
The Versatile World of Silicone 3D Printing

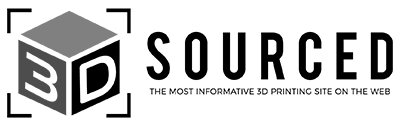
At 3DSourced we’ve covered everything 3D printing and 3D since 2017. Our team has interviewed the most innovative 3D printing experts, tested and reviewed more than 20 of the most popular 3D printers and 3D scanners to give our honest recommendations, and written more than 500 3D printing guides over the last 5 years.
If you’re looking for a durable, flexible, sustainable 3D printed material wide a wide variety of applications, look no further than silicone. Silicone 3D printing has attracted a lot of attention for its versatility, and is one of the most exciting plastics in the industry.
As a relatively new player in 3D printing, it is not yet close to becoming mainstream, but early signs indicate that it has a huge potential to positively affect our lives.
Part 1: How does Silicone 3D Printing Work?
What is Silicone?
First discovered in 1854, silicone is a polymer comprising silicon, carbon, hydrogen and oxygen. As a synthetic substance, silicone comes in a rubber-like form that is flexible and elastic.
Silicone is produced through a complex process. Silicon powder is heated with methyl chloride to form methyl chlorosilane. This is then distilled to collect dimethylchlorosilane. Water is added to catalyze the hydrochloric acid within; the resulting chemical can be polymerized in a number of ways to form whichever silicone form is required.
Despite silicone’s complexity, silicone can be mass produced, and relatively cheaply. Among the most popular forms of silicone is silicone rubber, an elastomer used in silicone 3D printing.
Both in the 3D printing industry and the wider world, silicone rubber has a variety of useful properties and applications. It is extremely insulating, with low thermal and electrical conductivity, low chemical reactiveness, and is watertight.
Silicone rubber can survive in both hot and cold conditions, as low as -100°C and as high as 300°C. Furthermore, it does not stick, but adheres well, making it easily moldable. These factors make silicone a very promising 3D printable material.

Silicone Additive Manufacturing
Traditionally, silicone is injection molded, where liquid silicone is pressurized into a mold and cooled, forming the final solid product. However, though cheap to produce, set up costs are high. Silicone molds are astronomically expensive, some as much as $100,000 each.
Traditional silicone production was unsuitable for small production runs, requiring a different approach. A major barrier to silicone 3D printing is its high resistance, so typical FDM 3D printing is not possible.
However, German chemical researcher Wacker has developed ACEO, a technology that allows silicone to be 3D printed without the need for thermal regulation.
ACEO works similarly to 3D inkjet printing. A filament is heated into a liquid, deposited on to the baseplate by a nozzle, and treated under UV light to solidify. This process then repeats, layer by layer, to create the final silicone 3D print. However, ACEO uses silicone resin, a low-viscosity liquid-like substance that remains as such until treated by the printer. This prevents the need for high levels of heating that would be ineffective.
ACEO’s precision is admirable, capable of printing structures as slim as 0.6mm in width. In March 2019, ACEO opened their first Open Print Lab in Ann Arbor, Michigan.
Other companies like German RepRap, Carbon 3D and EnvisionTec have also developed silicone 3D printing techniques and are making waves within the industry. Carbon 3D now offer a silicone urethane material for their range of resin 3D printers. And while the technology is still developing, early signs look promising for a range of industries.
Part 2: Silicone 3D Printing Applications
Robotics
One similarly futuristic industry increasingly relying on silicone is robotics. Engineers are constantly looking for ways to improve movement, durability and authenticity in their models, and silicone is perfect for this.
Silicone offers key advantages in customizing parts to meet specific needs, and can be printed accurately and on-demand. This means development is quickened and perfected through rapid prototyping.
Silicone 3D printing is becoming useful in the production of lifelike androids. This is because silicone’s elasticity and flexibility make it ideal for synthetically replicating muscle and skin. The technology allows developers to print structures to their preferred specifications and make producing their designs easier.

Silicone 3D printing also has uses in soft robotics. With programmable or manually controlled robots that do not have any hard metal structures, personalized 3D printed silicone devices are finding usage in the physiotherapy industry. They are able to aid the rehabilitation of limbs following trauma or degenerative conditions, and research is being conducted to perfect this process.
This technology gives silicone 3D printing other applications in a range of industries like construction, burrowing into the ground to locate underground pipes or wires, animal conservation in tracking and tracing endangered species, or even in the military with bomb disposal or reconnaissance.
Medicine
Silicone 3D printing also has a variety of medical uses. Firstly, its low toxicity makes it ideal for producing implantable devices. Silicone gel is notoriously used cosmetic implants, but also for muscle implants and contact lenses.
Similarly, silicone is gas permeable, allowing for oxygen to freely pass through without obstruction, crucial for implants as blocking oxygen flow in the body leads to tissue death and necrosis. Silicone is a vital material in preventing fatal bodily damage, and one of the few materials suitable for these procedures.
Silicone also does not support microbiological growth; this means that it self-sterilizes and prevents bacteria developing. This makes potential silicone 3D printed medical devices useful, such as catheters, feeding tubes, and drains.
The bacterial sterilization is also why silicone gel is applied in Scar Treatment Silicone Sheets. The sheets are placed over scar tissue to help relieve itching and discomfort, while also helping to flatten the scar.
With 3D printing, doctors can print medical implants and devices on site and customize them to the patient’s needs. This removes the generalized approach of mass production and printing in-house saves time and money.

Part 3: The Advantages and Disadvantages of 3D Printing Silicone
Silicone 3D printing: Benefits
Cheaper
Traditional injection molding molds can cost an eye-watering $100,000 without even factoring in material and equipment cost.
Not only does 3D printing allow for small-batch or individual prints, but also a variety of different designs, eliminating the need to buy molds and allowing manufacturers to print on-demand.
This also makes technology far more accessible to individuals and smaller manufacturers who previously couldn’t afford expensive silicone molds.
High Flexibility and Elasticity
Silicone’s ability to be bend and stretch without breaking or deforming gives it a distinct advantage over other 3D printable plastics like ABS or PLA.
While TPU and other more elastic 3D printable materials exist, silicone tends to be more durable, especially in everyday situations, like garden hoses. Combining both durability and elasticity makes silicone stand out.
Extremely Insulating
As a watertight plastic, silicone is highly resistant against water, temperature, oxidization, chemical reaction and electricity. For this reason, it has found use in industries where stability under stress is vital.
In construction, silicone is used as a sealant in gaps, joints and crevices in buildings, as well as a moisture resistant barrier around window fittings. It is also used widely in North American homes to act as a firestop between rooms, preventing the spread of smoke or flames from one room to another in the result of house fires, showing its life-saving potential.
3D printing silicone does not diminish this quality, while allowing components to be microscopically tailored in thickness and shape based on the project so it fits perfectly. This improves safety and makes fitting the parts easier, reducing the risk of error.

Limitations of Silicone 3D Printing
Needs Specialized Equipment
Even though silicone 3D printing uses a technique similar to typical inkjet printing, the use of resin requires specialized silicone 3D printers. Regular inkjet printers use heat to melt filament for deposition, which is not possible for silicone.
ACEO’s printer design is able to correct this, but the printer itself is patented and not available commercially. That means that if you want a 3D printed silicone product, your only way to get it is to buy it through a 3D printing service. ACEO offers its services to professionals and businesses, and it can be done entirely online.
Materials Not on the Market
Likewise, the silicone resin used as a building material is also not available for purchase. Silicone 3D printing is still very much in its infancy stages as an industry. The resin is not on sale yet, and silicone filaments do not exist yet. As resin 3D printers and FDM 3D printers are two of the most common types of 3D printer, this is a major barrier to adoption.
ACEO’s success expands the potential for 3D printing silicone, but is currently only available through their 3D printing service.
Not Yet Scalable
Even if you were to find a service at a reasonable price, printing large volumes of products is far from becoming a reality.
ACEO’s silicone 3D printer, along with others in the field, have very small build volumes. On top of that, print speeds are low, limiting production capabilities. Silicone 3D printing in its current state is not going to change the world, but with the right amount of patience and belief, it may do soon.
Conclusion: Where Does Silicone 3D Printing Go from Here?
Silicone 3D printing has not yet extended to making the technology available for purchase. Instead, companies who have silicone 3D printers sell their services as 3rd party manufacturers, and aside from ACEO, there are several major organizations pushing the industry forward.
In February 2020, German injection molding firm Arburg purchased German RepRap, a 3D printing company that uses a technique they have dubbed Liquid Additive Manufacturing (LAM). In practice the technique is similar to ACEO’s, but they are able to print using slightly higher-viscosity silicone, making stronger, more durable parts.

German RepRap have been actively manufacturing since 2018 and include Airbus Helicopters and SIKA Automotive, who themselves supply sealing and reinforcing solutions for some of the biggest car brands in the world such as Audi, Ford, and Tesla.
Another company emerging as an industry leader in silicone 3D printing is Carbon 3D. They have developed a new technique called Digital Light Synthesis (DLS) whereby cured layers of silicone are detached from the printer’s vat and deposited. This increases the speed of construction, potentially expanding silicone 3D printing to industrial levels.
With such high-profile progress being made, perhaps within the next few years silicone 3D printing will become commercially available for the private market, where anyone would be able to buy both the technology and the materials to print products for themselves without the need for 3rd parties.
When that becomes reality, it will no doubt benefit the medical industry particularly, with hospitals able to print an array of medical devices on-site which would bring down costs and improve the efficiency of patient care.
With silicone making a big splash in a very short period of time in the plastic 3D printing industry, it is clear that this versatile material will seal its place in the mainstream before long.