
The Ultimate Guide to Concrete 3D Printing

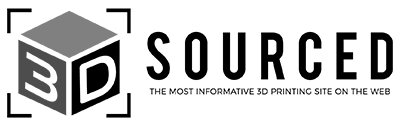
At 3DSourced we’ve covered everything 3D printing and 3D since 2017. Our team has interviewed the most innovative 3D printing experts, tested and reviewed more than 20 of the most popular 3D printers and 3D scanners to give our honest recommendations, and written more than 500 3D printing guides over the last 5 years.
The 3D construction industry is evolving quickly and expected to reach a market value of $1,575 million by 2024, a huge increase from the meager $3 million in 2019.
And with that comes the undeniable growth and impact of concrete 3D printing, or C3DP.
As the most prevalent form of 3D printing in construction, concrete 3D printing builds houses in record time and at lower prices, improving production in a way that traditional building methods can’t compete with. Streamlining operations has never been easier when technology can craft 3D printed concrete molds and assemble entire buildings within days or even a day.
But how does it work?
Join us as we go through the ultimate breakdown of concrete 3D printing. We’ll cover how this technology works, what methods are available, current market-leading concrete printers, and the projects they’re working on now!
How Does 3D Concrete Printing Work?
Concrete 3D printers work in the same way as an FDM 3D printer — they both print layers to create the finished object. Just instead of a plastic filament, concrete 3D printers extrude concrete mixtures specifically manufactured for that project.
Now, there are some differences.
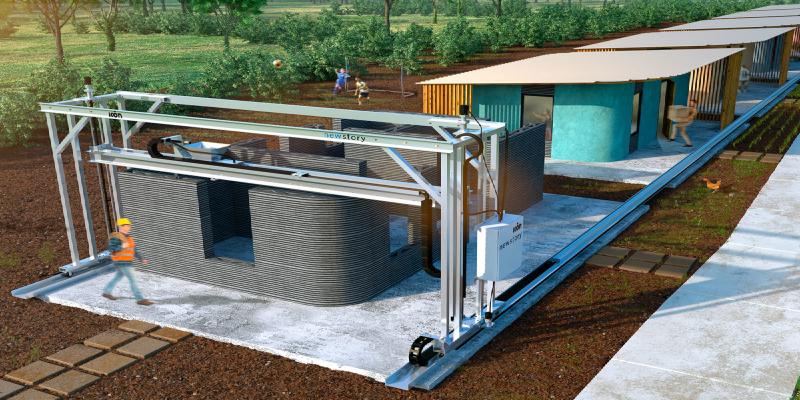
First, the printer is much larger — printing a whole house or building requires an industrial-sized printer. Second, its software program is much more advanced. In construction, the integrity of the infrastructure is under huge scrutiny, so zeroing in on geometric precision is crucial to the foundation and layout of the building.
- We also have a feature story covering 3D printing in construction.
Like with all 3D printing, you have to model the object first. This is how the printer knows what it’s printing. So, with either an outsourced or company-specific program, 3D modeling software is used to create the intended structure and then programmed into the printer.
From there, once the printer is set up, the structure is printed either onsite or off-site of the location of the final product.
The Different Types of Concrete 3D Printers
There are two main types of concrete printing used in construction: gantry systems and robotic arm systems.
Each method uses a different system to 3D print concrete, and some projects are better suited to each type.
Type 1: Gantry Concrete 3D Printers
First up we have the gantry style printer. This is the more popular method out of the two.
Named for its hanging-like structure, a gantry system involves a secure-hanging printer head that pivots from an x, y, and z-axis. Imagine the classic arcade claw game, where the claw points downwards and moves along the roof to the desired location.
The printer can move up-down (z-axis), forward-backward (y-axis), and side-to-side (x-axis). The printer sits around the intended structure and then prints layers of concrete, creating the desired object inside the boundaries of its axes.
A great example of this is the COBOD BOD2 printer from Denmark. It features a large structure that swivels the printer head, round and round, until the project is complete.
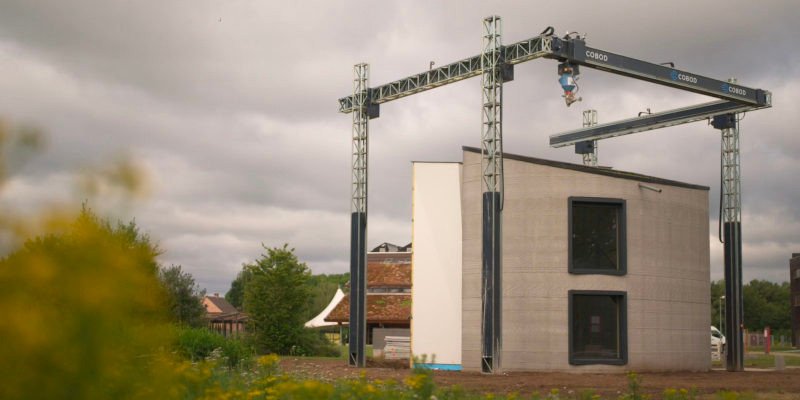
Due to its size and moveability, seldom are they ever employed on smaller projects, mostly used for housing or commercial buildings.
There are some strict advantages to using a gantry printer. First, they’re capable of printing bigger jobs than robotic arm printers. You can print entire buildings, as opposed to printing piece by piece and transporting them to their final destination.
Second, it’s more cost-efficient, structurally stable, and easier to control than robotic arm printers. Gantry offers non-continuous printing and does not require extensively trained programmers for operation. Not to say professionals aren’t integral to the process, however, there’s more forgiveness with a gantry system.
We recommend this style for larger minimalist projects that focus on structure and efficiency rather than detail.
Type 2: Robotic Arm Printing
Next is robotic arm concrete 3D printing, which may not be as popular, but easily just as powerful.
A robotic arm concrete 3D printer has a moveable printer head like gantry printers, however, instead of moving around a defined space, or grid, it’s a crane-like structure that contains 6 axes. They still move between the x, y, and z planes, but they are afforded more flexibility and reach when doing so.
A robotic arm then holds out the printer head and moves it around, layering the concrete until the project is finished.
You can see this in action with the CyBe RC 3Dp, which we’ll also explore in-depth further in this article. The robot acts as a giant limb that can direct and move the printer wherever necessary.

Robotic arm printing trumps gantry in detail and compactness. Robotic arms are notoriously easier to set up and take down and can print more complex detail and geometric precision than a gantry system.
This is all thanks to the robotic arm, which allows for free-flowing actions, unlike the gantry, where it’s confined to the boundaries of its axes. It does require experts to operate, but trained technicians typically come with the use of the printer. It’s also capable of working on smaller projects since users have greater control over the printer head and it can create finer detail.
Out of the two types, the gantry is the bulkier version that can handle bigger jobs and offers easier programming, and the robotic arm is limited in terms of scaling up but offers skilled precision and portability.
Common Applications for Cement 3D Printing
There’s no shortage of potential and imagination when it comes to applying cement 3D printing across various industries, but the most widespread application of C3DP is 3D printed concrete houses.
All over the world, 3D printed houses have popped up thanks to the technological advancements in 3D concrete printing. There are even a few projects underway that are aiming to 3D print entire communities and neighborhoods, creating a future blueprint of what could become the new norm.
- More information on these projects can be found in our exciting list of 3D printed homes.
It’s also popular with engineering commercial buildings, like the offices in Dubai and the hotel in the Philippines.
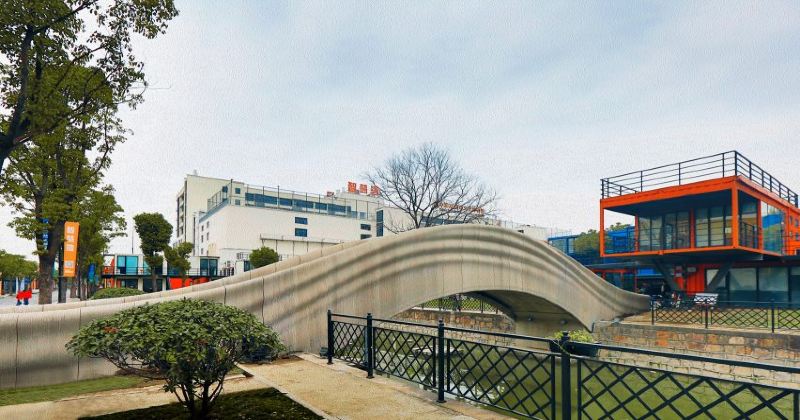
Some non-housing structures include bridges and monument letters that are made with the MudBots concrete 3D printer, and decorative features like fireplaces and water fountains. Systems like drainage structures also benefit from this technology.
- We also have a guide to and ranking of the best ceramic 3D printers.
The Leading Concrete 3D Printers for Sale
To wind down our trip through the mechanics and uses of concrete printing, we’re going to list the top concrete 3D printers currently on the market and what projects they’ve worked on.
While these printers are the top runners now, this is by no means an exhaustive list of the amazing work being done in the world by concrete printers or the last we’ll see.
ICON’s Vulcan Printer
Starting us off is the gantry-style beast Vulcan, ICON’s 3D printer.
The Vulcan is one of the most popular concrete printers on the market, costing up to $250,000, and is known for its extensive use on 3D printing houses across the US and Latin America.
Specs include an 8.5ft print height, 28ft print width, and prints 1in tall, 2in wide cement beads at 5-7inches per second. It boasts a vertically-integrated tech stack that allows you to control the robotics and complete 3D modeling from a tablet and use programmable cement mixtures.
Its focus is on building ergonomic, durable single-story homes, but at rapid operating speeds.
Current projects you can see the Vulcan in action on is the New Story initiative taking place in Latin America. Here, they work with poverty-stricken communities to create neighborhoods of 3D printed homes for affordable prices they can pay.
They’re also turning heads in East Austin, Texas, where it plans to open a street of 3D printed homes for sale in the summer of 2021.
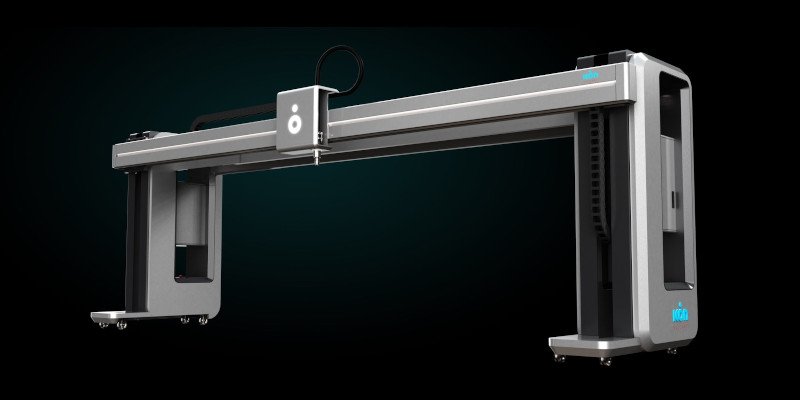
COBOD’s BOD2 Printer
Next, we have COBOD’s BOD2 printer, Europe’s prized gantry printer possession.
Construction of Building on Demand built the second-generation BOD (the only second-generation printer on the market) as a modular 3D construction printer. Each printer comes with a customizable printer head and a minimum of 1 x-axis, 2 y-axes, and 4 z-axes for full area printing inside the cube-shaped printer.
Their construction printers can cost up to €1 million and come in three different models, each varying in size and number of axes, the biggest offering a print area of 12.10 x 24.75 x 8.14m.
BOD2’s unique features include its surface mapping tool, which allows you to print on uneven surfaces by mapping out and calculating the uneven floor trends, and it can print with a variety of mixtures with its open material compatibility system.
It makes a point to specialize in customization for customers with modules and axes varying for each project, offering excellent scalability.
The most notable project this printer has worked on is the Kamp C build, which was the first two-story house printed on-site. They also 3D printed the first ever wind turbine in June 2020, and once they solve the remaining logistical issues, they hope to see them out on the fields.
CyBe Construction’s CyBe RC 3Dp
Finishing off our list is CyBe’s robotic arm concrete printer.
Hailing from the Netherlands, CyBe design their printers around versatility, offering a fixed 3D concrete printer for €150,000 and a mobile one for €180,000. Both come with a robotic arm, CyBe control software, mix pump system, material storage, and training for up to three people.
The fixed CyBe R 3Dp acts as an entry-level concrete 3D printer and is ideal for research, universities, and those looking to conduct prototyping and in-house testing. The mobile CyBe RC 3Dp is ideal for construction due to its portability. It sits on movable rubber tracks so it can maneuver and print on uneven terrains and stabilizes with retractable hydraulic feet when printing.
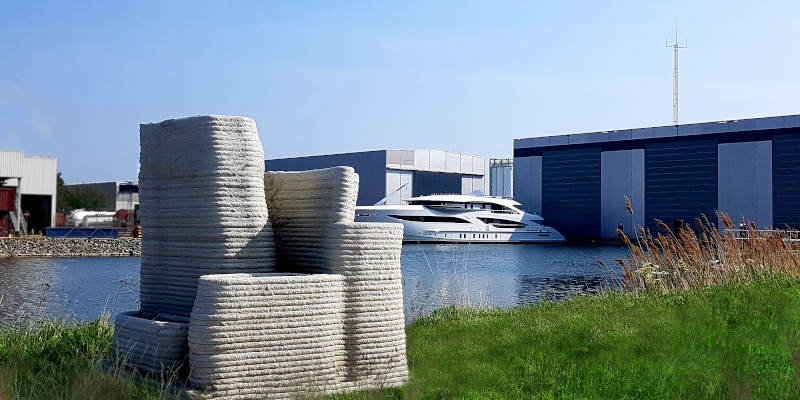
CyBe has an impressive resume under its belt in way of projects.
On top of their efforts to build affordable housing, they’ve also successfully 3D printed concrete artificial coral reefs to help protect, rehabilitate, and stimulate marine life and prevent coastal erosion. They were also commissioned by Haarlem, a city in the Netherlands, to 3D print a series of concrete benches to furnish the city.
These examples showcase the level of intricacy that robotic arms can reach and highlights its true differences from gantry style printers.
Future Outcomes of Concrete 3D Printing
With so many successful outcomes already available, like 3D housing communities and marine conservation, and more cutting-edge projects underway, it’s hard to believe this technology isn’t affecting more of our everyday lives.
So far, the biggest hurdles in the way of concrete printing are the public’s perception of the safety and potential of this technology, and logistical issues when it comes to size and transport for bigger projects like wind turbines.
That hasn’t stopped people from dreaming big though, as there have been recent discussions about 3D concrete printing in space and developing the first-ever human habitat on another planet. As we continue to shed light on the possibilities, and companies continue to experiment, we believe it’s safe to assume concrete 3D printing is only in the embryonic stages of its work.