
Direct Drive vs Bowden Extruder Comparison Guide

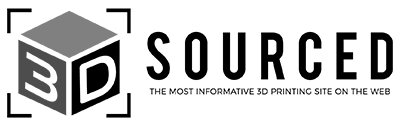
At 3DSourced we’ve covered everything 3D printing and 3D since 2017. Our team has interviewed the most innovative 3D printing experts, tested and reviewed more than 20 of the most popular 3D printers and 3D scanners to give our honest recommendations, and written more than 500 3D printing guides over the last 5 years.
Direct Drive and Bowden are among the two most common terms you’ll stumble upon when shopping around for FDM printers.
The lexicon attached to 3D printing isn’t for the faint of heart. Jargon and acronyms can leave beginners and even those with some 3D printing experience under the belt bewildered.
What do they mean? How do they affect the print process? What about print quality? And, more pressingly, which one is better?
We’ll tackle these questions and more in this direct drive vs. Bowden extruder comparison guide.
Direct Drive and Bowden Extruder System Definitions
When we talk about direct drive and Bowden, we are referring to the extruder system, specifically the mounting location of the extruder and how this affects how it feeds filament into the hot end. They serve the same basic function but come with their own set of benefits and downsides.
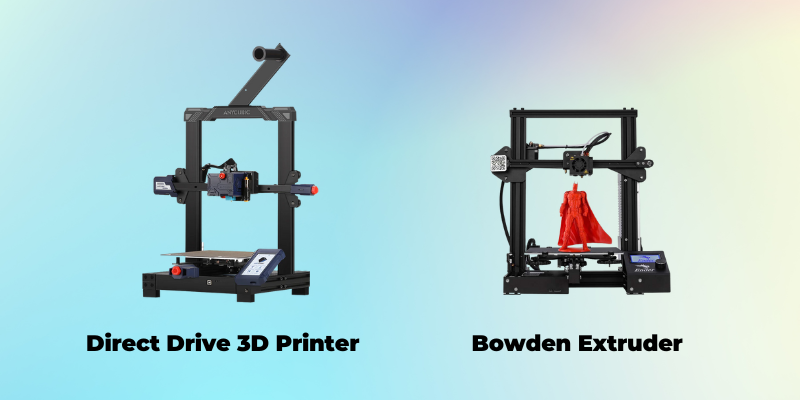
What Is a Direct Drive 3D Printer?
In a direct drive system, the extruder is attached to the print head assembly and feeds filament directly into the hot end, hence the name ‘direct’.
A direct drive system has a much shorter path between the extruder and the hot end, but the print head has to carry around more weight.
Popular direct drive printers: Anycubic Kobra, Prusa i3 MK3S+, Artillery Sidewinder X1
What Is a Bowden Extruder?
In a Bowden extruder setup, the extruder is generally mounted away from the print head, typically on the printer’s frame.
The extruder feeds filament to the hot end through a lengthy cut of PTFE tubing, known as a Bowden tube, hence the name. Consequently, the path between the extruder and hot end is much longer with a Bowden extruder, but the print head weighs much less.
Popular Bowden printers: Ender 3, Voxelab Aquila, Anycubic i3 Mega S, Prusa MINI+
3D Printer Direct Drive vs Bowden
Now that we have a basic understanding of what sets these two extruder setups apart, we’ll explore their pros and cons:
Speed
With a Bowden setup, the extruder is fixed to the frame, which reduces the weight load on the print head. A lighter print head translates to smoother travel movements.
With more efficient acceleration/deceleration and less jerk, the printer moves with more precision and is less prone to layer inconsistencies. Cleaner surfaces and less ringing at higher print speeds are also a benefit.

With less weight on the print head, Bowden printers tend to be quieter as the stepper motors don’t have to work as hard during travel movements.
The extruder is attached to the print head assembly on a direct drive setup. The printer has to work harder to deliver travel movements while also contending with more pronounced vibration, overshooting, and wobble, which can affect print quality and accuracy at higher speeds.
Though present, these issues can largely be sidestepped with correct slicer settings and printer tuning. But, direct drive printers don’t offer the same quality at higher speeds as Bowden extruders.
Extrusion
Due to the location of the extruder on the print head assembly, a direct drive system controls extrusion far better than Bowden systems.
This results in better responsiveness and less force required to push/pull the filament through the hot end. A by-product of this is that a direct drive extruder requires much less extruder stepper motor torque and less aggressive slicer settings to perform well.
On the other hand, a Bowden system offers less precise and responsive extrusion control, and requires more motor torque to move the filament. This is due to the longer filament path and the added resistance, or friction, caused by the filament running through the PTFE tubing.
This results in a lag, or a delay, between extruder actions and movement in the hot end. Common issues are stringing, oozing, and other extrusion-linked problems.
Retraction
Retraction is the name given to the action of the extruder pulling the filament back into the hot end during travel movements. It ensures filament isn’t pushed through the hot end as the print head moves over non-print areas and reduces unsightly oozing and stringing, which can affect the finish and overall quality of prints.

