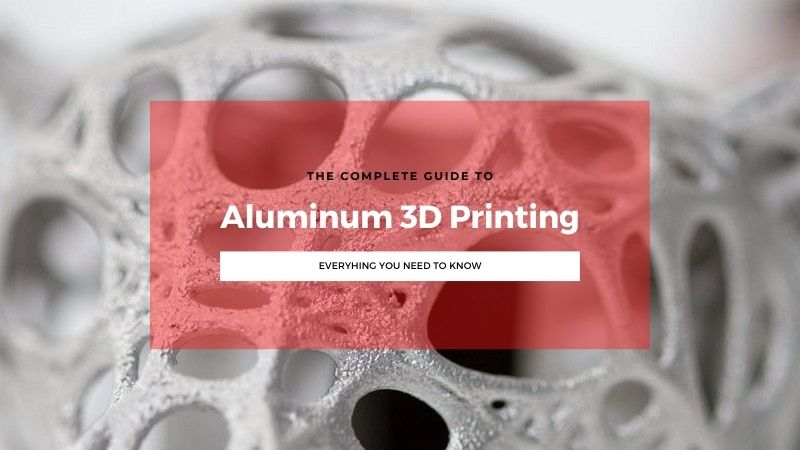
The Complete Aluminum 3D Printing Guide
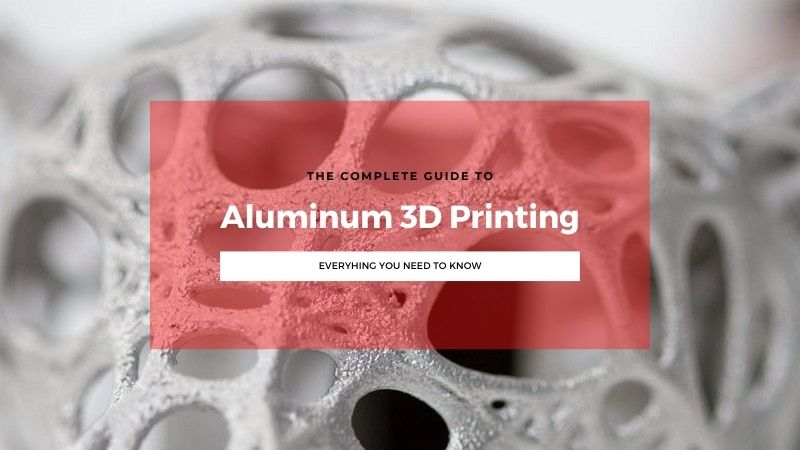
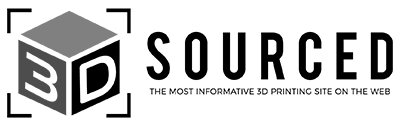
At 3DSourced we’ve covered everything 3D printing and 3D since 2017. Our team has interviewed the most innovative 3D printing experts, tested and reviewed more than 20 of the most popular 3D printers and 3D scanners to give our honest recommendations, and written more than 500 3D printing guides over the last 5 years.
One of the most widely used metals in society, aluminum 3D printing is expanding the uses of this historically jack-of-all-trades metal. As metal 3D printing continues to develop with new techniques and applications, aluminum 3D printing’s accessibility makes it key to the future of metal additive manufacturing.
- We also have a guide to the best metal 3D printers.
After iron and silicon, aluminum – or aluminium in the UK – is the planet’s third most common element, and its usage can be traced as far back as Ancient Greece. Alum, a compound of pure aluminum and salt, had many uses such as water purification, dyeing, tanning and cosmetics.
Aluminum has a diverse variety of properties. Pure aluminum is a very weak substance with a low 660C melting point, used instead in industry in alloys. The most common 3D printing aluminum alloy is AlSiMg0.6, combining aluminum with silicon and magnesium.
Aluminum is, however, a very ductile and electrically conductive element, giving it distinct advantage in electronics. It also has a high resistance to chemical and environmental corrosion, allowing aluminum to withstand an array of harsh conditions. It is these properties that have caught the eye of 3D printer manufacturers.
The Aluminum 3D Printing Process
Aluminum first rose to prominence in the metal 3D printing industry in 2006, when MCP HEK, a German chemical researcher and tool technology company, became the first to process aluminum and titanium through Selective Laser Melting (SLM). From there the process has evolved, and is now commonly used in both aluminum and metal 3D printing in Direct Metal Laser Sintering (DMLS).
DMLS involves a roller coating a baseplate in powdered metal, with a high-powered laser melting it together into layers formed in 3D CAD software. The plate is then lowered and recoated for the next layer to be formed.
