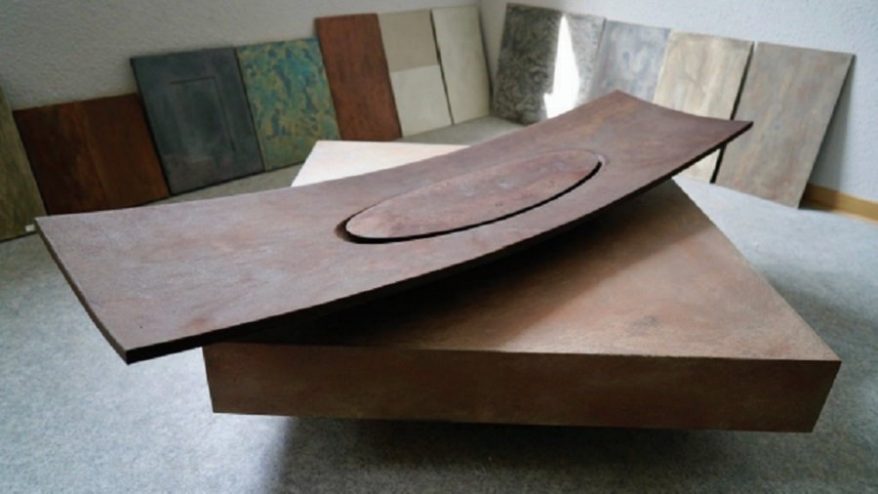
3 Ways To 3D Print Your Own Furniture!
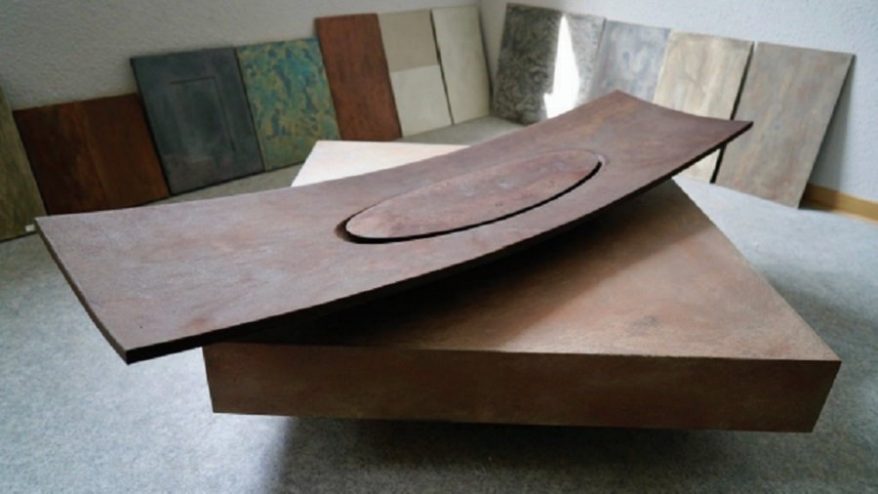
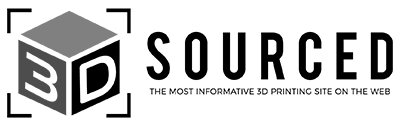
At 3DSourced we’ve covered everything 3D printing and 3D since 2017. Our team has interviewed the most innovative 3D printing experts, tested and reviewed more than 20 of the most popular 3D printers and 3D scanners to give our honest recommendations, and written more than 500 3D printing guides over the last 5 years.
Have you ever wanted to produce your own 3D printed furniture, but then dismissed the idea as impractical? After all, such projects are often expensive, slow, and require large industrial 3D printers to produce. Or at least they did, until now.
Recent innovations have made 3D printing furniture more accessible than ever. Whether you want a dramatic centerpiece for your palace’s dining room, or just a custom kitchen sink, one of these three techniques will work for you.
Using a large 3D printer, multiple prints on a desktop 3D printer, or the relatively new technique of “Hangprinting” represent the most viable ways of 3D printing furniture. In this article we will explore these options, the opportunities and challenges they present, and the most interesting projects that have used them.
If you’re interested in learning to design furniture, have also written an article on the best free furniture design software.
Option 1: Producing furniture with the Hangprinter
Designed by Torbjørn Ludvigsen, the Hangprinter is intended to make printing large objects as cheap as possible. Rather than being housed in a case, The Hangprinter mounts on your room’s ceiling, rather than standard Cartesian or delta 3D printers which print within their enclosure. This makes your maximum print volume as big as your room allows.
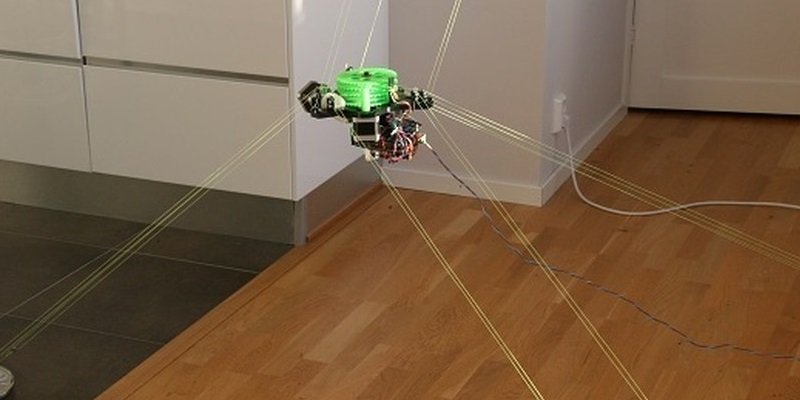
Hoping to inspire others to try frameless 3D printing, Torbjørn made the files open-source, making them free for anyone to replicate, improve upon, and even sell. Most of the Hangprinter’s parts can be 3D printed themselves, and its construction is estimated to only cost $250.
Is Furniture 3D Printing Really That Easy?
As a relatively new technique, only making its debut in mid-2017, few examples of Hangprinted projects exist, however, furniture projects are among them. Specifically, a lampshade printed in its first promotional video, and Chris Riley’s Hangprinted stool.

Despite proving that this technique can indeed print furniture, these videos also exposed significant shortcomings.
Constructing and operating the Hangprinter requires a familiarity with 3D printers, as well as an understanding of mechanics, electronics, and debugging. Despite this, there are detailed instructions for new users, as well as a small but growing community of other Hangprinter users that can be turned to for help. The impact of this skill requirement will ultimately be dependent on how much trial and error you are willing to endure.
Additionally, Chris Riley’s stool printed with both layer shifts and layer adhesion defects. Perhaps most significantly however, the print ended up taking 14 days to complete, mainly because the Hangprinter was so loud that it couldn’t be run 24/7 in his home.
For furniture printers willing to put up with these shortcomings, Hangprinting remains the cheapest and most accessible way of producing entirely 3D printed furniture. Even if it isn’t quite as easy to use as the more professional options we’re about to discuss.
Option 2: 3D printing furniture with a large 3D printer
Household furniture tends to be much bigger than a desktop 3D printer’s maximum build volume, so our second technique is perhaps also the simplest approach: using a much bigger printer.
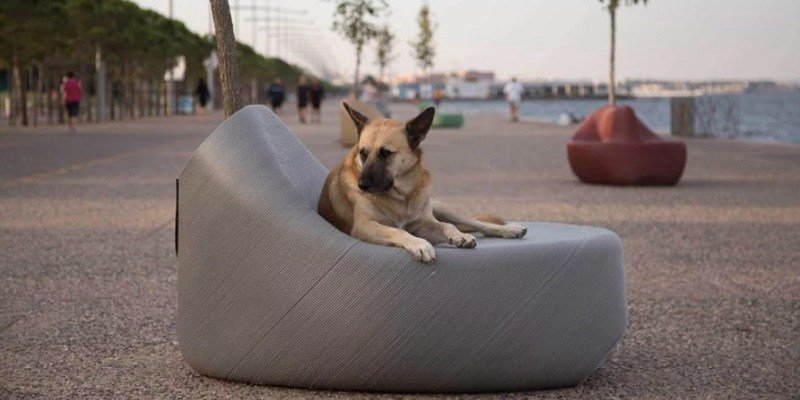
Although straightforward, this technique is inaccessible for most individuals. Large 3D printers not only take up a lot of space –sometimes entire rooms — but are also incredibly expensive. Although prices have fallen recently, large industrial 3D printers can still cost hundreds of thousands of dollars.
As a result, very few furniture projects are produced by individuals. Instead, 3D printed furniture has tended to be either the ventures of large companies, or artisan pieces, with Wilkhahn’s stool being an example of both.
Wilkhahn Printstool One
Designed by Thorsten Franck and produced by Wilkhahn, this 3D printed stool was produced on an industrial 3D printer and is available as a part of Wilkhahn’s range of premium office furniture.

Wilkhahn, a furniture manufacturer based in Germany, sees themselves as set apart from the rest of the industry. “Unlike virtually any other manufacturer in the office furniture industry, Wilkhahn stands worldwide for designs made in Germany. It offers high-quality office and dynamic conference furniture which are benchmarks for the entire industry.”
The Printstool One represents one of the few commercially available pieces of 3D printed furniture available today. It can be completed in a few hours, including assembly of the non-3D printed base and seat. The main body is 3D printed with lignin, an organic biopolymer which makes the stool completely biodegradable.
Despite being commercially available, the Printstool One isn’t easy to obtain. It is not part of Wilkhahn’s main catalogue, only produced in a limited edition 500-piece run.
The price for each unit is undisclosed and likely varies with customization options. Using Wilkhahn’s main catalogue as a guide, their conventional stools cost between $266 and $660; assuming that the Printstool One matches these prices makes it a very expensive plastic stool.

Paying a premium for high-quality furniture is nothing new however, with Wilkhahn itself being a good example of that. This pricing however still makes the Printstool One too expensive for most individuals just trying kit out their home office.
However, over the last few years, concerted efforts by some 3D printer companies may have reached a turning point in making large-format 3D printing far more accessible.
Making Large-Format 3D Printing cheaper
Printing on large 3D printers will always be expensive, however recent years have seen some companies produce models specifically to be as affordable as possible.
These printers still cost tens of thousands of dollars, making them unsuitable for most individuals looking to try out furniture printing; but they have allowed more designers and smaller manufacturers to experiment with furniture 3D printing.
RH Engineering & ManoFigura Home Furnishings
With a promotional push in mid-2020, this pair of German designers hope to disrupt the luxury furniture and furnishings industry with their signature “Manoveneer” finishing technique, and large-scale 3D printing.
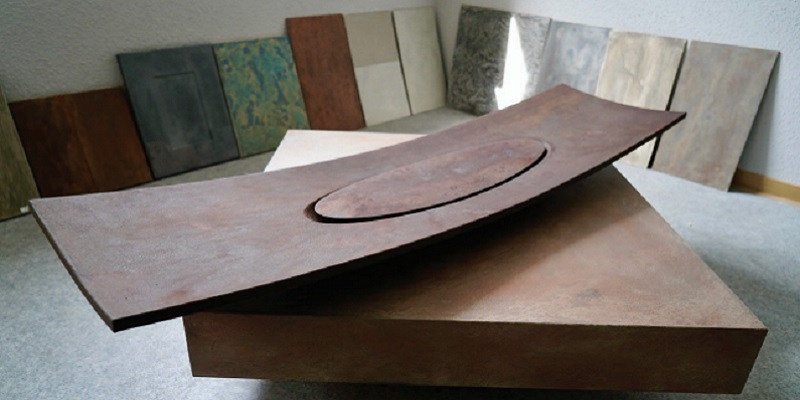
Their printer of choice is a BigRep One. The printer is big enough for furniture printing, with a 1005mm³ build volume, but comes with a $39,000 price tag, depending on specifications.
Their process begins by 3D printing artisan furniture based on a client’s design. The piece is then coated with their signature “ManoVeneer.” What Manoveneer is made from isn’t revealed, but we know the coating is waterproof, and can add a range of surface textures to granite, slate, and sandstone, while weighing far less.
The duo has seen much success since their launch, launching their webstore in late 2020. Pretty impressive for a pair of designers in the mountains of Schwarzenberg.
Option 3: Producing furniture with a small 3D printer
Large 3D printers will always represent a barrier to furniture 3D printing due to their size and expense, prompting designers to look for ways to work around using them.
Instead, designers are turning to small 3D printers, and printing multiple smaller parts before assembling them, combining 3D printing and conventional furniture making. The former being used to construct the Supermod.
“Supermod” 3D Printed Wall
Designed by the founders of Simplus Designs, the Supermod is made up of individually printed storage modules joined together to make a modular storage “wall.”
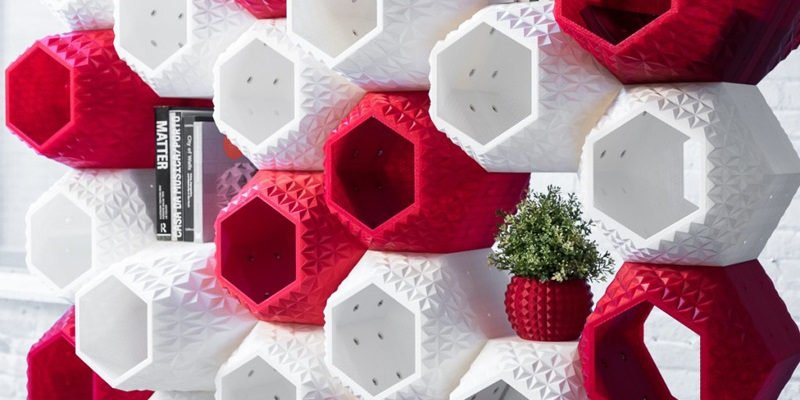
Intended to be a home furnishing, the Supermod’s patterns and opacities are designed to allow sunlight into each module’s contents during the day, as well as produce a glimmering effect around the wall’s room.
As a modular system, the Supermod also sidesteps the need to use large-scale 3D printers. Despite the wall being taller than most people, each module can be printed on an affordable 3D printer.
The later method, incorporating 3D printed parts into conventional furnishings, is perhaps the most accessible technique provided that the end-user has some knowledge of furniture construction. This technique can also be scaled up or down for use in amateur projects or designer pieces such as the “Saul” series.
Jon Christie’s “Saul” Dining Table & Chairs
Jon Christie, a bespoke furniture producer, spent 20 years trading modernist furniture before returning to university at the age of 40.
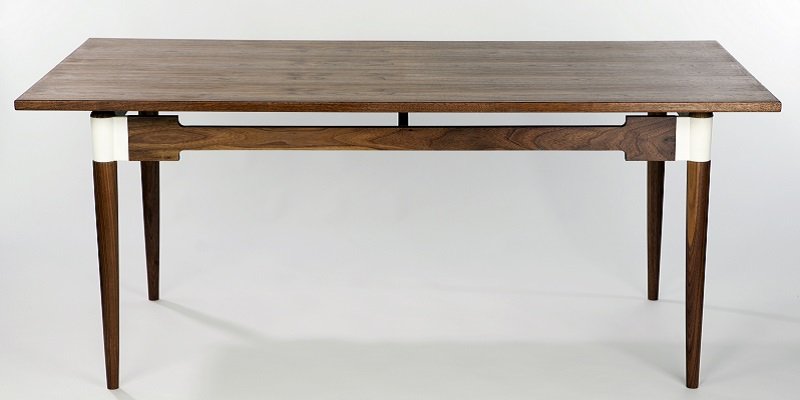
“During my student years, I became interested in 3D printing and how I might integrate it with traditional furniture making. The projects I worked on explored how 3D printed parts could be used to assist the furniture maker and manufacturer.”
He is most famous for his “Saul Dining Table & Chairs,” the 3D printed table is an artisan piece made from wood with 3D printed joints. He has theorized that his 3D printed joint system would allow for “greater customization, quicker production times and reduce waste” when applied to existing pieces of furniture. His set was displayed at the Royal Academy of Art Edinburgh in 2016.
Despite being artisan pieces, this technique has also been used by individuals in amateur furniture making, with many of these creators, much like our next project, uploading their creations to video sharing platforms such as YouTube.
Alexandre Chappel’s Side Table
Designer and Youtuber Alexandre Chappel documented the construction process of his own wooden side table with 3D printed joints. Like Jon Christie’s project the only 3D printed parts in this table were the joints, with the rest of the table being constructed out of wood with conventional hand tools.
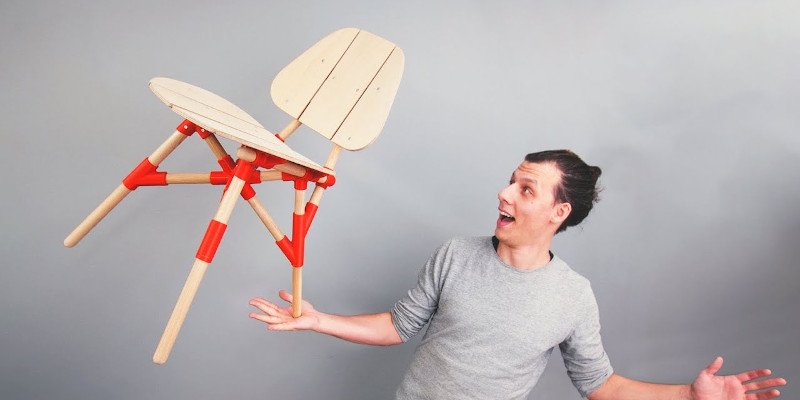
He has made the STL files and instructions available on his personal website for only $5. With the rest of the table’s material costs easily being under $100, this is perhaps the most accessible way to 3D print your own furniture.
Despite their successes, the fact that both Jon and Alexandre’s projects are mainly made of wood does raise significant questions: is using a minimal amount of 3D printing the only way to accessibly 3D print furniture? Is a table mostly made of wood actually a 3D printed table?
Although these questions don’t diminish this technique’s potential, they will need to be answered by an end-user.
Which technique should I use to 3D print furniture?
So, which of these three methods should you use for your own furniture project? Well, that depends.
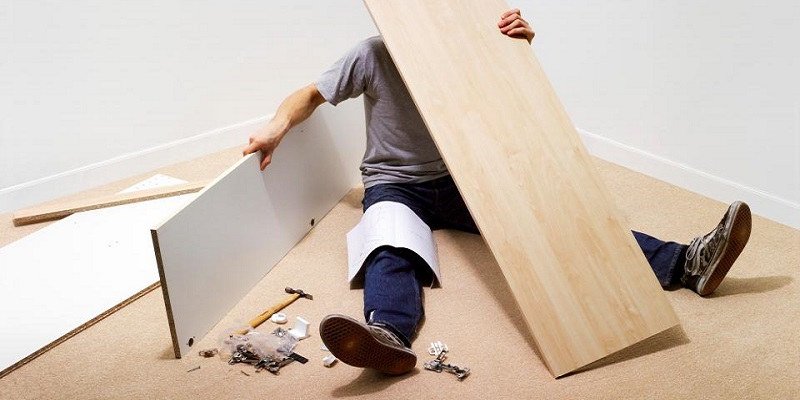
If you’re a professional studio or independent designer with the necessary funds, and you have a project that needs to be printed reliably and to a high quality, then a large 3D printer could serve you well.
If an industrial 3D printer is unaffordable, then high-quality pieces can still be constructed by using 3D printing alongside conventional techniques. That is, provided you have existing furniture construction skills, as these pieces will only be as good as you are at building them.
And if you’re willing to jump onto an emerging technique, and possess both the technical skills, and patience, to endure its current shortcomings, then Hangprinting could prove perfect.
And regardless of your chosen technique, you can do so with the confidence that 3D printing furniture is no longer an innovation for the near future. It’s something you can do in your living room right now.