Direct drive systems provide much better and faster retraction performance because the extruder is located closer to the hot end. It doesn’t have to work as hard to retract the filament, resulting in finer retraction control, which reduces stringing.
In many cases, 3D printers with direct drive systems function well with very low retraction settings.
A Bowden extruder has a much harder time delivering accurate retraction. It has to work harder to pull back the filament through the tube, which can also rub against the filament, causing resistance.
Retraction is, therefore, slower, less responsive, and needs more extreme in-slicer tuning to perform well.
Flexible Materials
One of the major benefits of a direct drive extruder is how well suited it is to printing flexibles and abrasive materials, notably TPU. The more precise filament control, better retraction, and much shorter filament path make it so that there’s less potential for things to go wrong, unlike Bowden systems.
Due to the flexible or abrasive properties of the materials, they are particularly prone to jamming and clogging as they wear, bend, and bind. These issues are heightened as the filament passes through the long Bowden tubing, affecting the extruder’s grip and, therefore, its ability to control the flow of filament correctly.
A common manifestation of a Bowden system struggling with materials other than PLA and ABS is excessive oozing and stringing, the latter producing wispy strands of filament on prints, which require substantial post-processing.
Though optimal settings and printer mods can mitigate the problem to a certain extent, there’s no way to avoid the problem entirely with a Bowden extruder. As such, if you’re planning to work primarily with flexibles, you’ll want a direct drive printer.
A well-tuned Bowden 3D printer is more than up to the task of printing PLA and ABS.
Recommended Direct Drive Extruder and Bowden Extruder Upgrade Kits
Direct Drive

E3D Hemera Direct Drive Kit – A complete direct drive upgrade suitable for a broad range of printers, including the ever-popular Ender 3. E3D is one of the most respected manufacturers of hot ends, nozzles, and extruders around, so you’re buying quality. The E3D Titan is worth a look as well.
Micro Swiss Direct Drive Kit – Another excellent direct drive upgrade kit from a big name in the printer part market. It comes with Micro Swiss’ highly-respected all-metal hot end as a bonus and a dual-drive train.
Petsfang – If buying a kit isn’t your cup of tea, there’s no shortage of DIY paths to a direct drive system. Among the best is the highly-respected Petsfang. Much of the project is 3D printed, which should keep costs significantly lower than buying a kit.
Bowden

Capricorn Bowden Tubing – A simple and cost-effective upgrade, buying a Capricorn-branded tube, known for its extra lubrication and the quality of the PTFE, is the easiest way to perk up a flagging Bowden system.
Bondtech BMG Dual Drive Extruder – Stock extruders on low-cost printers can be hit and miss; some even use plastic to cut costs which can affect drip and speed up wear and tear. You can easily upgrade to a more reliable and robust part such as the Bondtech BMG Dual Drive Extruder. It’s lightweight, has an excellent 3:1 gear ratio, and is easy to install.
FAQs
Does Direct Drive Help With Stringing?
Yes, a direct drive extruder drastically reduces instances of stringing. The extruder requires much less force to push and pull the filament because the path between it and the hot end is much shorter, reducing noticeable delay or lag when extruding and retracting. Better and more precise filament control means less stringing.
Is Direct Drive Really Better Than Bowden?
Not necessarily; it all depends on your preferences, how willing you are to tune slicer settings, and what type of material is being used. Direct drive is unquestionably better for flexibles as these can’t bend, snap, or wear away in the long tubing on a Bowden extruder system. But, if you’re using PLA or ABS and want faster print speeds with a lesser impact on overall print quality, Bowden is arguably a better option.
Should I Upgrade to Direct Drive Extruder?
A direct drive upgrade is highly recommended if you’re planning to print flexibles such as TPU. A well-tuned direct drive extruder can all but eliminate stringing, one of the main issues plaguing Bowden setups. There’s also the added benefit of better retraction control, which reduces other extrusion-linked problems.
Is a Bowden Extruder Better?
Once again, better is subjective, and the answer depends on what material you use most. For flexibles like TPU, direct drive is uncontestedly better in most cases, while PLA/ABS performance is on par for both systems. Bowden extruders tend to handle higher speeds better, but direct drive extruders offer more precise filament control and better retraction.
Other related articles: