
How 3D Printing in Construction Will Change The World

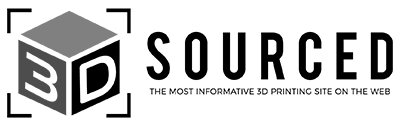
At 3DSourced we’ve covered everything 3D printing and 3D since 2017. Our team has interviewed the most innovative 3D printing experts, tested and reviewed more than 20 of the most popular 3D printers and 3D scanners to give our honest recommendations, and written more than 500 3D printing guides over the last 5 years.
The average bricklayer can lay around 300-500 bricks per day. At these speeds, traditional house builds can take anywhere from 4-12 months. This is fine, but compared to the burgeoning alternative we have that can print accurate houses within 24 hours, and with unmatched repeatability, it can’t compete. Welcome to construction 3D printing.
- We also have a ranking of the most exciting 3D printed house builds.
3D printing in construction is sometimes referred to as 3DCP, or LSAM (large scale additive manufacturing), using 3D printing to build all kinds of structures, like houses and bridges.
Rather than plastics on standard FDM 3D printers, these huge construction 3D printers print layers of concrete on massive robotic arms. They use FDM-style techniques, depositing concrete layers (no bricks) to create the entire frame of a house.
They can only build house walls and chassis structures however, leaving the house as a skeleton with rectangle holes to install windows, and plumbing and other systems need to be installed afterwards. However, for building house skeletons, construction 3D printing offers unmatched autonomy and speed.

How does the construction 3D printing process work?
3D model design
Before you build a house traditionally, you need to get planning permission, draw up plans, get them approved, and agree on the house’s layout.
With 3D printing, you’ll need a 3D CAD model, or STL file. This is all your construction 3D printer needs to print the entire house or other structure.
- We also have a ranking of the best architecture software.
Concrete 3D printer set up
Construction 3D printers print concrete and other mixes to build houses. These need to be mixed and prepped, and the huge house printers set up. Some can take an hour to set up, with huge robotic arms and wide frames to support their weight.
Construction printing
Once ready, the concrete 3D printer deposits material along the dimensions specified from the STL house file. Once one layer is finished, the printer rises up one layer, and repeats the process, creating taller and taller structures until the house is finished.
History of 3D printing in construction
Beginnings: theoretical
Though mainstream progression has been fairly new, construction 3D printing has been theorized and developed for around 25 years. Joseph Pegna’s 1997 paper — “Exploratory Investigation of Solid Freeform Construction” — is considered the first construction 3D printing technique.
“A thin layer of sand is deposited, followed by the deposition of a patterned layer of cement. Steam is then applied to the layer to obtain rapid curing.”
Pegna, 1997
Around the same time, Behrohk Khoshnevis of the University of Southern California’s Information Sciences Institute patented his ceramic extrusion technology in 1995. This technology developed into Contour Crafting, a technique using huge cranes to deposit large amounts of cement.
Originally planned as a way to make large molds, a series of natural disasters convinced Khoshnevis that his technology could effectively produce new houses in areas destroyed by earthquakes and other disasters.

Whereas Contour Crafting focuses on extrusion-based concrete 3D printing similar to FDM, D-Shape focuses instead on binder jetting-based housebuilding. The technology binds sand with a seawater and magnesium-based binder, creating stone-like structures. Invented by Enrico Dini and first patented in 2006, the company aim to 3D print entire buildings, having already printed the tallest 3D printed sculpture in 2009, the Radiolaria.
D-Shape’s construction 3D printer sits in a huge 6x6m aluminium frame, with 300 nozzles in the print head, each jetting cement. D-Shape’s binder jetting techniques are the major alternative to Contour Crafting’s extrusion-based house 3D printing proposals.
In 2008, experimentation and research on construction 3D printing and concrete 3D printing started at Loughborough University in the UK. Headed by Richard Buswell and his colleagues, the research moved from a gantry system to a robotic arm.
Whereas the gantry arm system previously used XYZ Cartesian coordinates to direct the print nozzle, the robotic arm offers additional degrees of freedom and accuracy. Additionally, some robotic arms can be programmed simultaneously with other construction 3D printing arms, speeding up the construction process. In 2014 the technology was licensed to Skanska, the world’s fifth largest construction company.
2013: Construction 3D printing becomes feasible
In 2013, NASA conducted a study testing Contour Crafting’s construction 3D printing technologies to build lunar structures. The study tested whether they could print with materials found on lunar surfaces, minimizing the need to fly materials from Earth and potentially saving billions of dollars. We have a full section on construction 3D printing in space further on in this article.
DUS Architects, a Dutch architecture firm, first released plans for a 3D printed building — the 3D Canal House — in 2013. The Amsterdam-based site was opened to the public on March 1st 2014.

In 2014, Winsun, a Chinese construction company, claimed to have 3D printed ten houses in one day. This is however a controversial area of construction 3D printing, with Contour Crafting founder Behrohk Khoshnevis claiming these efforts are faked, and that they have stolen his technology and infringed on his patents.
He and Dr Jing Zhang (founder of Sprintray), in an interview allege that Winsun CEO’s claims of being in the construction 3D printing industry over a decade are untrue, that Mr Ma, Winsun’s CEO, barely understood what 3D printing was when they met, and that they stole his technology, print elements of houses off-site, transport them to the locations, assemble them, and then claim to 3D print houses.
Winsun refute these claims, questioning the legitimacy of patent infringement claims when they have built structures while Contour Crafting have not. They claim nobody has seen their gargantuan construction 3D printer for privacy and intellectual property reasons, and that Dr Khoshnevis was prevented from ever viewing the technology when they were in previous discussions because of company laws.
Winsun have since 3D printed concrete bus shelters, are helping Elon Musk with the Hyperloop project, and claim to have sold more than 100 3D printed houses. From a paper detailing construction 3D printing’s history and development, Winsun appear to print off-site, saying: “[Winsun] print a mix with added waste material, off-site, in the factory, for transportation.”

The Army have also taken an interest in construction 3D printing. Tests have been carried out in 3D printing temporary barracks, bunkers, and fighting positions.
The first 3D printed bridge was completed in December 2016, in the Castilla-La Mancha Park in Alcobenda, Madrid, Spain. Constructed using Spanish conglomerate ACCIONA’s 3DBUILD technologies, the bridge spanned 12 meters, was 1.75 meters wide, and printed in micro-reinforced concrete.
Other recent exciting construction additive manufacturing projects include the printing of what is claimed to be the EU’s first 3D printed home, in Milan, Italy. The home, built out of a collaboration between Arup and CLS Architetti, was printed in 48 hours, comprising 35 modules. One of the major challenges for the project was developing a new type of fast-drying concrete that could dry before the next layer of concrete was 3D printed on top.
- More information on this build can be found in our ranking of the coolest 3D printed houses.
Arup used house 3D printer company CyBe Construction’s RC 3Dp printer. They are now further optimizing the process, developing recycled concrete mixes with natural fibers which are more sustainable, as well as bringing down costs and allowing materials to be sourced locally.
- We also have an article discussing the most innovative house 3D printer companies.
2017 onwards: Construction 3D printing goes viral
Russian 3D printer company Apis Cor shot to prominence by constructing an entire house in 24 hours back in 2017. The video went viral, exposing additive manufacturing houses to people who hadn’t even heard of 3D printing, and bringing Apis Cor to the forefront of 3D house printing. Apis Cor have since pitched to and collaborated with NASA, and broken the record for the world’s largest 3D printed house, a huge building in Dubai.

A year after Apis Cor’s victory, non-profit New Story and 3D housebuilding startup ICON collaborated to 3D print a house in Texas in March 2018. Compact and costing just a few thousand dollars, this proof of concept propelled ICON to $44m investment to bring their technology to fruition, and have since built a number of affordable 3D printed houses in Mexico.
Non-profit New Story focus on using building 3D printed homes for people in the developing area, building over 2,200 homes for 11,000 people across countries such as Mexico, El Salvador, and Haiti.

Further innovating, in August 2020 Belgian construction 3D printing company Kamp C printed the first ever multi-storey house, a 90-square meter, two-storey house all printed on-site in one part. Though this building took just under three weeks to construct, Kamp C believe that this can be brought down to two days.
“Our aim was to print the floor area, height, and shape of an average contemporary home, in the form of a model home with multipurpose options. This is a principle of circular building. The building can be used as a house, a meeting space, an office, or an exhibition space.”
Piet Wielemans, architect at Kamp C
How construction 3D printing can change the world
- Faster — entire house chassis can be built in under a day, leaving just the furnishings and electrical, plumbing and other systems to be finished.
- Cheaper — doesn’t require skilled labor, which also has uses where there may be labor shortages e.g. in developing world. Workers are still required to set up and monitor the printer however, so it doesn’t eliminate human labor. Only having to rent a construction 3D printer for a few days, rather than pay wages for months, significantly reduces costs.
- More precise and no human error — makes for more structurally sound builds, removing the possibility of a dangerous build due to a ‘cowboy builder’.
- Better for the environment — around 32% of all landfill comes from the construction industry, but additive manufacturing famously wastes almost nothing, making housebuilding much eco-friendlier. Moreover, companies are researching more environmentally friendly 3D printable concrete materials, such as more energy efficient, biodegradable, and better insulating concrete mixes.
- Creates homes for homeless & in developing world — ideal for those who have had their houses destroyed in natural disasters. 3D construction printing can also build on difficult geographies and curve round tight spaces. A good example is a home constructed in Nantes, France, which curved around a tree, making more efficient use of the space and making housebuilding more versatile. In the developing world where there may not be enough skilled builders to create houses, construction 3D printers can overcome this and create basic structures quickly.
- Safer — 400,000 US workers are seriously injured or worse every year. With construction 3D printing, risks are much reduced as workers are not physically building the structure.

Construction 3D printing in space
Construction 3D printing was first proposed for building permanent human settlements on Mars and the Moon back in 2013. As sending anything into space is so expensive, the ability to 3D print structures for astronauts to live in using locally sourced lunar materials would save billions — perhaps even trillions.
Therefore, Contour Crafting was tested back in 2013 with lunar-mimicking materials. If successful, NASA’s plan would be to use 90% locally sourced lunar materials to build settlements, with only the remaining 10% needing to be shipped over in rockets, such as the inflatable enclosed areas astronauts would live in.
D-Shape’s binder jetting construction 3D printers were also tested in a zero-gravity environment to ascertain whether the printer could create effective living structures with local lunar material.

NASA themselves hosted the NASA Centennial Challenge, completed in 2019, tasking people to build 3D printed habitats for future deep space exploration. The challenge awarded $2m to various projects across three stages.
One NASA-endorsed project, the aptly named architecture studio AI Space Factory’s Marsha Project design, was a tall yet thin four-astronaut house that can be made using local Martian materials, including basalt. Its thinness is more effective against the harsh Martain terrain, making it more appropriate for interplanetary habitats, and work is now being done to create a scaled down prototype.

The future of 3D printing in construction
Construction 3D printers are only getting more powerful, fast, reliable and versatile over time, with new advances changing the landscape every year. New innovations include COBOD’s new BOD2 second generation construction 3D printer, able to print 18 meters per minute, three times faster than the original BOD.
Swiss chemical multinational Sika claim to have mastered the required steps to 3D print concrete on industrial scales using their industrial robot arms. This is aided by Sika’s material developments, a range of mortar-mixed additives that dry within seconds — so additional layers can be printed on top with no ill effects.
According to Sika CTO Frank Höfflin, “digitisation is changing every aspect of construction and the entire life cycle of a building, from the design process and automated construction all the way to maintenance.”
However, though able to build house silhouettes quickly and effectively, the technology has not managed to achieve anything like a luxury villa, mansion, or hotel design. Currently relegated to basic huts, bungalows and basic house structures, we will see how construction and concrete 3D printing advances in the future, and whether it can solve the world’s growing housing crisis.