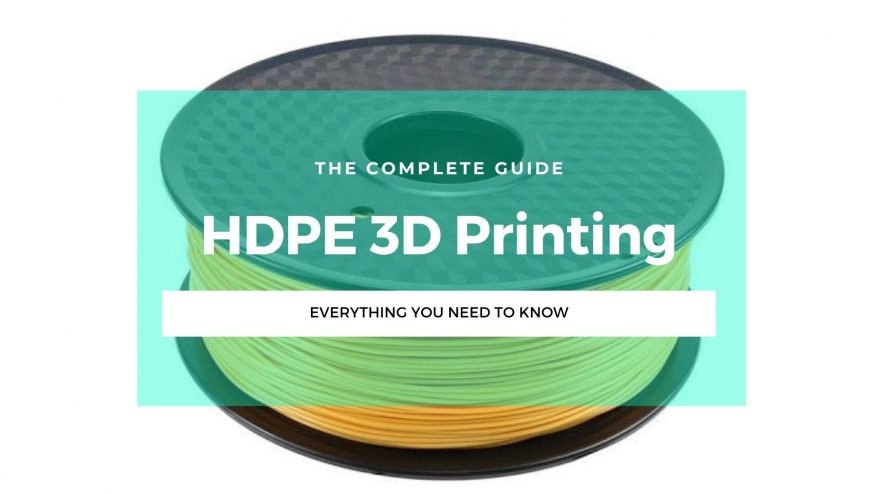
The Fall and Rise of HDPE 3D Printing Filament
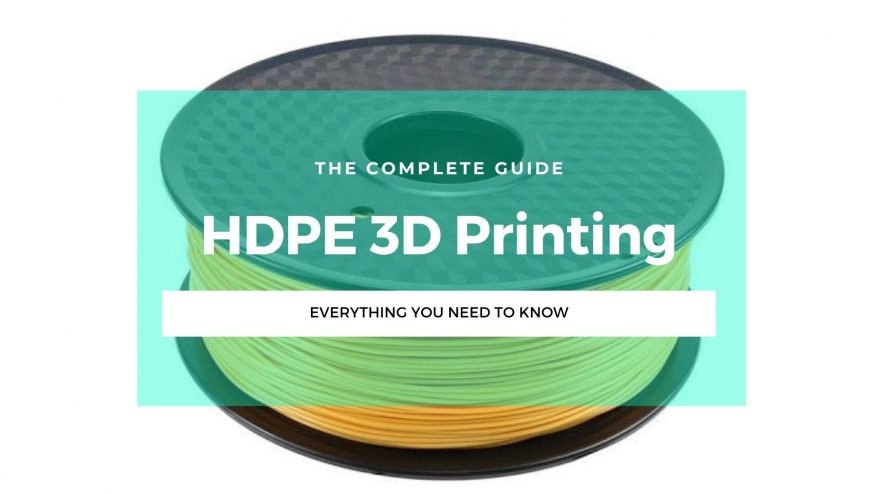
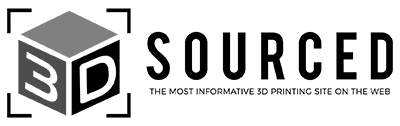
At 3DSourced we’ve covered everything 3D printing and 3D since 2017. Our team has interviewed the most innovative 3D printing experts, tested and reviewed more than 20 of the most popular 3D printers and 3D scanners to give our honest recommendations, and written more than 500 3D printing guides over the last 5 years.
High Density Polyethylene (HDPE) has had a remarkable fall from grace. Once considered the future of 3D printing and a frontrunner of polymer additive manufacturing, it has fallen by the wayside in recent years. But is there any way back for this ubiquitous pioneer?
The History of HDPE 3D Printing
Even if you are not familiar with the name HDPE, you have certainly encountered it. It is estimated that HDPE accounts for around 40% of the world’s total plastic production. And that is in no small part due its many useful properties.
Not only is it extremely cheap to mass produce, but it is a lot stiffer and sturdier than its sibling, Low Density Polyethylene (LDPE). It does not degrade or corrode, has a high melting point, is waterproof, food safe, recyclable, and most crucially, when it malfunctions it does not shatter and leave sharp edges, but instead bends or tears.
These factors make HDPE the ideal plastic for everyday domestic use. The plastic milk bottle you bought from the supermarket today? That was HDPE. The plastic bag you used to carry it to the car? HDPE. It is used to make outdoor furniture, heavy-duty trash bags, chemical-resistant piping and cladding, fireworks, fuel tanks, mannequins, and the list goes on.
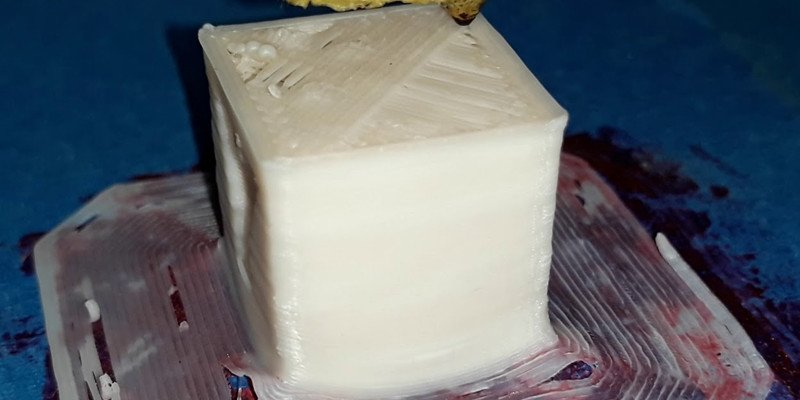
Seemingly, you cannot move for seeing HDPE somewhere, and the high turnover rate of certain HDPE products mean that there is always high demand for more. This is one of the reasons why it became such a focus of polymer 3D printing.
One of the most exciting elements to the democratization of 3D printing is the ability to make everyday goods yourself. With HDPE being such a fixture of our everyday lives, it was natural to experiment with 3D printing HDPE. It was expected that it would be a gateway material in driving low-cost 3D printing.
The Beginning of the End for HDPE
However, tragically, it soon began to fall out of favor with the 3D printing community. HDPE filament’s high melting point was a double-edged sword, as it required vast amounts of heat to print effectively. It also meant the parts shrunk after printing, a high potential for warping, and its lack of dependable bed adhesion.
Soon, other materials like Polylactic Acid (PLA) began to emerge, with near identical properties, but with much less demand on heating and aftercare, as well as being much easier to 3D print. HDPE became all but obsolete, and soon faded from the conscience of the community.
While HDPE is still a favorite with traditional plastic manufacturers, and still in wide use, 3D printing has all but given up on this former titan of the industry. And this strange disconnect has left many wondering whether there is a way to bring it back for one more round.
Getting the Best Results from HDPE 3D Printing
- Nozzle Temperature: 200°C-260°C
- Bed Temperature: 100°C-130°C
HDPE filament is compatible with most FDM 3D printers. Looking around online, there is wild speculation about the temperatures and settings to use. Some estimates for nozzle temperatures go as high as 260°C, while some claim to get good results at as low as 200°C. Like with most polymers, the advice is to start high and decrease the temperature over multiple tests until you find the sweet spot.
Having a heated bed is also a necessity to maximize bed adhesion, although again, advice varies. All of this uncertainty can leave you scratching your head. However, help is at hand.
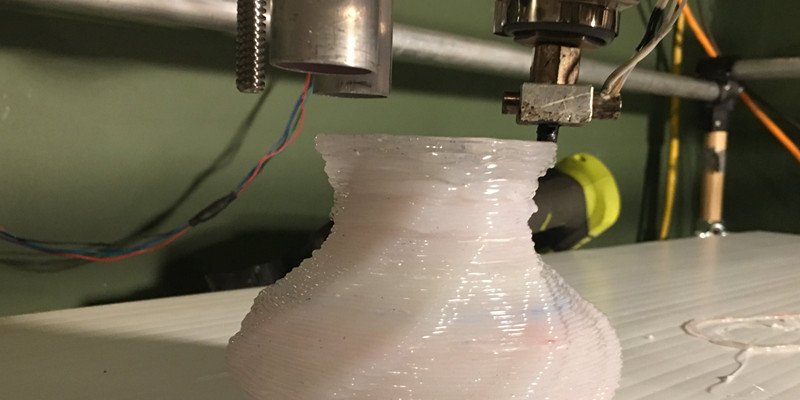
A study conducted by the University of Akron, Ohio, tested a number of different aspects of HDPE parts when printed at certain temperatures. They measured impact resistance, shape deformity and tensile strength of HDPE parts printed using Fused Filament Fabrication (FFF) methods, another term for FDM.
The parts were printed at higher extruder temperatures than would commonly be used in desktop 3D printers, but the results showed that 260°C yielded the best results for all of these metrics.
The parts printed at 260°C were stronger, were less brittle, and did not warp or shrink as much as parts printed at higher temperatures. And while it is possible to print HDPE at lower temperatures than this, it is almost always beneficial to start high and decrease temperature as you become more confident.
These high temperatures also mean that, for smaller parts, it is recommended to use a cooling fan as part of the aftercare for HDPE. This should help to reduce and warping or deformities as the part cools.
HDPE is also renowned for difficulties with bed adhesion. Along with warping issues, this is the biggest reasons why the material has fallen out of favor in the 3D printing community. Using tape on the build plate should help to provide the sticky surface necessary to get the parts to build properly.
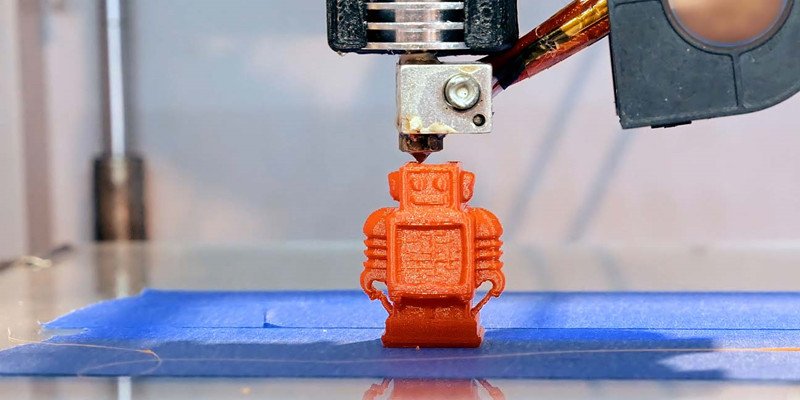
How Much Does 3D Printing HDPE Filament Cost?
As the demand for HDPE 3D printing filaments has plummeted over the years, nowadays, you can find listings online for under $30 per kilogram. This makes it one of the cheapest plastic filaments on the market.
The Advantages and Disadvantages of HDPE 3D Printing
Advantages of HDPE Filament
Cheap
When compared to similar 3D printable polymers, HDPE filaments are very cheap. This makes it very easily accessible for enthusiasts working on a tight budget.
Versatile
HDPE has a range of useful properties that make it extremely useful in everyday applications. Its strength, corrosion resistance and non-toxicity make it ideal for containing food both commercially and domestically. Being a stiff and shatter-resistant plastic with a high melting point also gives it multiple industrial applications in plumbing and construction.
Recyclable
One of the most sought-after qualities in modern plastics is the recyclability. With everyone becoming more environmentally conscious, HDPE could once again become a useful material in low-emissions, reusable manufacturing in the 3D printing industry.
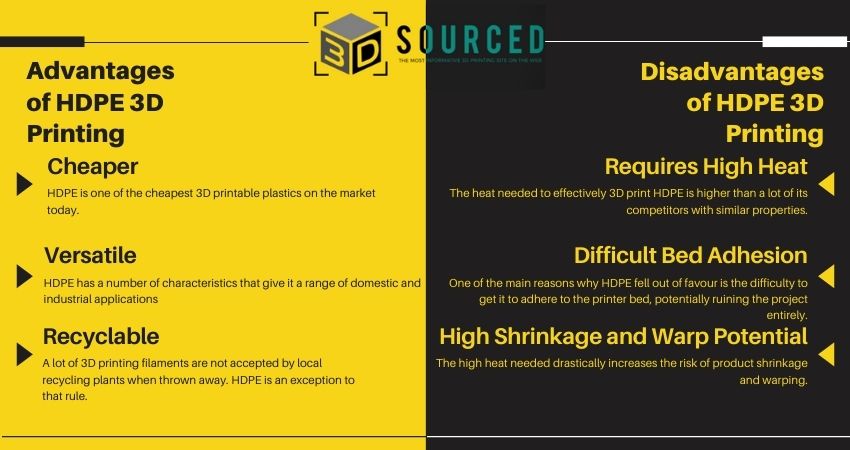
Disadvantages of HDPE 3D Printing
Requires High Heat
Conversely, HDPE’s high melting point also makes it very difficult to print, requiring very high heat to melt the filament. HDPE 3D printing filaments require a consistent nozzle temperature of up to 260°C, and bed temperature as high as 130°C, to get good results and avoid malfunctions.
Difficult Bed Adhesion
One of the biggest barriers to success when printing with HDPE is the bed adhesion difficulty. If the material does not stick to the base plate, there is no solid foundation on which to build the layers for your part, increasing the risk of deformities.
High Shrinkage and Warp Potential
HDPE died out as a mainstream filament in large part to its tendency to shrink and warp during the cooldown process. This has ruined many a project. As other polymers emerged like PLA emerged with much easier aftercare requirements, HDPE faded into obscurity.
Is There a Future for HDPE in 3D Printing?
The slow demise of HDPE as a mainstream 3D printing filament has been sad to see. But it does beg the question of whether it could once again experience a resurgence in the industry.
While it is likely that HDPE will never again become the aspirational focus of 3D printing as it continues to develop, it is very possible that it could once more carve out a distinct place in the market for one key reason.
Many of the 3D printable thermoplastics currently on the market like PLA, ABS, or Nylon, while being very popular, are not widely recyclable, and many local recycling sites around the world do not accept them. It is possible for individuals to recycle these materials themselves, but it is not as easy as it could be to recycle filaments. HDPE is a key exception to that rule.
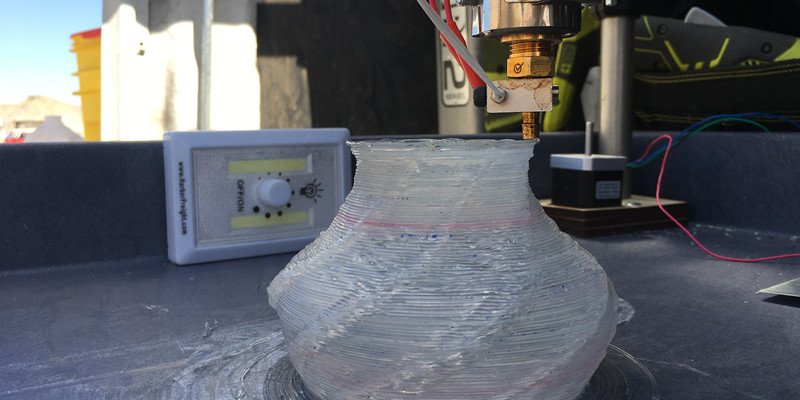
In fact, there are a number of services that specialize in recycling HDPE containers into filaments for resale. This is a major advantage in HDPE’s favour as the world’s attitude to plastic waste and environmental issues continues to evolve.
And with governments and private corporations committing got being more environmentally friendly, it is only a matter of time before the additive manufacturing industry begins to follow suit. Single-use plastics will begin to be phased out in favour of greener alternatives, and HDPE will surely see a resurgence with this trend.
While it possesses a number of drawbacks that put it at a disadvantage in comparison to other similar competitors, in just a few short years, expect to see a high density of demand for HDPE.