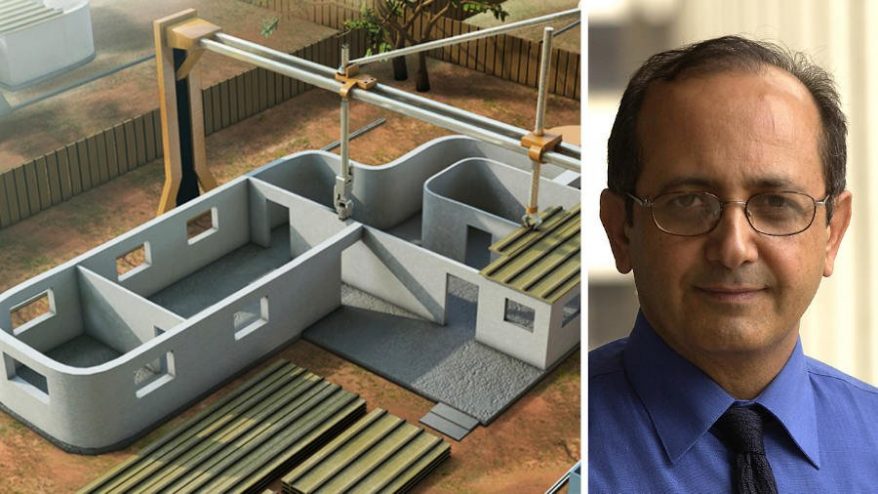
Dr Behrokh Khoshnevis: on the 25-year journey to bring Contour Crafting & construction 3D printing to the masses
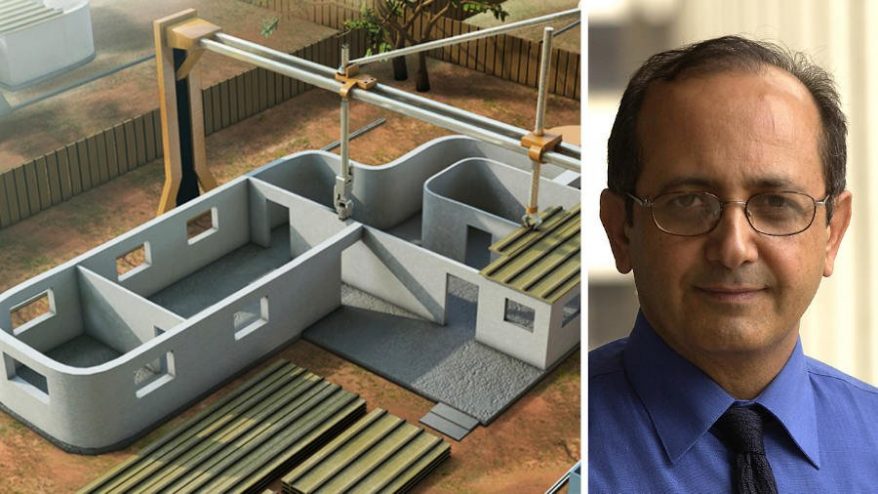
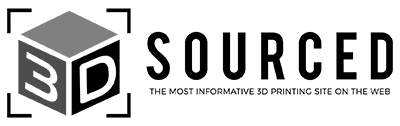
At 3DSourced we’ve covered everything 3D printing and 3D since 2017. Our team has interviewed the most innovative 3D printing experts, tested and reviewed more than 20 of the most popular 3D printers and 3D scanners to give our honest recommendations, and written more than 500 3D printing guides over the last 5 years.
The tale of Behrokh Khoshnevis, and of Contour Crafting, is one of steely resilience and determination. It’s also a tale of numerous setbacks, precocious vision, economic collapse-forced pivoting, and now, almost 25 years on, vindication.
Seeing Dr Khoshnevis’ achievements on paper, you could be forgiven for deducing that this was a glittering professional and academic career without any serious antagonist. Holding over 100 patents (the most of anyone in the field), winning two NASA International Grand Prizes in 3D printing in 2014 and 2016, and having invented a metallic 3D printing technique licensed to American giant HP, you might think this was just the work of a steady genius; a comfortable academic chipping away at the marble block of global innovation.
Peer behind the curtain, however, and the story of the father of construction 3D printing — and his company, Contour Crafting — is far more tumultuous.
We had the opportunity to speak with Behrokh Khoshnevis about the early beginnings of his vision, the difficulties with its development and navigating the political world of university research funding, moving into space for interplanetary 3D printing with local in situ materials, and finally, bringing the technology and construction 3D printers to market.
- If you enjoyed this interview, you can read more in our feature story covering 3D printing in construction.
Note: the interview transcription has been edited slightly to improve readability. No changes have been made to the verbiage.
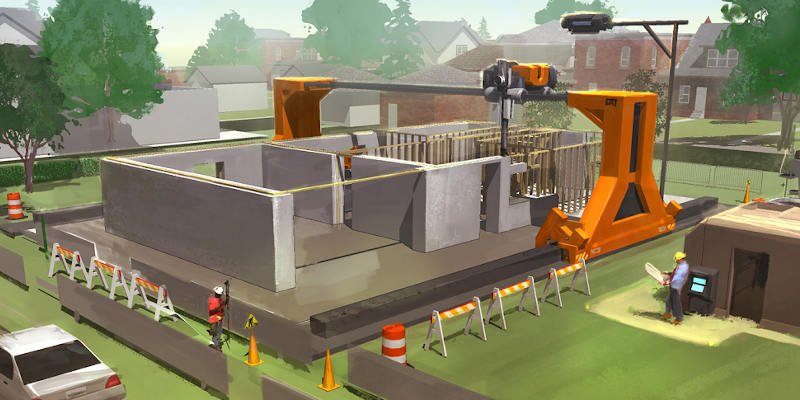
“In 1994 I started thinking about large-scale fabrication with 3D printing. I wasn’t happy with the speed of fabrication of the early 3D printers, and still they haven’t changed much as far as speed is concerned. I knew there was no other way to increase the speed of 3D printing than increase the layer height, but if you increase layer height then surface quality will suffer.
“So then I came up with the idea that I call Contour Crafting, in 1994. My first patent on it was issued in 1996, a couple years after.
“I started with polymers. The concept of Contour Crafting was pretty simple in reality. Back then, FDM was already there, Scott Crump had come up with that. But that was for plastic filaments. The challenge of extruding composites was different.
“The second problem was I wanted to print with very thick layers, and I wanted to maintain very smooth surfaces. So the amount of innovation I put in there was significant enough to really call it another process altogether [to FDM].
“I was originally investigating methods of building big sand molds for propellors of ships and submarines, and large aerospace tooling.
However, realizing the potential of the technology to create shelters for populations decimated by natural disasters, he focused his efforts on housebuilding.
“When you’re working in a university you have to bring your own research money, they will go so far in giving you seed money, but you cannot always depend on that. And especially for this kind of research I needed a big laboratory, but getting the resources to justify having a big lab in a university campus that is nearly in the heart of the city, very near to downtown Los Angeles… land is extremely expensive.
“There is always competition among faculty for space, so it has been a difficult path. It’s really troublesome when you find a spot and you start building something and a few months later they [the university] ask you to move to another location. I switched three times.
“Anyone who brought more to pay for the overhead of the university, they had the priority, and that’s understandable.”
Dr Khoshnevis
“Then you have to work with transitional students and the kinds of research at the earliest stage was pretty cumbersome, mixing concrete, it’s not a very pleasant research activity to involve graduate students, and just cleaning the whole thing was a big mess.
“Every day after experiments, lots of the time concrete would cure inside devices we had spent so much time building, so we had to throw everything away.
“It was a different kind of research, not like a desktop machine like I worked with in regular small scale 3D printing, it is definitely not the job of one or two people to do the experiments and everything even if you have the machine there already, and we had to build the machine from scratch! But it was surely a journey with a lot of adventures in it.
“We [managed to first accurately extrude concrete] around 2003. And in 2004 my work became very famous, in the New York Times… and that’s when the world learned about [Contour Crafting], and it inspired a lot of others to go after it.
“So I had to also chase the money. In 2008, 2009, real estate went down… and with it went construction, and the support I was getting from industry disappeared. So that’s when I started thinking about space.”
Without funding or support, a project of such magnitude could not maintain itself.
Yet, fully believing his idea of construction 3D printing could change the world, Dr Khoshnevis expanded his vision beyond our planet.
The idea was deceptively simple: if we could print concrete on a 3D printer on Earth, an adapted version could be made that could print with locally-sourced lunar regolith to create Moon (or Mars) bases for permanent settlements in the near future.
It costs an eye-watering $10,000 to send 1lb into space, so shipping the materials to build shelters for astronauts won’t work. Sending a construction 3D printer to print harvested lunar materials, however, could save billions.
Khoshnevis’ Contour Crafting methods were tested, simulating microgravity environments and using materials that mimicked the properties and difficulties of genuine lunar soil.
The 2014 NASA Grand Prize victory followed, receiving $20,000 to further the idea.
As of now however, Khoshnevis does not currently work or focus on the space applications of construction 3D printing.
“Because of my preoccupation with the company I have halted my activities for space. But I keep myself informed about it and we desire to get into space applications in the near future.
“We demonstrated at least two technologies that are viable. Technologies for building vertical structures such as hangars, shade walls, radiation protection walls, blast protection walls, and horizontal structures most particularly the landing pads, roads, we demonstrated the feasibility of those entirely to be made with in situ material.
“We actually built… and demonstrated it, that’s why we got Grand Prizes from NASA. My hope and expectation is that those technologies will eventually be used for planetary missions.”
No longer focusing on NASA and space, it was back to housebuilding and construction on Earth. The housing market, and confidence in it, had recovered. It was time to un-pivot.
And others saw the potential. Doka Ventures, a wing of Austrian construction company Umdasch Group, bought into the vision, taking a 30% share in the newly formed Contour Crafting company.
“In 2017 I received investment from a reputable European multinational construction company [Doka Ventures]. We started this company and our mission became looking closely at the real implementation issues and solving the remaining problems, difficult problems that once solved would make the technology maybe easier to use and more appealing to use.
“I don’t think that competing with conventional construction is a trivial change, it’s a major challenge. There’s a lot of hype about 3D printing, especially in construction.
“Since my first demonstration many years have passed, and yet we see that the technology has not taken over the world, right? It’s not a mainstream construction approach — one here, one there.”
Referencing other companies’ recent housebuilding demonstrations, he says:
“There’s not much information specifically about what the cost of building that construction was, and how long it took, what was involved in setting up the system on site, and what kind of talents and number of people were engaged in that construction activity, what were the logistics problems associated with it — we don’t hear much of those. So, unless there is an accurate assessment of any technology, there will not be necessarily a justification for the market to absorb it.
“So those have been the types of concerns I have had since when I started the company.
“3D printers…can only build the shell of the building. This is only maybe like 15-25% of the entire building. So all this hype really about 3D printing really solving the building construction problem really is not warranted. There is a lot more that should go into the building. My vision, as is reflected in my early patents, was to combine 3D printing with a lot of other robotics operations in order to build a more complete building.
“The technologies I developed 15, 16 years ago, are still the most advanced among large-scale 3D printing methods I see around the world.”
And though regulatory issues until very recently have plagued the development of 3D construction printing in the USA, Contour Crafting has carved an effective niche selling a custom-made, portable 3D printer to the government.
“We have released our new product, the first units of the product has gone to the government, they contracted us to build this machine.
“It’s a highly transportable machine, like a transformer, can quickly set it up on site. So, these are just different than straightforward gantry machines, so those are the areas in which we have worked. We have innovations in material processing, delivery and all that.”
The US Department of Defense funded the development of this custom 3D printer in July 2018, the CrafTrans. The CrafTrans is a sub-1,000kg rapid prototyper that fits snugly onto a truck and can be quickly unloaded and deployed in both military and civilian situations. It was delivered in December 2020.
So, despite rocky beginnings, being moved from laboratory to laboratory to accommodate perceived more fruitful research projects, and a financial and housing crisis just as the technology was getting off the ground, Khoshnevis showed that with the perseverance and creativity to pivot and the grit to keep looking for opportunities, you can win in the end.
“The reality is that I never gave up, I never gave up on it. Although I had other very intriguing projects, this was the most difficult one — the most cumbersome one — I never lost hope in it, and I still haven’t lost hope.
“I am doing as much I can to advance the technology, and what is important to me is really the journey. The destination is not in our control always, we just carry it so far as long as we can while we are around, and that is my philosophy in life.
“The important thing is to just move, when you have an idea keep on moving, and then you run in to opportunities, that movement teaches you a lot of stuff, rather than just sitting back and contemplating. That’s being a dream-weaver, not a creator. A creator always moves and makes things happen.”
And after two decades of being hardworking creator, the sands are finally shifting in favor of experienced Dr Khoshnevis. After decades of regulatory issues hounding development, in June 2019 a new acceptance criteria document was unanimously approved permitting automated construction. We could soon see metal concrete-extruding behemoths printing our future houses on our streets.