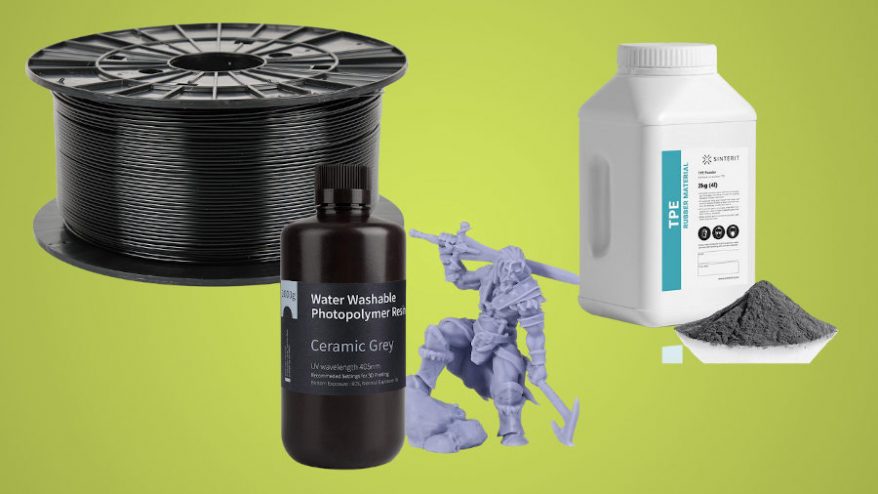
The 3D Printing Materials Encyclopedia – FDM, Resins, SLS & Metals
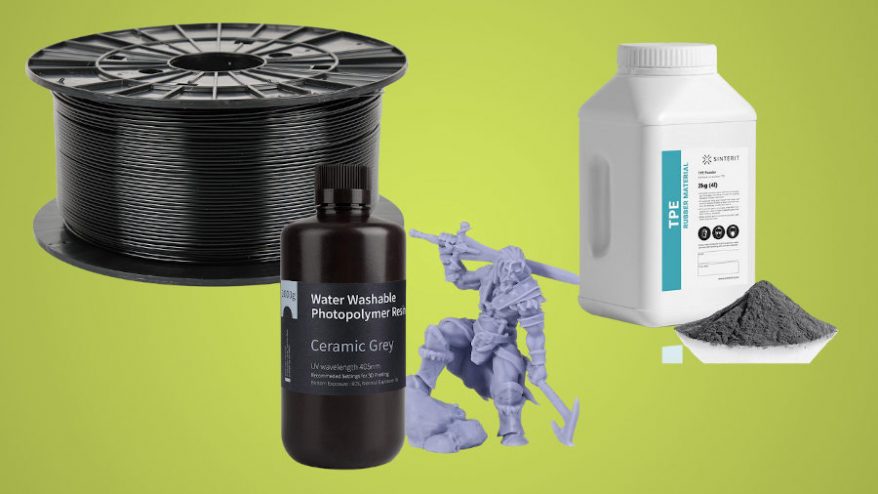
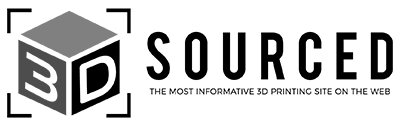
At 3DSourced we’ve covered everything 3D printing and 3D since 2017. Our team has interviewed the most innovative 3D printing experts, tested and reviewed more than 20 of the most popular 3D printers and 3D scanners to give our honest recommendations, and written more than 500 3D printing guides over the last 5 years.
There are dozens of 3D printer materials across several different technologies, each with niche uses and areas they where they excel.
But, with so many materials it can be difficult to know when to use which: which is best for prototyping, and which is best for fun home 3D printer projects?
