completion time from scan to production, their COO Tim Dobrinich wants to reduce that to just 12-30 minutes.
The Spanish startup uses a specialized camera attachment that they fit onto an iPad. Using their app, they photograph a patient’s limb from every angle, and can produce a cast model in seconds, eliminating the need for lengthy 3D scanning and modeling.
See also: the best 3D scanning apps for iOS and Android.
Xkelet casts have a design that uses anchor points called o-rings, which can allow them to re-cast the same injury multiple times, making their product reusable.
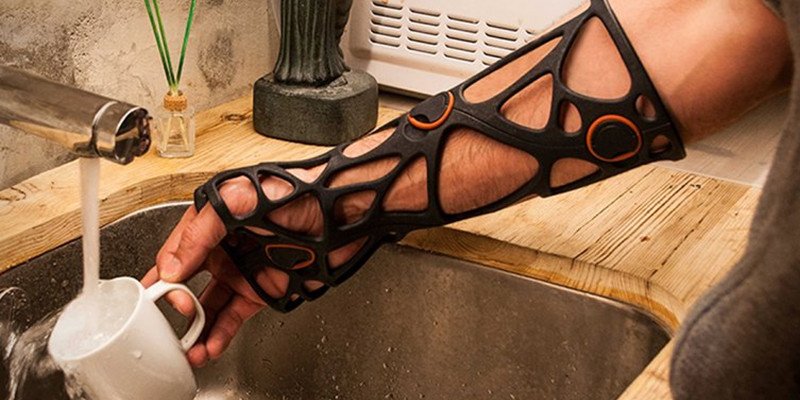
Part 4: The Pros and Cons of 3D Printed Casts
Benefits of 3D printed casts
Cheaper
3D printed cast treatment is far cheaper than with plaster. CastPrint’s personalized casts cost around €100 ($118), whereas, according to National Health Service data from the UK, the per patient cost of plaster casting was on average £727 ($1000).
3D printing is a much more financially efficient option due to the reduction in the cost of the material, and requires less time with a specialist.
More Comfortable and Personalized
The design of 3D printed casts makes targeting injured areas much easier than the blanket application of plaster bandages, helping the healing process.
The 3D printed casts’ open lattice structure also improves breathability and comfort, especially helpful when treating children. The casts are rugged and lightweight, crucially not restricting movements so cast wearers can still join in activities that were difficult with traditional casts.
Reusable
Another way in which costs are reduced is through the reusability of some 3D printed casts, particularly Xkelet. By being able to recast injuries using the same cast and structure, less material is required, and making the process far quicker and more convenient.
This ability allows care to develop throughout the healing process, assuring the absolute best outcome possible. Certainly more so than the costly, albeit rare necessity for multiple plaster casts.

Disadvantages of 3D printed casts
Not Enough Data
For a long time, there was very little data to establish whether 3D printed casts were more effective at treating injuries than their plaster competitors. Even now, with more studies being conducted and the data pointing in the right direction, medical consensus has still not been achieved.
For this reason, widespread adoption cannot take place without concrete agreement based on data. It will take time for the evidence to prove how effective 3D printed casts are. But for now, we can only wait.
Leg Injuries Still Not Widely Treatable
While CastPrint have developed casts for leg injuries, there are only a few companies in the world that do so. Even then, the designs may still be solid and lightweight, but are still bulky and resemble traditional walking boots.
These are not very convenient as they make wearing socks and shoes difficult, and are comparatively larger and more restrictive than their arm-based counterparts.
Conclusion: What’s Next for 3D Printed Casts?
One of the next challenges to overcome is expanding the technology to cover whole limbs, rather than just the hands, wrists, feet and ankles that current models do. Industry leaders are looking to develop arm casts that extend beyond the elbow and up to the shoulder and bicep, as well as up to the hip for leg casts.
Some of the most devastating and difficult to treat injuries occur in these areas, primarily through car and motorbike accidents, and the casts we currently have available struggle with the worst injuries.

3D printed casts are currently available around the world in the private healthcare market but those receiving government-funded health coverage are unlikely to ever hear about them unless they have prior knowledge.
Perhaps this is due to the lack of definitive research that would leave governments liable should hasty decisions lead to bad outcomes. Hopefully, that data will soon be in and irrefutable.
As we have already seen, 3D printed casts are a much more cost-effective treatment than the alternative, with greater patient satisfaction.
If you’re still in doubt about 3D printed casts, it won’t be long before you’ll have to snap out of it.
Other articles you may be interested in: