
Is Rubber 3D Printing Possible? We Explain All

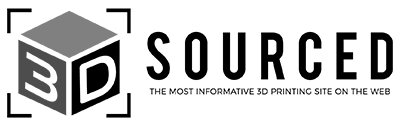
At 3DSourced we’ve covered everything 3D printing and 3D since 2017. Our team has interviewed the most innovative 3D printing experts, tested and reviewed more than 20 of the most popular 3D printers and 3D scanners to give our honest recommendations, and written more than 500 3D printing guides over the last 5 years.
3D printing using flexible filaments that mimic rubber proves just how versatile the industry has become. The sheer range of properties and applications of 3D printable materials is truly remarkable. And with rubber-like 3D printing, the range is stretching further than ever before. But can you 3D print actual rubber?
This article will discuss whether 3D printing rubber is possible, alternatives to 3D printing rubber, and the pros and cons of printing rubber-like materials.
Is Rubber 3D Printing Possible?
The 3D printing industry is constantly broadening its horizons, and finding more reliable ways to print useful materials. Rubber is one of them. Rubber’s elasticity, durability and stress-resistance make it a useful everyday material. On top of this, rubber is vital for advanced industries like transportation and robotics.
However, calling it rubber 3D printing is a slight misnomer. 3D printing rubber is not technically possible, and this is due to the way rubber is traditionally produced.
Rubber is traditionally harvested from the latex of rubber trees, mostly farmed in Indonesia, India and throughout East Asia. The sticky, milky fluid is extracted and treated using formic acid. It then undergoes a process called vulcanization, where the rubber is heated to extremely high temperatures for it to harden and become elastic.

This process prevents true rubber from being used in traditional 3D printing.
Once rubber is vulcanized, it can never be stably remelted, and since FDM 3D printing involves melting plastics to deposit them, you cannot 3D print real rubber. In fact, any exposure to high levels of heat is likely to burn the rubber rather than melt it.
This is the Catch 22 of rubber 3D printing. The very aspect that makes rubber such a useful and reliable material is what prevents it from being 3D printed. There are no true 3D printing rubber filaments or resins that exist.
And for this reason, researchers have dedicated themselves to finding alternative materials that will do the job instead. Here are some 3D printable rubber-like materials:
The Rubber 3D Printing Materials You Can Use
TPU
Thermoplastic Polyurethane (TPU) is considered to be the most rubber-like 3D printing filament. TPU can be 3D printed in its pure form, but it is also a popular additive in other plastic compounds to give them a more rubber-like consistency.
However, TPU is becoming more renowned in its own right for its ability to create durable, yet flexible, parts. And TPU 3D printing filaments are available for between $35-$55 per kilogram.
3D printed TPU parts have a number of advantages. They’re very stretchy and elastic, and have excellent impact resistance and shock absorption, making them ideal for commercial uses and hobbyists alike. They also do not degrade or corrode, giving TPU products a long lifespan.
However, there are a few caveats. Due to the softness of the material, TPU must be printed at low temperatures. While this does mean there is a low potential for shrinkage or warping, it is also susceptible to clogging and stringing. Additionally, its rubber-like consistency means that it is very difficult to post-process.
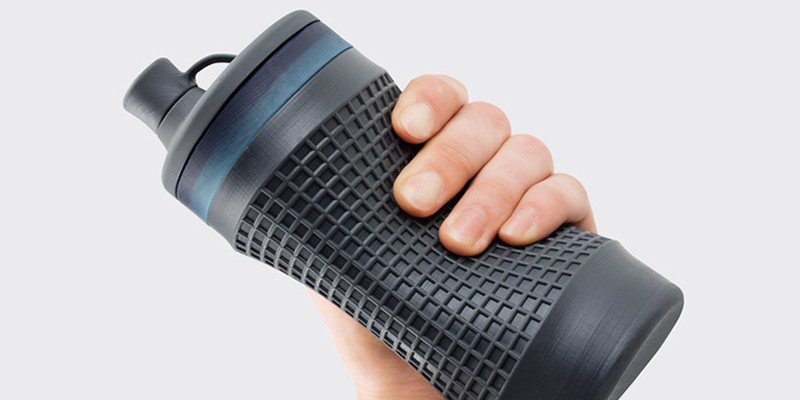
PCTPE
Plasticized Co-polyamide Thermoplastic Elastomer (PCTPE) is a compound of TPE and nylon. It is one of the easiest rubber-substitute 3D printing filaments to print on the market. The filament has the flexibility and impact resistance you would expect from a rubber material, while also being much less hygroscopic than pure nylon.
Unlike a lot of other flexible polymer filaments that require specific settings and setups to get consistent results, PCTPE can be reliably printed under a variety of different environments.
It’s strong and durable, and more hardwearing than almost any of its rubber-like competitors, able to withstand more than its fair share of punishment.
PCTPE is an excellent choice if you are patient and savvy enough to get it right. However, some makers say the material can be difficult to adhere to the print bed, even with the use of glue or tape.

Soft PLA
Soft PLA, sometimes called PLA+, is a flexible filament that infuses standard polymer PLA with either TPE or TPU. This gives it a springy rubber quality, and can be bent and pressured without breaking, making it ideal for use in products like phone cases that need to be stretchier to absorb shocks.
However, it warps more than PLA, and while being impact resistant like many other rubber filaments, is considered weaker than standard PLA.
However, soft PLA more than holds its own against alternative materials, with a competitive tensile strength and greater elasticity than TPU. It is on the more expensive end of the price spectrum, costing around $60-$65 per kilogram.

The Pros and Cons of Rubber 3D Printing
Advantages of 3D printing rubber
Cheaper
Rubber 3D printing has an edge over traditional manufacturing methods in cost similar to Silicone 3D printing, as we have discussed before. Once vulcanized, rubber is usually manufactured through injection molding, and the molds required to do this can be hugely expensive, some as much as $100,000 each.
This not only demonstrates 3D printing’s superiority as a prototyping technology, as well as for limited run production, but also for general manufacturing. It requires no molds, vastly reducing the upfront costs and giving manufacturers more freedom to change designs.
Durable
Rubber 3D printed parts are incredibly durable and resistant to a number of damaging influences. They can be bent and squashed, retain their structural integrity, are impact resistant, flexible, and durable over the long term.
Little Warping
It is often recommended to 3D print flexible filaments at lower temperatures to avoid damaging or weakening the material’s properties.
This also reduces the likelihood of any part warping occurring. This makes the overall production much more reliable and requires less aftercare.

Cons
Prone to Clogging and Stringing
Having to 3D print rubber filaments at low temperatures increases the risk of the filament clogging and blocking the nozzle, which could damage the 3D printer itself. Stringing is also a problem, with leftover strands of filament ruining the professional finish of the part.
Difficult to Post Process
Once 3D printed rubber parts are completed, it is next to impossible to remold or alter their shape through post processing methods. This can be a beginner’s trap as you have to get it right on the first attempt, otherwise you’ll have wasted your time, materials and money.
Poor Adhesion
A common problem with all rubber 3D printing filaments is poor bed adhesion, making it difficult to get a solid foundation on which to build.
There are ways to overcome this problem, such as changing your bed material, or using glue or tape on the bed, but you run the risk of a deformed part, or even cracks and splits forming in the structure itself, making the whole thing useless.
Rubber 3D Printing Applications
Sporting Goods
The sporting goods market uses traditionally manufactured rubber for a range of different products. Rubber is used for shock absorption in indoor sports like gymnastics and martial arts, and balls use rubber for their bounce.
But the biggest area for where 3D printing rubber-like filaments can contribute is personalized equipment grips. Tennis and badminton rackets, javelins, and bikes use rubber for making grips that are easy and comfortable to hold.
Another main area is in 3D printed shoes. Companies like Adidas, Nike, New Balance and many more are turning to 3D printing to create midsoles and other parts of shoes that work more effectively than traditionally made parts.
You can also read our feature story on 3D printed shoes

Producing rubber grips specifically tailored to the individual is an excellent way of improving performance for everyone from an amateur to a professional.
In elite sport, the slightest advantage can be the different between greatness and a loss. And a one-size-fits-all approach to such things is a barrier to that, especially when selling to the mass market.
Orthopedics
A similar principle is true in medicine, and specifically with rubber 3D printing, orthopedics. Personalized medical care is at the forefront of medical research, and 3D printing has already proven its usefulness in this sector, from 3D printed medical devices to 3D printed casts.

Non-essential care like orthopedics is nonetheless very important for patient quality of life, helping to reduce back and leg pain and improve posture. Rubber is used as a soft, cushioning material that can adapt to each patient’s anatomy for products like shoe insoles.
But through 3D printing, doctors can craft products designed to be comfortable and fit correctly on each individual, while providing targeted support formed around each person’s condition. This eliminates the need for generic, mass-produced items and improves outcomes.
Transport
Rubber is a vital material in the automotive industry, most obviously in the production of tires for cars, bikes and trucks.
While 3D printers aren’t large enough yet to produce tires in their entirety, the industry is constantly working to increase the scale and production capacity of its machines.

3D printing in industry has been repeatedly shown to reduce costs for a range of materials by cutting down waste, and rubber 3D printing is no different.
As the industry continues to grow, with car and bike companies already incorporating 3D printed parts into their newest vehicles, do not be surprised to see rubber become a focus in short order.