
4D Printing: Taking Manufacturing into a New Dimension

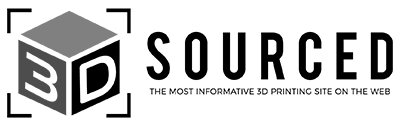
At 3DSourced we’ve covered everything 3D printing and 3D since 2017. Our team has interviewed the most innovative 3D printing experts, tested and reviewed more than 20 of the most popular 3D printers and 3D scanners to give our honest recommendations, and written more than 500 3D printing guides over the last 5 years.
As 3D printing technology continues to push the envelope with the kinds of objects that can be printed, it edges closer and closer to something more akin to a Star Trek Replicator, able to “print” essentially anything. Although that reality is still far off, a new technology, 4D printing, may allow us to entirely 3D print objects that have until now been impossible.
With furniture that can build itself, undulating pipes and transforming art installations all functional straight off the print bed, it’s worth looking at how 4D printing is bringing a new dimension to the industry.
When Was 4D Printing Invented?
An exact date for the technology’s invention is difficult to pinpoint, however the term “4D printing” became used widely after it was coined by Skylar Tibbits during a Ted Talk in 2013.
“So, remember I said 4D? So today for the first time, we’re unveiling a new project, which is a collaboration with Stratasys, and it’s called 4D printing. The idea behind 4D printing is that you take multi-material 3D printing, so you can deposit multiple materials, and you add a new capability, which is transformation. That right off the bed, the parts can transform from one shape to another shape directly on their own.”

What is 4D Printing?
Conventionally, a 3D print is complete and unchangeable once printed. It occupies space as height, length, and width, hence its three dimensions. A 4D print also occupies space three-dimensionally, but unlike 3D printing it can also change its shape, color, or other properties over time after being printed. This ability to change form allows 4D prints to not only occupy three-dimensional space, but also the additional dimension of time.
To explain: adding time to an object that cannot change form does nothing. For example, 3D printing a miniature character and leaving it alone overnight will result in exactly the same character the next day, because the PLA filament or other filament will not change overnight. However, leaving a soft clay 3D printed sculpture alone overnight will result in a hard clay sculpture by morning, because clay can change its properties over time, and therefore just like a 4D print, occupies time.
Currently, there are no commercially available 4D printers. However, that didn’t stop Skylar Tibbits from using buzzwords like “robotics-like behavior,” “material logic,” and “adaptive products” to describe the technology.
Which begs the question, has the concept of shapeshifting materials just caught the imagination of its researchers? Or does 4D printing truly have the potential to change the applications of 3D printing across all industries? What could the world look like if Skylar Tibbit’s vision came true?

4D Printing Tomorrow: How The Future Could Look
You wake up and enter your bathroom. You flick on the lights, but nothing happens because your apartment’s power is out. Not to worry, the sink still rises so you can use it without stooping over.
Water still flows from your taps, the piping beneath undulating to pump the water themselves. As you wash your face, your windows open themselves up to let out the steam.
You go into your medicine cabinet and take your prescription, the small capsule you swallow waiting patiently in your body until it needs to release its drug payload.
After, you head downstairs and begin making yourself coffee. You take a thumbnail-sized, almost perfectly flat coffee cup and begin to slowly pour it in, all the while the cup expands to a regular size. Once you finish your drink, you again crush it down small, and put it away in your tiny cupboard.
These are all possible with objects that are reactive to certain conditions, changing quickly over time. We’ll have to wait and see whether this vision of the future will eventually become reality. In the meantime, we can explore what 4D printing is capable of today.
4D Printing Today
Currently, researchers have created objects that can change shape with exposure to temperature, water, humidity, gravity, and even light kinetic force. Most importantly, they can all change form without any electronic or mechanical devices. They are effectively just standard 3D prints with shape-changing properties.
The implication is that as the technology improves, a single 3D print could soon replace objects that up until now would have been impossible to produce without multiple mechanical or electrical parts. Why build and assemble door hinges when you can do both with a single 4D print?
Within 4D printing, two main techniques currently lead the field: printing with water-reactive materials, and with heat-reactive materials.
4D Printing Part 1: The Hydro-Reactive Approach
The aforementioned Skylar Tibbets, founder, and director of the Massachusetts Institute of Technology’s (MIT) Self-Assembly lab, has conducted research and created multiple projects on what they call “Programmable Materials.”

So far, MIT Self-Assembly labs are best known for their series of water-reacting objects. These 3D prints use various composite polymers containing both hydrophilic and inert elements. Hydrophilic materials are strongly attracted to water and are highly absorbent, whilst the inert elements have no reaction with water. When submerged in water, the hydrophilic elements swell as they absorb the water, while the inert elements remain rigid.
The resulting object changes shape, with the swelling elements distorting the object into its final form.
The Vision
Skylar Tibbits and MIT’s vision for programmable materials means progressing 4D printing technology until it can achieve the same feats as robotics! Speaking about their designs, they explained that they intended for them to be “As cost-effective as traditional materials, easily fabricated and capable of flat-pack shipping and self-assembly…offer unprecedented capabilities including programmable actuation, sensing and self-transformation from a simple material. Our goal is true material robotics, or robots without robots.”
Their 4D printed objects include a flat and unfurled cube that transforms itself into a box, a long string that becomes the letters “MIT,” and a hex grid that becomes a ball (technically an octahedron).

The applications for a technology that allows objects to build and maintain themselves, rather than rely on complex machinery or human interaction, would undoubtedly have sweeping implications across a range of industries.
In the same Ted Talk where Skylar introduced the term 4D printing, he also presented a specific medium-term application for the technology:
“Let’s go back to infrastructure. In infrastructure, we’re working with a company out of Boston called Geosyntec. And we’re developing a new paradigm for piping. Imagine if water pipes could expand or contract to change capacity or change flow rate, or maybe even undulate like peristalsis [the muscular contractions that allow you to swallow food upside down] to move the water themselves. So, this isn’t expensive pumps or valves. This is a completely programmable and adaptive pipe on its own.”
The implications for this specific case would be pipes that never need to be maintained. Once laid, they’ll be able to expand and contract to deal with changing populations, city-planning, and fluctuating usage. In theory, your drive home would never be disrupted by pipe-related roadworks again.

Despite its ambitious aims, there are several practical reasons why hydro-reactive 4D printing technology still hasn’t progressed much further than boxes that can fold themselves.
Disadvantages of 4D Printing: Time
MIT has released several videos demonstrating how their prints transform. Despite these videos lasting less than a minute, the footage had to be sped up from 50x, to sometimes 150x real time.
Considering a hand-sized cube takes up to two hours to self-assemble or transform, imagine how long a far larger object would take. For example, at current transformation speeds, a hydro-reactive sofa-bed would take up to a full day submerged in water to convert.
Despite the appeal of single-piece objects, 4D printing will struggle to seriously compete until their transformation time rivals conventional objects.
4D printing disadvantages: Water-Loss and form-holding
Although the concept of objects that can build themselves by adding water is an incredible thought, this also means the same polymers can lose water through evaporation and heat – losing their new characteristics.
Despite the complexity of conventional engineering, there is no risk of your IKEA furniture slowly dismantling on a hot day, or your car falling apart when it’s not parked in the shade. A workaround could be creating objects that have to be regularly “watered” in a similar way to plants to preserve their current shape, though this would undermine MIT’s vision of creating objects that need only limited or no human interaction to build and maintain.
However, technology already exists to create improved hydrophilic materials that do not dry out. In 2016, an unrelated MIT mechanical engineering team lead by Xuanhe Zhao created a hydrophilic material resistant to water. They achieved this by binding hydrogel with layers of elastomers, preventing water from being able to evaporate from the hydrogel.
Arguably however, if a hydrophilic 4D print was prevented from being able to lose water, it would also be prevented from being able to transform. Without the ability to change over time, it would arguably no longer be a 4D print, but rather a hydrophilic 3D print.
Until the technology allows for sustainable transformations outside of water, it will struggle to compete with its conventional competition.
The alternative to water-reactive 4D prints are thermo-reactive 4D printing techniques, which seemingly offers solutions to both the time and form issues.
4D Printing Part 2: The Thermo-Reactive Approach
Another technique being explored is that of using Shape Memory Polymers (SMPs). Rather than swelling with water like MIT’s hydrophilic polymers, SMPs instead store a “memory” of their original shape, and if deformed can transform back to it once heated.
A notable research project in this field was led by Assistant Professor Qi Ge in 2016. Using SMPs, he was able to print high-definition objects with a predefined “original” shape. Two of the most notable prints resulting from this research was a model Eiffel tower, and grippers.
The Eiffel Tower model very clearly demonstrates the technology’s concept at work, with his research and published videos showing the model’s spire bent at 90 degrees, only to completely straighten once heated.
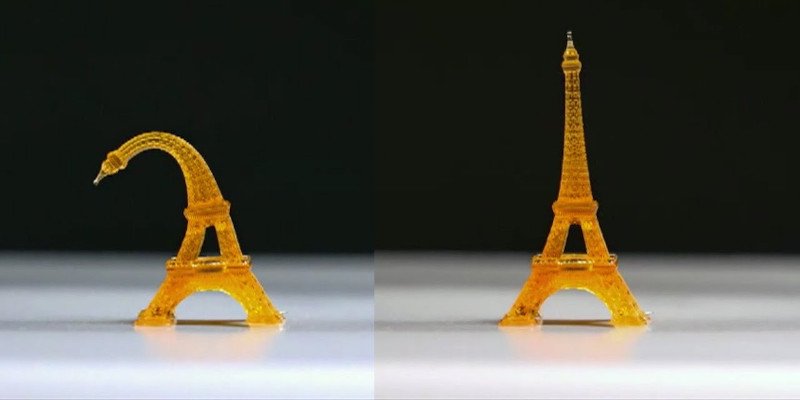
The grippers meanwhile resembled a tiny, clawed hand, and as the name suggests can grip other objects. In its demonstration video it begins in a “deformed” position with its fingers open and splayed out, before being placed onto a screw and heated. This causes its fingers to transform to their “original” closed position and grip the screw, allowing both to be picked up.
Better than Water?
Thermo-reactive SMPs offer solutions to the hydrophilic material’s challenges of time and permanence. While MIT’s folding objects take potentially hours to transform, both the Eiffel Tower and grippers transformed in just seconds, making them far more practical for everyday life.
Additionally, without the issue of water loss, these SMP objects will hold their new shapes permanently – unless deformed by further human input or heat – whereas water-reactive 4D prints risk transforming if they dry out.
Heat 4D printing applications
SMPs crossover with hydrophilic polymers in terms of their wide range of suggested future applications, however SMPs offer applications specific to their heat reaction. They can produce art installations that transform throughout the day with the sun’s heat, drugs that activate according to body temperature, and 3D printed clothing that responds to emotion or skin temperature.
However, despite its potential advances over hydrophilic polymers, it too has its own challenges to overcome.
4D Printing with Heat Disadvantages: Too Hot to Handle
Currently, the high heats required to reliably transform these polymers can create problems. Specifically, Qi Ge’s research used temperatures between 122-158⁰F to transform his Eiffel Tower and grippers. The convenient way for end-users to achieve this temperature would be with a moderately powerful heat-gun. Although this is far faster than waiting for prints to absorb water, having such high reaction temperatures limit its uses in everyday life.

For example, 4D printing can’t be used in transforming clothing or furniture without the risk of injuring the user. It also can’t be used in medicine as the prints will either be too hot to safely enter the body, or won’t react within the human body’s relatively cool 98⁰F operating temperature.
This can be worked around, such as by heating up your 4D printed sofa to convert it into a bed, then waiting around for it to cool down before you can use it. However, until the technology advances to operate at cooler temperatures, it can’t compete with the convenience of a conventional mechanically operated sofa-bed.
Conclusion: All in good time
4D printing is still very much in its infancy, having yet to progress from research and development stages. However, despite its current limitations, 4D printing has still managed to make shapeshifting single-piece 3D printing a reality.
I opened this article by questioning whether this technology had simply caught the imagination of its researchers? Well, when said technology also has the future potential to intelligently shape-shift, then perhaps a better question could have been, how could it not?