
Steel 3D Printing: Everything You Need To Know

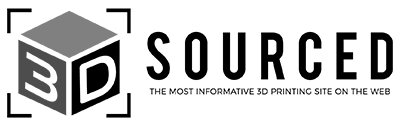
At 3DSourced we’ve covered everything 3D printing and 3D since 2017. Our team has interviewed the most innovative 3D printing experts, tested and reviewed more than 20 of the most popular 3D printers and 3D scanners to give our honest recommendations, and written more than 500 3D printing guides over the last 5 years.
New techniques in steel 3D printing are creating new possibilities for the future of steel production. While limitations on the technology such as scalability were an obstacle to further progress, metal 3D printers have begun to overcome those obstacles.
Previously, metal 3D printing was limited to very small components, preventing scaling of both the part itself, and the manufacturing process. However, those limitations could soon be a thing of the past with new advancements in 3D printing steel.
The History of Steel 3D Printing
Steel’s uses in manufacturing go back as far as 1800 BC. It is typically created by combining iron with carbon to increase its tensile strength and reduce brittleness. In the late 1700s it was discovered that steel could be combined with chromium to produce stainless steel, giving the material a shiny, metallic look that prevented other elements from sticking to it or staining it.
Traditionally, steel is manufactured by purifying liquid iron with high-pressure purified oxygen blasts to remove unwanted elements like Sulphur. Carbon is then added and it is then cooled to form steel. Extra work is then required to create the desired end user products.

Both steel and stainless steel have a number of useful properties. First, steel is an extremely strong metal. Some steel alloys have double the tensile strength of even the hardiest aluminum alloys, and stainless steel even more so.
What’s more, the iron in steel makes it magnetic, enhancing steel’s use in shipping and transport. Unlike many metals, however, steel’s high oxide concentration makes it a poor electrical conductor. Instead, it is used as a metallic insulator where careful electrical transfer is important, such as in the energy sector.
The 3D printing applications have piqued the interest of engineers, as other metals used in these sectors, like titanium, have proven the benefits of the technology.
If you are interested in purchasing a metal 3D printer capable of 3D printing steel:
*One of our trusted partners will be in touch following a quote request.
The Steel 3D Printing Process
Steel 3D printing uses similar processes to that of titanium and aluminum, namely Direct Metal Laser Sintering (DMLS) and Direct Energy Deposition (DED).
- We also have a guide to aluminum 3D printing.
- We also have a guide to titanium 3D printing.
DMLS uses a roller to spread steel metal powders over a baseplate. The printer’s laser then selectively sinters the steel powder to form a solid metal part. The baseplate is then lowered, and more powdered metal is spread across for the next layer to be sintered.
DED is slightly different, and more reminiscent of FDM 3D printing methods that use filaments. With DED, a metal wire is heated using plasma, and the liquid metal is deposited in layers to form the finished product.
3D printing is a much more targeted and precise method of metal construction, and has already shown it is capable of producing better quality products at a cheaper price with lower energy consumption. While the current part production time is a lot slower than traditional manufacturing methods, the industry’s rapid and continued evolution is improving print speeds every year, as shown by Desktop Metal and a number of other successful metal 3D printer companies.

Steel 3D Printing Applications
Energy
Almost every form of energy production uses steel in some way, making it one of the most prevalent materials in the industry. Steel is used in nuclear and fossil fuel-based energy in the manufacturing of mining equipment, offshore oil platforms and storage tanks.
Energy pylons, generators and turbines are also made of steel, with some of the largest turbines able to operate at 250 megawatts of power, enough to supply a city of 300,000.
Renewable energy sectors also benefit. Hydroelectric dams are reinforced with steel, and wind turbines are extensively made using steel. 3D printing increases the efficiency of the parts it creates through targeted, microscopic design, and in an industry where efficiency is everything, steel 3D printing could have an enormous impact. Reducing waste also brings down costs.
The United States Department of Energy announced in February 2020 that they would be partnering with additive manufacturers to begin 3D printing blades for wind turbines, which are traditionally made from steel. With this news, it is clear that steel 3D printing has an important place in the energy sector, both now and in the future.

Medicine
Stainless steel is a popular material used in a variety of surgical applications. Surgical implements and medical equipment use steel for its corrosion-resistance and non-toxicity. It is also easy to sterilize, making the implements easily reusable. Steel is further used in bone reconstruction and replacement as its strength helps to protect the damaged area and keep it fixed in place.
Dentists also use steel for needles and root canal treatments for the same reason. The ability to produce customized items, specifically tailored to each patient on-demand, is a huge benefit for patients and dentists as it saves time and money.

Transport
Steel is vital for all kinds of transport systems, from cars, to boats, to trains. External panels and intricate internal components use steel for its strong impact and corrosion resistance.
In planes, steel is used in engines and landing gear. 3D printed parts are lighter than their traditionally manufactured equivalents, and in industries where weight reduction is key, steel 3D printing is a crucial tool.
3D printing these parts lowers costs, which in sectors like the automotive industry means lower costs for consumers. With 3D printing becoming capable of larger-scale production year on year, it might not be long before entirely 3D printed transportation reaches industrial levels.

The Advantages and Disadvantages of Steel 3D Printing
Advantages of Steel 3D Printing
Strength and Durability
Steel is widely renowned for its strength and durability under stress. Steel has many uses in industries such as transport and energy where high impact resistance is vital.
Rather than producing generic parts, steel 3D printing allows custom parts to be produced for specific needs. Prototypes or single parts can also be made more cost effectively with 3D printing for research and development.
No Forging
Unlike traditional steel manufacturing, 3D printed steel does not require any forging to produce. While heat treating, as well as a certain amount of machining, is required to create more professional and durable parts, there is no need for melting or significant heating of any kind before production.
Steel’s high heat resistance requires great amounts of energy to melt and mold. With 3D printing’s targeted melting process, those high energy costs are vastly reduced, making 3D printing steel much more cost-effective for manufacturers. This also has the added benefit of making steel production more accessible for individuals and hobbyists.
Larger Sized Parts
DMLS printers are usually only capable of small build volumes, and larger industrial ones can cost millions of dollars. This means that the technology is very limited in what it is able to achieve. However, steel is a material of focus for 3D printing engineers looking to change this.
German manufacturing giant Siemens has developed a new method called Wire Arc. Using an iron filament, they are able to print parts of much greater size and weight than with other 3D printing methods. They believe this development has the potential to greatly increase efficiency in a wide array of industries, and expand the 3D printing market beyond where it was previously with new possibilities for production.

Limitations
Requires Heat Treating and Machining
Steel 3D printed parts require some aftercare in order to make high-quality products. Steel parts need to be heat treated to purge imperfections and reduce irregularities. Moreover, to get the best quality shape and finish, many manufacturers still use milling to round off the part and give it a more professional look.
Even though it is only a minor inconvenience, this affects production time and costs due to the need for extra equipment.
Potential for Porosity
Steel is extremely susceptible to porosity, where small pockets or air bubbles form within the internal structure of the component, and undermine the strength of the steel. The finished part therefore has a much higher risk of splitting or shattering, especially if not detected before being put into use.
The damaging effects of porosity can be mitigated by the heat treatment process, but with steel porosity is always a risk. Researchers are developing ways to minimize these flaws and maintain the strength of the steel throughout the process, but for the foreseeable future, the risk will be there.
Where Does Steel 3D Printing Go from Here?
There are a number of companies looking to take steel 3D printing into the future with new developments and technologies.
Where previous metal 3D printing technologies had major part size limitations, Wire Arc additive manufacturing developed by Siemens is changing that. The process is very similar to DED, where steel and iron wires are melted and layered within their machine to produce the parts.
However, their Wire Arc machine is able to print much larger parts, both in size and weight, than traditional DED or DMLS machines, as much as 800-900 millimetres length. What’s more, as it is a metal wire being melted, the process is much quicker than DMLS, as the metal is fed through a single heated nozzle as opposed to heating small areas over a wide surface. Siemens claim they are able to 3D print 3 or 4 kilograms of steel per hour.
This will no doubt revolutionize metal 3D printing. As new technologies improve and optimize the steel and stainless steel 3D printing process, additive manufacturing will become more and more viable for industrial steel production.
And other companies are focused on democratizing metal 3D printing. American 3D printer manufacturer Markforged have developed the MetalX, a metal 3D printer that uses metallic filaments that can go from design to functioning part in as little as 72 hours.
The filament is created by combining steel powder with other materials that will produce a finished product with the look, weight and strength of pure metal, for a fraction of the cost. Stainless steel filaments costs only $130 per kilo, much less than most metal powders used in other 3D printing methods.
With steel 3D printing constantly developing, its biggest industries will soon begin to see the benefits that the technology can offer, and with previous obstacles removed, 3D printed steel is sure to have a bright future.
Other articles you may be interested: