
How 3D Printed Prosthetics Can Change The Lives of Millions of Amputees

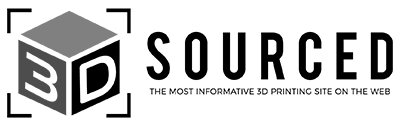
At 3DSourced we’ve covered everything 3D printing and 3D since 2017. Our team has interviewed the most innovative 3D printing experts, tested and reviewed more than 20 of the most popular 3D printers and 3D scanners to give our honest recommendations, and written more than 500 3D printing guides over the last 5 years.
Around 1 in 1,900 newborns in the USA are born with a limb reduction deficit, and there are an estimated 30 million people worldwide who need need a prosthetic. Of those, less than 20% actually have one. Even in the USA, the richest and most powerful country in the world, many don’t have replacement limbs due to the prohibitive costs. Despite this, around 200,000 amputations are performed in the USA per year, leaving many with stumps who struggle to live as they used to. But 3D printed prosthetics offer a potential solution.
These difficulties are seen most widely in poorer countries, where those who are born or who acquire a disability struggle to find adequate care. There is a shortage of 40,000 trained prosthetists in poorer countries, and even for amputees who have access to a prosthetist, there are issues such as time and money. They may need to traverse the long distance to the technician, and once they get there it can be a week-long procedure to assess the patient’s needs, produce a prosthetic, and fit it. Most cannot be away from their peers or children that long. Some cannot be gone for a day without losing their livelihoods and source of food.
There is therefore a problem. Traditional prosthetic technologies are leaving a gaping wide gap in those who need a prosthetic, and those who have one. They fit great when completed, but are expensive, have long lead times, and need to be replaced if the receipient is still growing.
Traditional Prosthetics: The Problem
Modern prosthetics involve inserting the limb, such as an arm, into a silicone sleeve and using straps to hold it in place. The traditional process of creating a custom fitting prosthetic involves wrapping the stump in plaster to make a reverse mold, before letting it dry.
Then, fill this reverse mold with more plaster, and leave it to harden. A socket can then be made from this that fits, after additional modifications for precision, to the bone on the stump. It’s not a simple process by any means — care is required to avoid tender areas or nerves — and the process can take over a week due to the three days of physical therapy involved in the fitting.

To add to this, there’s the cost. These are one-off, custom made pieces made from polypropylene, acrylics, and polyurethane, as well as a pylon made of either aluminium of carbon fiber. These are not cheap, and the fact they are made as a one-off rather than mass-produced only rocks the boat further. The cost of a traditional prosthetic is estimated to cost between $1,800 and $8,000, and they must also be replaced every five years, with children requiring replacements within two.
There are three key points here. One is time, one is cost, and one is accessibility. Prosthetics struggle in all three areas. How do 3D printed prosthetics differ here?
3D Printed Prosthetics: The Solution
Rather than spend a week with a technician to perfectly tailor a prosthetic, a 3D scanner can do all this work under 15 minutes, and the resulting scan sent across the world, to be 3D printed or analyzed, in seconds. What’s more, there are 3D printed prosthetics that can be made in a variety of colors such as to match the patient’s skin tone, and for less than $30.
Once the 3D design of the prosthetic has been tailored, you can keep the STL files forever. This means that if you fit a five-year-old with a 3D printed arm prosthetic, and he grows out of it, you can revisit the file and scale it up for them. 3D printed prosthetics literally grow with you. This makes 3D printed prosthetics for children a perfect solution.

How 3D printed prosthetics are already changing lives
In Jordan, the increasingly unstable climate in Syria and the Middle East has led to a rising number of refugees coming into the country, many with amputated limbs. The amount of people in this situation means the time that it would take to fit all these people with prosthetics is unfathomable, and therefore drastic measures had to take place.
One particular hospital in Jordan began trialing 3D printing in prosthetics to treat these refugees, many of whom carry serious mental issues and trauma as well as their physical injuries. Rather than spending a whole week creating the prosthesis, these 3D printed prosthetics can be created from scratch in 24 hours, seven times more efficiently than traditional techniques. Médecins Sans Frontières (Doctors Without Borders) are therefore trialing 3D printing to crate prostheses, with a view of applying it worldwide if the results come back positive.

Advantages of 3D printed prosthetics
Irrespective of the speed advantages, there are a number of other reasons why 3D printed prosthetics may be the future of the industry. When a person loses a limb, their problems span beyond the loss in ability from that limb’s use in everyday functions; there are also issues in balance, center of gravity, and ergonomics that come from a sizable weight no longer being present. 3D printed prosthetics can be made to weigh the same as the child or adult’s other arm or leg, leading to improved posture and balance, and also helping the spine.