Our 3D printer material encyclopedia covers:
- Filaments used for FDM
- Resins used for SLA, DLP, LCD
- Powders used for SLS
- Metal powders used in DMLS, EBM
- FDM 3D printing materials: filaments
- PLA
- ABS
- PETG
- TPU / Flexibles
- Nylon
- PVA — support 3D printing material
- HIPS — support 3D printing material for ABS
- ASA
- PC — Polycarbonate 3D printing material
- Wood Filaments
- Metal Filled Filaments
- PEEK
- Resin 3D printing materials
- Standard Resin
- Clear Resin
- Tough Resin
- Durable Resin
- Flexible Resin
- Medical / Dental Resin
- Castable Resin for Jewelry
- Ceramic Resin
- SLS 3D printing materials
- Metal 3D Printing Materials
FDM 3D printing materials: filaments
Fused deposition modeling (FDM) is the most accessible, and most used technology by hobbyists — and it also has uses in rapid prototyping in industry.
FDM uses filaments to print the object, melting and extruding the plastic onto a print bed using an extruder. Different filaments have widely different print settings, requirements and heats, so here’s the low-down on some of the most used filament materials:
PLA
- Printing temperature: around 200C (180-220C)
- Heated bed temperature: optional, at 60C
- Price: around $20/kg
PLA is the easiest 3D printer filament to print overall. It doesn’t warp like ABS, doesn’t require a heated bed to print (though it is an advantage), prints at a lower temperature, and adheres well to the print bed.
PLA comes in almost every color on the spectrum, as well as in a variety of hybrid forms like conductive PLA, metal-filled, carbon fiber-filled, and wood-filled options. It’s also biodegradable, made from corn starch and similar crops, so it’s the most environmentally friendly and sustainable 3D printing material.
Who is it best for?
- Beginners looking to 3D print without stress
- Makers not concerned about high temperature or impact resistance parts
- Professionals looking to prototype cheaply and efficiently
Who is it not for?
- High temperature applications
- Strong parts that can carry heavy loads — PLA is fairly brittle
Read our full guide and recommended brands here.
ABS
- Printing temperature: 220-250C
- Heated bed temperature: 90-110C
- Price: around $20/kg
ABS is another very commonly used 3D printing material, and was the most popular filament prior to PLA’s rise as another low cost alternative for home makers. It’s used by both hobbyists and professionals alike who want to make use of its low cost and high strength.
ABS’ toughness comes with some drawbacks however: its strength requires higher extruder temperatures than PLA, and at these high temperatures it can warp and crack if cooled too quickly, ruining your print. For this reason, it’s extremely important to print with a heated chamber to maintain the temperature around your print to prevent warping.
A major selling point of ABS is that due to its lack of chemical resistance to acetone, it can be fairly easily polished for a glossy finish. However, it can smell while printing, and you shouldn’t really be in close proximity to your printer if printing ABS.
Who is it best for?
- Makers looking to create tough, rugged or polishable prints with a glossy finish
- Professionals looking to cheaply produce functional testing prototypes
Who is it not for?
- Anyone without a 3D printer enclosure to carefully maintain the temperature
- Makers who don’t need the added strength and headache ABS can bring with added printing difficulty
Read our full guide and recommended brands here.
We also have a buyer’s guide for the best enclosed 3D printers
PETG
- Printing temperature: 220-250C
- Heated bed temperature: 70-90C
- Price: around $25/kg
PETG is an accessible middle ground between ABS and PLA. It’s stronger than PLA, and warps less than ABS, as well as offering some of the best layer adhesion of any 3D printing filament — owing to its sticky nature.
It’s also naturally glossy, offering an elegant, translucent surface finish that looks great on most models, and like PLA and ABS there are plenty of color options available for PETG.
However, it’s stickiness makes it poor for supports, so ideally you could instead use a dual extruder 3D printer with PLA filament supports. It’s also prone to stringing, difficult to post-process due to its chemical resistance, and is prone to scratching over time.
Who is it best for?
- Makers who appreciate PETG’s glossy surface finish
- Anyone looking to take advantage of PETG’s food-safe and waterproof nature
Who is it not for?
- Those who like to post-process their prints
Read our full guide and recommended brands here.