3D printing aluminum has shown marked benefits compared with traditional methods of aluminum production, such as CNC milling, or melting and molding. CNC milling uses metal ingots or blocks, and cuts them into the desired shape, whereas melting and molding involves pouring a melted metal into a mold, and cooling it.

3D printing not only produces much less waste metal than these methods, but the use of targeted lasers reduces the amount of energy used, making the process more efficient and saving money. As the 3D printing technology develops, these advantages will only become more apparent.
If you are interested in buying a 3D printer to print aluminum, we may be able to help:
*One of our trusted partners will be in touch following a quote request.
3D Printed Aluminum Applications
Mechanical Components
Many internal components of machines like CNC mills, belt sanders and pillar drills are made from aluminum. Aluminum’s light weight does not restrict the movement of these parts, including cogs, brackets, screws and pulleys, improving efficiency.
As these parts don’t need to be strong, only durable and electrically conductive, aluminum is a cheaper and more appropriate solution than steel or titanium. This is of notable benefit to manufacturers who buy these tools, as using aluminum will reduce the price.
As a form of additive manufacturing, 3D printing aluminum uses only the required metal powder to build the final part. On the other hand, traditional manufacturing methods, especially CNC milling, are subtractive manufacturing methods which generate large amounts of waste. Though recyclable, this wasted aluminum adds to costs. Using aluminum additive manufacturing drastically cuts down on waste and saves money.

Bikes and Drone Accessories
Commercial cycling is expensive, using costly carbon fiber frames, chains, handlebars, and pedals. While cheaper than materials like titanium, current costs are still a strong deterrent. This has made it a less accessible hobby, with prices soaring to hundreds or even thousands of dollars, not to mention the plethora of accessories.
Aluminum 3D printing offers a cost-effective alternative for bike and drone accessories. While not as robust as carbon fiber, aluminum is a similar weight. A sheet of aluminum one-meter square, 6mm thick, is approximately 16.2kg, not significantly more than the 9.3kg of carbon fiber.
- We also have a guide to 3D printing carbon fiber filaments.

An aluminum 3D printed bike could also be designed to their specifications, improving ride quality as well as safety from easier control.
Also, in the hobbyist sector aluminum is often used to build drone body panels and rotor guards. While lacking a high impact resistance, aluminum’s extremely light weight allows for greater efficiency while still protecting from minor collisions. If costs come down in future, aluminum 3D printed drone parts could improve drone efficiency.
Construction Tools and Fixtures
With aluminum being a light, low cost, and scratch-resistant material, it has found many uses across the construction sector. While pure aluminum is not suitable for this sector, alloys like AlSi10Mg are widely popular.
As a construction material, aluminum is used in almost every area of a building’s composition. Due to its corrosion-resistance, aluminum is a popular material for a building’s external parts. It is also used in roofs, walls, windows, doors, and railings.
Its reflective properties help to boost the energy efficiency of the building by retaining heat and light, it can be anodized to meet a wide variety of aesthetic needs, and it is very eco-friendly with no maintenance costs.
Aluminum 3D printing has already shown promise in this sector. A Science Direct report from 2018 concluded that 3D printing in construction has the potential to revolutionize the industry, with benefits in greater structural efficiency, waste reduction and material consumption, streamlining the design process, greater architectural freedom, enhanced customization, and improved on-site safety.
Aluminum 3D printing is already beginning to catch the eye of the construction industry, and could lead to widespread adoption of 3D printed houses.
- Read our feature on the 8 Most Exciting 3D Printed House Builds of 2020

The Pros and Cons of 3D Printing Aluminum
3D printing aluminum advantages
Lightweight
Aluminum is one of the lightest natural solid metals, weighing only 2.7g/cm3 – just a third of steel. This gives aluminum uses in many everyday areas where heavier metals would be impractical, such as metal packaging, electrical components, and kitchen appliances.
Aluminum is only practically useful in alloys. These aluminium alloys however are lightweight, making them useful for these everyday applications where harder metals are not required.
Ductile and Electrically Conductive
In wire form, aluminum is highly ductile, meaning it can be bent and twisted without snapping. 3D printing can construct components smaller than a millimeter across, so smaller items have a lower risk of breaking.
What’s more, aluminum is an excellent conductor, making it an ideal choice in the production of components in electrical goods. This makes 3D printed aluminum parts ideal for electronics.
Corrosion-Resistant
Unlike other lightweight, conductive metals like copper, aluminum is not degraded easily by oxygen or rainwaters’ acidic effects. This makes aluminum useful in the construction and transportation sectors, where resistance to the elements is key.
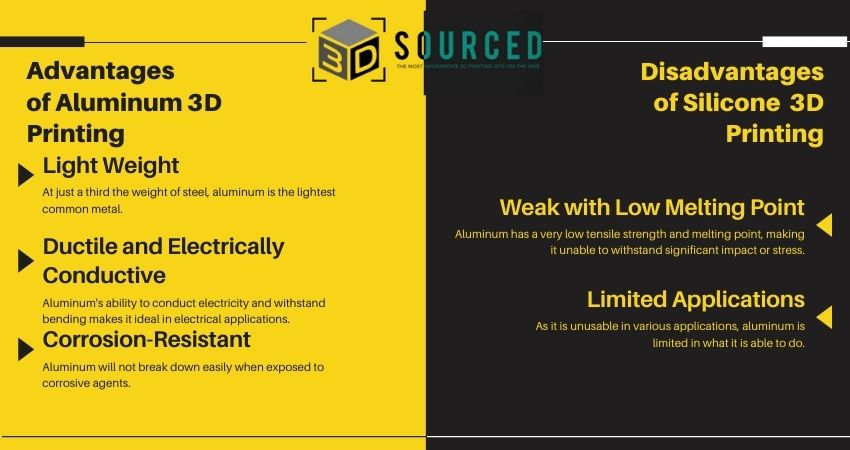
3D printing aluminum disadvantages
Weak and Low Melting Point
While metals like titanium can boast being both lightweight and strong, Aluminum has low tensile strength. Almost 40 times weaker than steel, pure aluminum simply cannot compete with other metals. Stronger aluminum alloys are therefore preferred.
Additionally, aluminum’s 660°C melting point is 300C lower than silver, 700°C lower than stainless steel, and more than 1000°C lower than titanium. In fact, it has the lowest melting point of all common metals.
- We also have a guide to 3D printing titanium.
Therefore, aluminum parts are much less capable of functioning in high-temperature scenarios such as in the functioning of energy plants, or as 3D printed car parts that come into close contact with hot engine systems.
Limited Applications
This lack of strength and heat resistance limit aluminum’s 3D printing applications. Aluminum is an unwise choice in high-stress and high-temperature industries, a factor that does not hamper other choices that are available.
Its advantages are far from unique. Its low weight, corrosion-resistance, malleability, ductility and electrical conduction are all present in other materials. What it does have in its favor, however, is its relatively low cost.
Conclusion: What’s Next for the 3D Printed Aluminum Industry?
Aluminum’s saving grace is that it is one of the cheapest 3D printable metals. Currently, powdered DMLS-suitable aluminum, namely the AlSi10Mg alloy, costs around $80 to $120 per kilogram.
With the price being a fraction of other metal powders, aluminum is one of the most accessible on the market, making it a leading material in further 3D printing research. The powdered aluminum industry is expected to reach $3.43 billion by 2025.
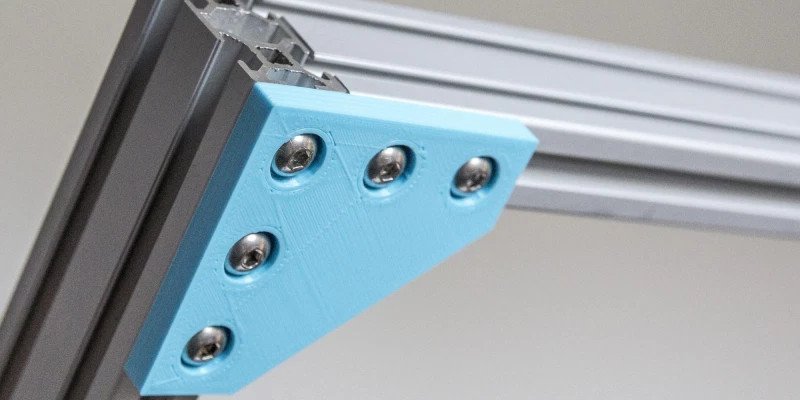
And progress is continuously being made. In November 2020, scientists from the National University of Science and Technology (NUST) in Russia developed a nanocarbon powder, derived from waste oil, for aluminum alloys. The new material is 1.5 times harder and has a significantly lower porosity, greatly improving aluminum part usability in air and space travel.
Beyond this, the low cost of aluminum powder will also come to benefit consumers in the near future. Experts suggest that at-home 3D printing could become a mainstream reality within the next 10 to 20 years, and with that, much focus has been placed on what will be printable.
Aluminum will surely be among the first metals to become a part of this reality, as its numerous applications in kitchen and homeware, combined with its affordability and low melting point, will facilitate the evolution of the industry in this direction.
With the future looking bright for 3D printed aluminum, we will certainly see more ‘cans’ than ‘cannots.’