3D printing has already seen use in areas such as knee replacements, as well as jaw surgeries via 3D printed surgical guides. There is no reason why its usefulness should stop there, and prosthetics seem the ideal area for 3D printing to help improve peoples’ standards of living. What’s more, if 3D bioprinting and 3D printed organs are possible, leading to 3D printed hearts in the future, then creating workable limbs seems simple in comparison.
The low barriers to entry and costs of creating 3D printed prosthetics for those in need led a number of makers and tinkerers together via the common goal of doing good. If you need a reason to re-believe in humanity, this is it.
Most 3D printing materials cannot support the entire body weight, so the vast majority of 3D printed prosthetic research and design has focused on 3D printable hands and arms.
Limbitless Solutions
Limbitless Solutions is a non-profit in Orlando, Florida working on creating incredibly advanced 3D printed prosthetic arms and hands for children with a limb reduction. They build myoelectric prostheses (prosthetic arms that use electrical impulses generated by muscles to move like a real human limb would) including ABS filament 3D printed parts to save on costs and increasing customization for wearers.
Limbitless’ 3D printed prosthetic hands have EMG sensors on the wrist area that directs the hand based on muscle signals, with a battery in the arm that powers the hand, and individual joints for each finger that gives the hand full-finger dexterity. Each 3D printed prosthetic is sketched out before it is designed on a 3D CAD software tool (Limbitless Solutions use Maya and Fusion 360), before the wearer customizes the design online based on what they think will look best. The custom parts are printed based on the wearer’s custom measurements that are taken, and then these parts are sanded, smoothed, painted and programmed with the EMG sensors so they can be used by the children who need them most.

This fantastic initiative is currently raising money for a clinic trial involving 100 children receiving custom 3D printed myoelectric prostheses, and have raised enough for 62/100 as of August 2020. Beyond 3D printed prosthetic hands, Limbitless also research how to help wheelchair-bound and ALS/MND sufferers operate wheelchairs using EMGs, and other important projects.
However, these are still expensive, even if 3D printing reduces the prosthetic cost, namely due to the sensors and electronics. For very cheap and simple enough to build at home prosthetics, E-Nable are doing great work.
Enabling The Future
Enabling The Future was born accidentally, and out of bizarre circumstances. Back in 2011, Ivan Owen made a functional metal hand (which looks amazing, by the way) for a steampunk convention, of which a video was found by Richard, a carpenter across the world in South Africa.
Richard had lost his fingers in an unfortunate woodworking accident, and got in touch with Ivan about creating bionic fingers for him in the same vein as his steampunk costume. Communicating over Skype and email, they worked to create this ambitious model to restore some of Richard’s livelihood. This then led to another encounter with Liam, a five-year-old boy also from South Africa who was too missing his fingers on his right hand.
Jorge Zuniga, who works in the biomechanics department at the University of Nebraska in Omaha, heard about the project. He put his vast mechanical skills into use and studied the human hand to create a workable model that looked and functioned like a human hand. Pleased with his progress, he gave the prosthetic to his young son, expecting glowing feedback. His son looked at him, disappointed. He didn’t want a hand that looked like a hand, he wanted it to look like a robot.

It is so easy for adults to forget the innocence, childlike wonder and curiosity young people possess, and adults seek to protect. This was an eyeopener; adults are used to trying to blend in when they have something considered abnormal like a missing limb, whereas children love cool things that stand out.
Jorge Zuniga went back to the drawing board, and emerged with the next iteration of his 3D printed hand project. It purposely looked like a toy, and made a bold statement rather than merely trying to mimic the human hand. He called it the Cyborg Beast, a suitably loud name. Since its release online, there have been over 50,000 downloads as of last year, and there are thought to be several hundred Cyborg Beasts in action across numerous countries.

It didn’t stop there however. A community rallied around these 3D printed mechanical hands, and 3D prosthetic designers actively encouraged people to design their own improvements, as per the open source ethos. Motivated by doing good and improving people’s lives, the Enabling The Future community has grown to over 20,000 members across dozens of countries, offering access to over 2,000 3D printers that have delivered over 8,000 arms and hands for those in needed. Many of the hands made are for children.
A case study: Natasha Hope-Simpsons’s 3D printed prosthetic leg
Rather than feeling robbed of a limb as a result of being hit by a car, Natasha Hope-Simpson viewed the situation artistically: she had inherited a large amount of negative space to put to use. At NSCAD University, in collaboration with 3D Systems using their ProJet 7000 SLA 3D printer, the team managed to go from the first 3D scan, to a fully manufactured and working 3D printed prosthetic in just 17 days back in 2014.
Not only was this a functional and working prosthetic, but it looked fantastic. The design was inspired by Melissa Ng’s designs for her brand Lumecluster, and was used to create a futuristic, elegant and radiant prosthetic. Not only does this show 3D printing as an alternative to traditionally-produced prosthetics, but highlights its ability to make improvements, allowing for intricate and attractive new designs that were not considered a possibility before. Something functional was turned into something beautiful, and customization was brought to a previously standardized industry.
Types of 3D printed prosthetic
A number of different 3D printed prosthetic hands have been created and are hosted on the Enabling The Future website. The most notable of these are the Cyborg Beast, Phoenix Hand, Raptor Reloaded, Team Unlimbited Arm, Osprey Hand, Talon Hand 2.X, and the Knick Finger. They each serve different functions depending on the basis of each person’s disability and aesthetic preference.
Here are a few of the most interesting designs:
Phoenix Hand — 3D printed prosthetic hand
Enabling The Future’s Phoenix Hand comes in three different versions, and requires a functional wrist with enough palm to press, with enough force, the fingers closed when the wrist is bent. If you don’t have a functional wrist, there are other options out there for you such as the Unlimbited Arm.

Unlimbited Arm — Entire 3D printed prosthetic arm for wrist amputees
Instead of being driven by the wrist as in with the Phoenix Hand, the Unlimbited Arm is elbow driven. Users of the Unlimbited Arm need to have a functional elbow that bends to force the fingers closed on the 3D printed hand. It was created for those with a functional elbow and some forearm, but no wrist.

Knick Finger — 3D printed prosthetic finger
Rather than being a 3D printed hand or wrist, the Knick Finger is for those who are missing a finger, or at least two finger segments. The Knick Finger works in a similar way to the Cyborg Beast or Phoenix Hand, just with one finger rather than the whole hand, and is completely adaptable for each person’s finger. Each component can be 3D printed separately based on the individual’s needs.

Problems with 3D printed prosthetics
We mentioned earlier that there were some problems with 3D printed prosthetics, and they aren’t perfect. Whilst they show significant promise, there are some issues that definitely need to be ironed out before they can be reliable called the future of prosthetics.
3D printed prosthetic materials break easily
The 3D printer materials used in creating 3D printed prosthetics is usually ABS or Nylon. These are both thermoplastics which, whilst being strong enough for most 3D printing needs, struggle with the task of supporting an amputee’s needs, day in and day out. They are also printed in very thin layers, and so can break when forced the other way than they are used to bending.
Unsuitable for 3D printed prosthetic legs
Most 3D printer filaments and materials are simply not strong enough to support a human’s body weight. Though the Exo Prosthetic design prototype in 2015 showed potential, this would be 3D printed in titanium, an extremely strong yet lightweight metal that can only be printed on industrial 3D printers that cost upwards of $100,000. This takes 3D printed prosthetics from accessible parts that can be built on cheap 3D printers, and moves them back into professional, industrial products.

It takes time to train prosthetic technicians in 3D printing
Creating prosthetics is an acquired skill, to be performed by an artisan. Therefore, it takes time to train somebody to be able to reliably create 3D printed prosthetics that won’t break almost immediately. Learning how to do things such as regulate the temperature when 3D printing prosthetics to avoid cracks forming takes time to master.
Products are not FDA approved
Whilst not the biggest deal ever, it is worth noting that these homemade 3D printed prosthetics are not regulated, and exist outside official ruling. It’s not currently an issue, but it may be moving forwards.
How to build your own 3D printed prosthetics
Unless you plan on designing your own innovative prosthetics from scratch, if you want to help create 3D printed prosthetic hands and arms, you should head to the E-Nable Volunteer page.
They have extensive guides showing how their 3D printed prosthetic hands are made, and you can either 3D print all the prosthetic components yourself and then buy the other components and start building, or buy 3D printed hand kits featuring all the extras you’ll need, already sourced for you.
Things you’ll need:
- An FDM 3D printer, with at least 6″ x 6″ build volume for the largest parts.
- PLA filament to 3D print the prosthetic parts
- The additional components, which you can either buy as a full kit, or source them individually here
Conclusion
To conclude, as with many other areas, 3D printing offers fantastic benefits, if the issues can just be ironed out. On a positive note, there are already working 3D printed prosthetic prototypes out there, which is far more advanced than in 3D bioprinting where much of the work is still theoretical.
There have been attempts to create a prosthetic with 3D printing that much more closely mimics the texture and feel of a human hand. It was printed in a material called filaflex, and looked far more realistic. The downside is that it cost $2,000, comparable to traditional prosthetic prices. This is a far more than the E-Nable $40 solutions, though the fact that it is possible to create realistic limbs using 3D printing, coupled with the assumption that technological improvements assumes costs will come down, means that there may be a bright future in 3D printed prosthetics.