TPU / Flexibles
- Printing temperature: 210-240C
- Heated bed temperature: 60C
- Price: starting at $30/kg
TPU is unlike other commonly used filaments as it is very flexible — and used as a substitute for rubber (which can’t be 3D printed) when flexibility is needed.
It’s used in phone cases and other protective cases as its flexibility is great for absorbing shocks and protecting your new smartphone’s screen from cracking when you inevitably drop it. It’s also seen use in 3D printed shoes for the same shock-absorption — making sure your knees, hips and ankles don’t grind down to dust by the time you hit your 50s and 60s.
Print slower with TPU, as it can create problems if printing faster than 30mm/s. It doesn’t print at super high temperatures, but it can still be difficult to print as it can string, break and clog often due to its fragility, and until recently it was generally considered difficult to print on a Bowden extruder — though this isn’t necessarily always the case.
Who is it best for?
- Makers looking to create cool flexible 3D printed projects like phone cases, coasters, and much more.
- Professionals making shoes (or parts of shoes), tires, drive belts, caster wheels, and more.
Who is it not for?
- Anyone not looking to create flexible, rubbery parts
Read our full guide and recommended brands here.
Nylon
- Printing temperature: 220-260C
- Heated bed temperature: 70-90C
- Price: starting at $35/kg
Nylon is very strong and impact resistant, owing to its flexibility that cushions impacts. It’s similar to ABS in that it requires an enclosure, heated bed and a fairly high nozzle temperature, and without any of these, it’ll probably warp and ruin your print.
It’s also very hygroscopic. While all filaments are hygroscopic to an extent, Nylon will be all but ruined if left in the open air for too long, so you should invest in some airtight filament storage to maintain it’s excellent print characteristics.
Nylon 3D printing materials are often used to create strong prototypes that can be tested in industry, as well as for creating parts like gears, hinges, screws, and similar parts.
Who is it best for?
- High-performance prototypes for industry
- High-performance parts like screws, gears and hinges
- Impact-resistant parts where some flexibility is preferred
Who is it not for?
- Anyone without an enclosure and filament storage to maintain Nylon’s print characteristics
Read our full guide and recommended brands here.
PVA — support 3D printing material
- Printing temperature: 200-225C
- Heated bed temperature: 60C
- Price: starting at around $70/kg
PVA is well known as a 3D printing material not for its ability as a filament, but as an excellent support for PLA prints. This is because it naturally dissolves in water, so simply put your PLA print in a cup of water and the PVA supports will naturally dissolve over time, leaving you with a smooth and blemish-free print.
However, you’ll need a dual extruder 3D printer to make use of PVA in your multi-material printing adventures.
Who is it best for?
- Makers looking for blemish-free PLA prints and who don’t want the hassle of removing supports by hand
- Professionals who need impeccable prints without any surface imperfections
Who is it not for?
- Anyone without a dual extruder
- Anyone content with manually removing supports, and sanding or other post-processing methods to improve part appearance
Read our full guide and recommended brands here.
HIPS — support 3D printing material for ABS
- Printing temperature: 220-240C
- Heated bed temperature: 90-115C
- Price: starting at around $25/kg
Whereas PVA is the ideal support material for PLA, HIPS performs a similar supporting role for ABS. Since it has similar properties, prints at similar temperatures, and can also be dissolved away, it’s the ideal 3D printing material support for ABS.
The difference between HIPS and PVA however is that while PVA dissolves in water, HIPS dissolves in limonene, which can be bought cheaply from most stores. The results are the same however: impeccable parts with few surface finish imperfections.
Despite mainly being used as a support material, HIPS still functions well as a 3D printing material on its own. It’s lighter than ABS, is more impact resistant, and if you’re a fan of the glossy look, HIPS’ surface finish is clearer than ABS. It’s also cheaper than many filaments, like PVA, and has some use as a prototyping 3D printer material in industry.
Who is it best for?
- Professionals and makers looking to print ABS parts with dissolvable supports
- Professional prototyping for tough and impact resistant parts.
Who is it not for?
- Home makers with only one extruder on their 3D printer
Read our full guide and recommended brands here.
ASA
- Printing temperature: 220-250C
- Heated bed temperature: 90-110C
- Price: starting at around $30/kg
ASA is very similar to ABS, with almost identical print settings. In fact, it’s mostly used in place of ABS for outside applications as it’s UV-resistant, whereas ABS is susceptible to UV rays.
In the same way as you’d print ABS, you need an enclosure, heated bed, and higher extruder temperatures than with a filament like PLA or PVA.
It’s generally more durable and lasts longer than ABS however, for example taking longer for white ABS to start turning yellow, but is more expensive than the very reasonably priced ABS 3D printer materials.
Who is it best for?
- Anyone who wants to print tough, durable parts
- ABS users who want to print parts with outside uses
Who is it not for?
- Those who don’t need it for outside applications, and are comfortable with ABS or any other lower cost filaments
Read our full guide and recommended brands here.
PC — Polycarbonate 3D printing material
- Printing temperature: 260-310C
- Heated bed temperature: 120-150C+
- Price: starting at around $50/kg
Polycarbonate 3D printing material, or PC, is an extremely temperature resistant filament and one of the strongest materials you can 3D print.
This temperature resistance naturally makes it difficult material to 3D print, and with most personal 3D printers unable such high heats, to print Polycarbonate material you’ll either need to buy a more professional 3D printer, or upgrade to an all-metal hot end that can reach the required temperatures.
Polycarbonate is commonly used to 3D print engineering parts, as well as other accessories where strength is important, like motorbike helmets.
Who is it best for?
- Commercial use as an extremely tough material for engineering use
Who is it not for?
- Almost all hobbyist uses — it’s expensive, tough to print on a lower cost 3D printer, and other filaments can offer similar benefits for most 3D printer projects.
Read our full guide and recommended brands here.
Wood Filaments
- Printing temperature: 180-220C
- Heated bed temperature: optional, 60C
- Price: starting at around $30/kg
Wood 3D printing material isn’t exactly wood per se, but mimics the appearance of wood so well that almost nobody will know any better.
Wood filaments are typically around 30% wood (usually using sawdust), mixed with 70% PLA, so the material prints at the same temperature and with the same print settings as PLA, while offering a wood-like aesthetic.
You can use a fairly wide temperature range with wood 3D printer materials — you can even engineer a darker wood finish with a higher temperature, or a softer, more mild wood finish at lower temperatures.
3D printing wood filaments is mostly an aesthetic choice with little use in industry, but it’s a fun material for makers to create faux-wooden 3D prints that look great. You can even polish and sand it like real wood to give it the most wood-like appearance possible.
Who is it best for?
- Maker projects to make fun household decorations, appliances, and 3D printed toys
Who is it not for?
- Any functional, professional 3D printing uses or prototypes for testing
Read our full guide and recommended brands here.
Metal Filled Filaments
- Printing temperature: 180-220C
- Heated bed temperature: optional, 60C
- Price: starting at around $70/kg
Metal filaments, or metal-filled filaments, are another alternative 3D printing material mostly used for aesthetic purposes rather than professional use.
Similar to wood filaments, most metal filaments are PLA filaments, but instead of sawdust, are infused with a percentage of metal powders. The most common metal 3D printing materials are bronze, copper, and stainless steel filaments.
As they’re mostly made with PLA, these filaments don’t possess the strength or impact resistance necessary for rapid prototyping. However, they’re a lot cheaper than metal 3D printing, as these materials can be printed on most desktop 3D printers — solid metal printing requires a metal 3D printer costing $80,000+.
As a result, metal filaments are mainly used to emulate metal’s appearance, without concern over the parts being as strong as metal. Historical ornaments have been made in these metal-mimicking metals, and a variety of other fun hobbyist projects.
Who is it best for?
- Makers looking to emulate metal with their own custom 3D printed designs
- Historical ornament emulation
Who is it not for?
- Professionals looking to 3D print real metal — read on to the metal section of this article for that
Read our full guide and recommended brands here.
PEEK
- Printing temperature: 360-450C
- Heated bed temperature: 120-160C
- Price: $300-500/kg
PEEK is considered the most premium, professional, strong and temperature-resistant 3D printing material around. It’s also probably the most expensive, routinely costing over $300 per kilo. It comes in very limited colors, so it’s not for aesthetics, but purely for high-strength part production for industrial uses.
PEEK is very tough to print, with specially-designed PEEK 3D printers developed with powerful heated chambers that can maintain and handle the high temperatures for potentially days to print larger parts — PEEK prints very slowly.
It’s used to make parts for planes, cars, and other engineering uses, replacing previously used metal parts as it offers better strength-to-weight ratio than materials like aluminum — and saves weight. This is crucial in aerospace where weight adds so much to costs via increased fuel consumption.
Who is it best for?
- Industrial production of high-quality engineering-grade parts
- Medical applications, such as in sterilizable medical tools and implants
Who is it not for?
- 99.9% of 3D printing applications.
Read our full guide and recommended brands here.
We also have a buyer’s guide for the best PEEK 3D printers.
Resin 3D printing materials
3D printing materials are not limited to filaments.
While FDM is ideal for low cost 3D printing and can create tough parts, it is constrained by its lack of accuracy and rougher surface finish.
Resin 3D printing methods like Stereolithography can achieve far smoother surface finishes, resembling injection molded parts with fine details and intricacies possible.
There are a variety of different resins that you’d use for different situations, so we’ll go through them here.
Standard Resin
Standard resins are a great, relatively low-cost way to create high resolution resin prototypes.
They’re ideal for prototyping as they’re lower cost than engineering resins, don’t need UV curing after printing to reach full strength, and still offer great detail.
Within standard resins you can buy Grey resins, known for being ideal for hobbyists 3D printing miniatures as the resins are easy to post-process and paint, as well as capable of capturing small details. White resins are best for smooth surface finishes.
Clear Resin
Clear resins are fairly self-explanatory: they can be post-processed to become completely transparent. They’re not naturally this way, and require sanding and polishing after the part is printed, or spray or resin coating.
This is ideal for LED lights and for showing the inner components or features of an appliance or other product, with other projects that have used clear resin including light pipes and prisms.
Tough Resin
Sometimes called ABS-like resins, tough resins share similar strength and elasticity characteristics to the popular FDM 3D printing material — creating far tougher resin parts than standard resins.
They’re durable, and ideal for tough prototypes for functional testing, as well as for parts you know will experience heavy impacts, such as drone parts that frequently crash. These resins however need to be cured under a UV light to reach their full strength, adding time to the printing process.
Durable Resin
Not too dissimilar to tough resins, durable resin 3D printing materials are more flexible, and designed to withstand long-term wear-and-tear. Despite this 3D printing material’s ruggedness, durable resins offer smooth and attractive surface finishes.
Durable resins are commonly used for prototyping, as well as for snap-fit products due to their low friction. It’s also used for prototypes for parts that will eventually be made from PP or HDPE.
Flexible Resin
Flexible resins are TPU-resembling rubber resins that elongate when pushed down or pulled apart like rubber without breaking.
They’re super flexible and are commonly used for prototyping flexible consumer goods, for parts to be used in robotics (especially soft robotics), and in medical anatomical models, among other industries.
Medical / Dental Resin
Medical and dental resins are biocompatible resins for custom dentistry and medical models. The patient’s mouth is 3D scanned using a dental 3D scanner to create a 3D model, which is used to create the custom dental part.
Dental resins are used to print surgical guides, entire dentures, prosthetics, crowns and bridges, retainers and splints. Using resin 3D printing these dental appliances can be created on-demand, and at lower costs than traditional ways of making them.
Castable Resin for Jewelry
Increasingly, custom jewelry is being 3D printed and then investment cast. It’s probably the easiest way to create custom-fitting precious gold or other metal jewelry. Castable resins are used to print the original lost wax mold of the final jewelry piece, before it is burned off to create the negative, inside which liquid precious metal is poured to cast the final model.
Castable resins offer incredibly fine details and hold their shape well, making them ideal for jewelry. However, they’re also used to cast rubber molds.
You can also read our guide to the best jewelry 3D printers
We also have an article on the most stunning 3D printed jewelry pieces
Ceramic Resin
Ceramic resins are rigid, and usually reinforced with glass or other ceramics. These 3D printing materials offer good heat resistance and stability, though they’re more brittle than stronger resins like Tough and Durable resins.
Ceramic resin 3D printed parts have a surface finish that resembles stone, and can be used to create attractive household objects, artistic projects, and more.
We also have a guide to ceramic 3D printers
SLS 3D printing materials
SLS is another major 3D printing technology, using a laser to melt polymer powders into the final part. It’s less accessible than FDM and resin 3D printing, but is used heavily in prototyping as the final SLS parts are tough, durable, and do not require supports.
Nylon PA12
Nylon 12 is a commonly used SLS 3D printing material that’s tough, able to handle hard impacts, and generally durable. It’s used heavily for prototyping tough parts that may require functional testing, as well as some end-use parts.
It’s relatively low cost, has good precision, and good chemical resistance. PA12 3D printing materials also have a fairly grainy appearance, though they can be polished and dyed.
Nylon PA11
PA11 is similar overall in characteristics to Nylon PA12, but is more elastic and flexible, making it better suited to parts that require added impact resistance and elongation.
It’s also biocompatible, making it useful for medical applications. PA11 is also used in orthotics and prosthetics, hinges, and some sports equipment applications.
TPU
TPU 3D printing materials function similarly to how they did as FDM filaments — they’re flexible, rubbery and offer great impact resistance.
TPU materials are used in consumer goods, prototypes for flexible end-use parts like hoses, and in creating impact resistant parts of shoes and sneakers.
Metal 3D Printing Materials
Although less accessible and still very expensive, 3D printing has seen huge growth in the printing of metal powders via methods like Direct Metal Laser Sintering, Electron Beam Melting, and Directed Energy Deposition. Here are some of the commonly used metal 3D printing materials:
Stainless Steel — 316L, 17-4PH
Different types of stainless steel material are used in 3D printing, with slightly different applications.
Stainless steel 3D printed parts are used widely in the oil and gas industry for parts, as well as in the aerospace and automotive industries, such as where parts need to have excellent corrosion resistance while being cost effective.
It’s also good for machining, is cost effective, and overall has good mechanical properties.
Aluminum
Aluminum is a 3D printing material known for being very light weight, which makes it ideal for lower cost lightweight prototypes.
This lightness also makes it attractive to aerospace, where saving even a few grams can save thousands of dollars over a year of constant flying. Aluminum is strong, very easy to work with using machining, and has good thermal resistance.
Nickel — Nickel alloys 625, 718, K500
Nickel alloys aren’t magnetic, giving these 3D printing materials interesting niche uses fuel system components, rocket engines, and turbine engines.
Nickel parts are strong, very thermal and corrosion resistant, so are used in high heat parts in the oil and gas industry as well.
Titanium — Ti64
Titanium is lightweight, yet extremely strong, has great mechanical properties, is corrosion resistant, and can be used in medical uses as it is biocompatible. It’s often used in motorsport, and in the aerospace industry for engine and other parts. Due to its biocompatibility, titanium is also used in implants, and EBM also prints titanium parts.
Cobalt Chrome
This alloy has great mechanical properties, and it’s very resistant to corrosion and heat. It’s often used in the dental industry, such as to create custom crowns and bridges, but it’s also used in radiation shielding, casting, and many other applications.